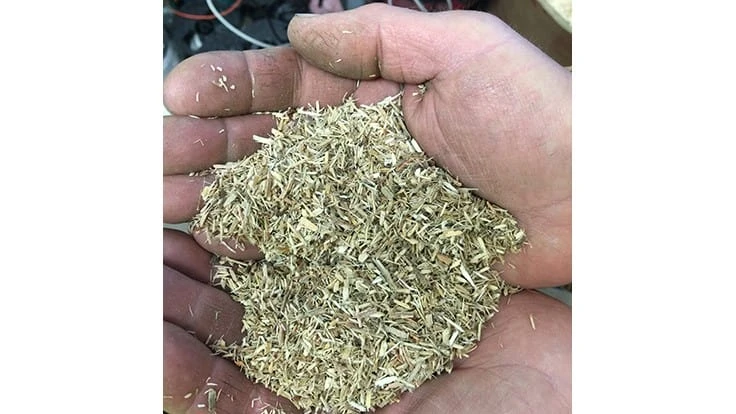
Photo provided by West Salem Machinery.
Oregon-based equipment provider West Salem Machinery (WSM) and its president Mark Lyman say the company’s approach of “providing innovative solutions to convert waste and residuals into the desired finished product in an efficient and cost-effective manner” is keeping it on the front lines at many recycling operations.
“We optimize machines through real world testing; our test lab can simulate various production settings and volumes,” says Lyman. “Our machines start with the same field-proven designs we’ve been building for years and are working hard around the world – right now. Every machine we build is built to the requirements of the customer. Machines are optimized based on what the machine must process.”
Lyman says listening carefully and asking thoughtful, detailed questions helps the WSM team zero in on the machine or system requirements of its customers. “Every application has its own idiosyncrasies, and getting the details right makes all the difference,” states the company.
WSM says its vibrating screens are deployed in applications involving biomass, laminated veneer lumber/plywood trim, particleboard furnish, sawdust/shavings and urban scrap wood recycling.
Its newly redesigned Oscillating Super Screener moves material four times faster than traditional “chip” screens and has less mass for a longer operating life, adds the company. Typical materials processed with these screens include animal bedding, bark, board furnish, mulch, sawdust/shavings, trim ends and wood chips.
WSM’s disc scalping screens including its Waterfall Disc Screen, typically have a smaller, low-cost footprint and smooth, low speed operation,” states the company. Its Titan Trommel Screens, meanwhile, can undertake separation tasks on compost, food waste, landscape products, hog fuel and soil amendments.
The company’s grinder product portfolio includes horizontal and vertical feed units, and low-RPM and high-speed models. WSM describes itself as a leading manufacturer of screening and size reduction machinery.
Latest from Construction & Demolition Recycling
- IDTechEx sees electric-powered construction equipment growth
- Global steel output recedes in November
- Canton, Ohio, nonprofit helps divert building materials for reuse
- Ferrous market ends 2024 in familiar rut
- NDA to offer certification test at convention
- Hyster-Yale commits to US production
- World Cement Association highlights challenges facing long-term cement demand
- Tata Steel to supply equipment maker JCB