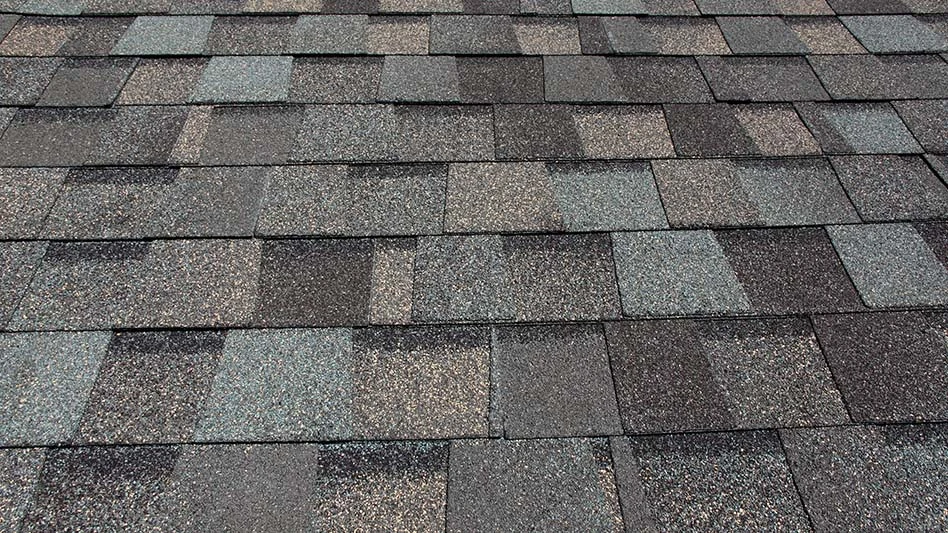
Photo from C&DR photo archives
Last year, Owens Corning, a Toledo, Ohio-based construction materials company, launched a recycling pilot facility for asphalt shingles in Indianapolis. The company says the pilot will drive its work to reclaim asphalt shingle components and repurpose the raw materials into new shingles.
The pilot was launched with ASR Systems, a producer of recycled asphalt shingles based in Barrington, Rhode Island; CRS Reprocessing Services, an industrial fluid and solid material management company based in Louisville, Kentucky; and Indiana Shingle Recycling, based in Indianapolis. Owens Corning says its goal is to recycle 2 million tons of shingles annually in the U.S. by 2030.
Construction & Demolition Recycling recently spoke with Mark Leo, Owens Corning’s director of circular economy, about the pilot program, the partnership that made it possible and the company’s circular economy goals.
C&DR: Can you explain what the pilot project seeks to do?
Mark Leo (ML): Owens Corning, with ASR Systems and CRS Reprocessing Services, is piloting a way to break down shingles into their components and utilize those components to produce new shingles and other products. While this work has been proven at a lab scale, the construction of the pilot on the grounds of Indiana Shingle Recycling is the next step toward commercialization.
While this work has been proven at [a] lab scale, the construction of the pilot on the grounds of Indiana Shingle Recycling is [the] next step toward commercialization.
C&DR: What role does Indiana Shingle Recycling play in this pilot?
ML: The deconstruction of postconsumer and postindustrial shingles into their individual component raw materials is being done on the grounds of Indiana Shingle Recycling in Indianapolis. This is a longstanding site for the collection of waste shingles, and additional equipment and facilities associated with the pilot have been constructed within Indiana Shingle’s existing footprint. The raw material outputs from the shingle recycling process will be transported to Owens Corning’s existing manufacturing facilities where they will be tested in producing new shingles made with recycled content.
C&DR: What are ASR and CRS’ responsibilities in this pilot?
ML: ASR Systems and CSR Reprocessing Services are key partners in this effort. ASR provides expertise in mechanical shingle deconstruction and a patented raw material recovery system for asphalt shingles. CRS Reprocessing uses solvent-based recovery technology to process the shingles into usable base components. Both methods of recovery are being used in Owens Corning’s shingle recycling system.
C&DR: Where do you source the materials for this pilot program?
ML: Indiana Shingle Recycling is an ideal partner in this effort due to its longstanding relationships with roofing contractors who bring tear-off shingles to the facility for recycling. Materials are supplied by contractors local to the facility [in and around Indianapolis].
C&DR: How are shingles separated from other materials prior to being fed into the recycling system?
ML: The first step of the recycling system is a mechanical grinding process. This process can accommodate shingles of different ages, shapes and manufacturers. Before entering the system, Indiana Shingle Recycling completes quality checks on the input material to ensure no foreign objects like wood, gutters or more are in the input stream. Any contaminants are removed with industrial equipment or by hand.
C&DR: What kind of equipment is used in the process?
ML: CRS Reprocessing Services and ASR Systems manage and operate custom equipment used by their respective proprietary processes. Owens Corning is using its manufacturing equipment for processing recovered asphalt, blending and preparing recovered materials for testing in shingle production.
C&DR: How many shingles is the pilot expected to recycle annually?
ML: The nameplate capacity for this pilot is 2,000 tons per year. The pilot was designed to be large enough to be representative of a full-scale facility and to produce enough material to qualify the output products for incorporation into shingle manufacturing and other applications. The knowledge gained from the pilot phase will be a key driver of the ultimate design of commercial-scale facilities.
C&DR: What must be done for this pilot to be considered a success?
ML: Our experience in building circular economy models has taught us that for a concept like this to be successful, every node in the ecosystem must be motivated and incentivized to participate. From the input feedstocks through the supply chain and end users, we must prove that this model is robust enough to stand on its own. Our strategy here is to partner with the leaders and innovators in the ecosystem and work together to determine what must be true for this concept to be viable, and we’re all relying on each partner to manage progress toward achieving the milestones associated with each piece of the puzzle.
C&DR: What are Owens Corning’s goals for a circular economy in shingle recycling?
ML: Owens Corning’s mission is to build a sustainable future through material innovation. This includes transforming our operations to a circular economy model. In 2020, the company established a circular economy team to define goals and prioritize projects that accelerate our circular economy ambitions. That team is leading collaborative work across the company to help [it] become net positive—where our handprint is bigger than our footprint.
Our 2030 goals for the circular economy include establishing viable circular economy business models involving our materials and how they are used. Our approach to our circular economy business model includes:
- avoiding the use of virgin raw materials whenever possible;
- sourcing materials and serving customers in ways that minimize transportation and its impact;
- manufacturing products in ways that reduce the amount of waste generated and ensure the least negative environmental impact; and
- ensuring that materials used in our products and packaging remain in the economy indefinitely.
More information about our approach is detailed in our annual sustainability report on our website.
C&DR: Are there plans to expand this pilot program in the future?
ML: The end goal of this work is to scale this process efficiently across our entire asset network, which allows Owens Corning to offer recycling solutions and recycled content products in all our markets. Beyond that, we are open-minded about a potential future where we share our capabilities within the asphalt roofing industry and adjacent spaces. Time will tell.