
Since 1867, The United States Playing Card Company (USPCC) has been one of the world’s leading designers and manufacturers of playing cards. From 1899 until 2009, the company manufactured many of its iconic brands of playing cards including Bicycle, BEE, Aviator and Aristocrat at its Norwood, Ohio-based headquarters located just outside Cincinnati.
Then, in 2009, the company made the decision to move to a new 570,000-square-foot state-of-the-art headquarters in Erlanger, Kentucky.
With the former site abandoned, many potential uses for the factory were explored over the next decade. Then, in 2019, a developer acquired the 21-acre property with the ambitious goal of investing $100 million to convert it to a mixed-use development site.
To perform remediation and demolition work on the now-obsolete factory, the developer selected Cincinnati-based O’Rourke Wrecking in February 2020.
According to Mike O’Rourke, president of O’Rourke Wrecking, the company’s extensive history working on projects with a similar scope made it a perfect candidate to tackle the USPCC job.
“The developer relied upon O’Rourke’s 58-year repository of vast demolition and abatement experience to devise and implement a site-specific environmental, demolition and site safety plan that was unique to the challenge of abating and demolishing multiple buildings with integral buildings and structures that had to be segregated and protected under a fast-paced schedule,” O’Rourke says.
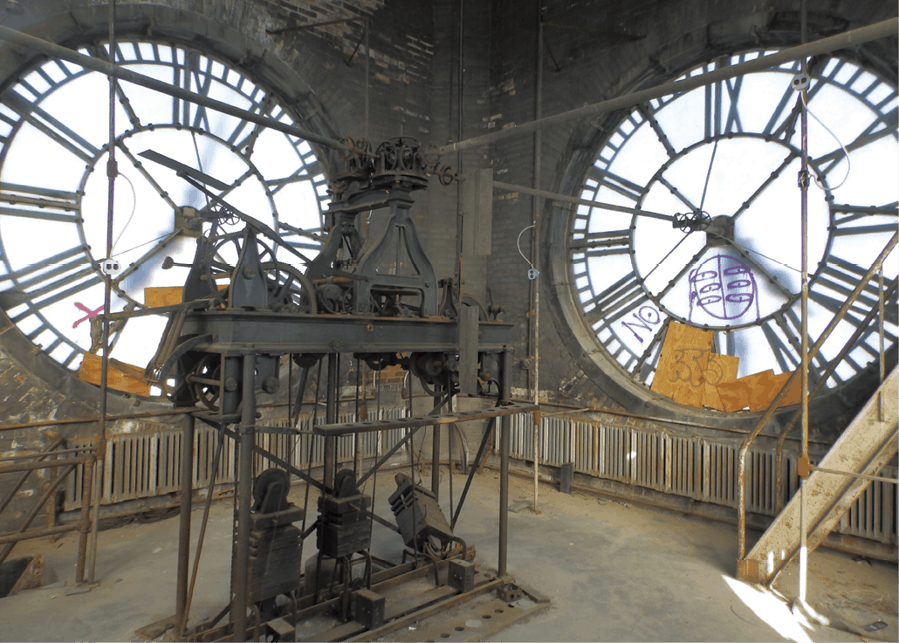
Getting to work
Construction of the former USPCC headquarters began in 1899 and continued into the 1920s. The result was a group of interconnected structures primarily of wood post and beam construction while the newest buildings were constructed of reinforced concrete. Steam for heat was supplied by the boiler house on-site through a system of below-grade steam tunnels.
One of the primary challenges O’Rourke had to navigate was preserving the site’s historic clocktower, which is listed on the National Register of Historic Places, as well as its smokestack, in order for these structures to be incorporated into the new site redevelopment.
Another challenge was dealing with the old factory’s asbestos-containing materials.
O’Rourke crews of around 20 began work in March 2020 to abate the large amount of regulated asbestos-containing material on-site. The largest area of concern was the boiler house that had two coal-fired brick boilers and a labyrinth of below-grade steam tunnels that contained thousands of feet of asbestos-containing piping.
In all, crews identified asbestos-containing thermal pipe and fitting insulation, mudded fittings, boiler breeching and tank insulation, cementitious (transite) panels, wire rope firestop material, fire doors, friable window glazing, electrical boxes and other components.
Once asbestos abatement progressed, a phased utility shutdown of the site began. This was critical, as most of the buildings were of wood construction and fire safety was a key concern.
Prior to the start of active demolition, O’Rourke also worked to install supplemental temporary fence panels and established general site security and access procedures to protect the site.
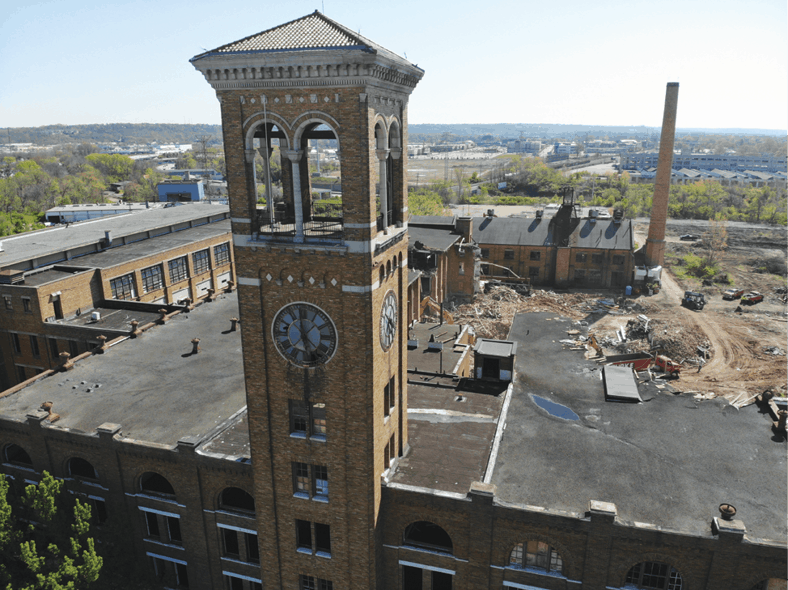
With the abatement and site preparation completed, demolition work was ready to begin. This would involve a combination of conventional mass demolition, ultra-selective dismantling and deconstruction, hand demolition, rigging, torch cutting and associated activities.
According to O’Rourke, being mindful of adjacent structures was one of the most pressing parts of preparing for the demolition.
“The USPCC site was situated in an urban setting with occupied businesses and neighboring facilities located in very close proximity to the demolition and construction work areas,” O’Rourke says. “Ongoing risks included general pedestrian, vehicular and construction traffic. Adjacent public sidewalks and streets were maintained and accessible during all abatement and demolition activities. … Special consideration and attention was expended with regards to protecting these adjacent facilities and site infrastructure scheduled to remain operational.”
O’Rourke relied on its extensive fleet of equipment to accomplish much of the demolition work. A Link Belt LS 208 crane with a clamshell bucket and wrecking ball, as well as five Caterpillar excavators with Genesis shears and grapples and JBR quick connects were the primary tools for the job.
The site structures were strategically demolished using the hydraulic excavators, which ranged from 70,000 to 150,000 pounds. The excavators equipped with the grapple attachments were used for initial structure takedown, post-secondary debris reduction and initial material segregation efforts. The excavators with shears were primarily used for scrap metal sorting, processing and sizing, and load-out.
For the ultra-selective demolition work needed to separate the old clocktower at the site, two four-men crews worked to hand demolish and isolate all buildings surrounding the structure in a floor by floor manner. Care was taken to segregate and recycle as much timber and floor planking as possible throughout the process. Over 250,000 board feet of timbers were salvaged from the structures. Also, the common brick from the facility was desirable, and approximately 750,000 bricks were cleaned and palletized for reuse. The bricks and wood were recycled and reused throughout the development and in other projects across the country. Additionally, 20,000 cubic yards of concrete was recycled and crushed from the project. O’Rourke says all waste generation, segregation, sampling and profiling, manifesting, transportation, and final disposal and recycling was monitored daily to assure compliance with, and adherence to, all applicable federal, state and local regulations.
O’Rourke also says that a waste tracking log was kept documenting all debris leaving the site to help verify the company’s waste and recycling footprint. In all, the company was able to recycle 90 percent of materials from the project.
“This project clearly demonstrated demolition as a ‘green industry’ in several innovative ways,” O’Rourke says. “We were able to recycle 90 percent of debris and clear a degraded and dilapidated plant while maintaining its history in preparation for new construction of a much-needed development [project]. At O’Rourke, we believe that there will always be a ‘tomorrow’ and our core business practices reflect this concern for the future. Our corporate sustainability goal is to reduce, recycle and repurpose or reuse materials whenever possible on all of our projects.”
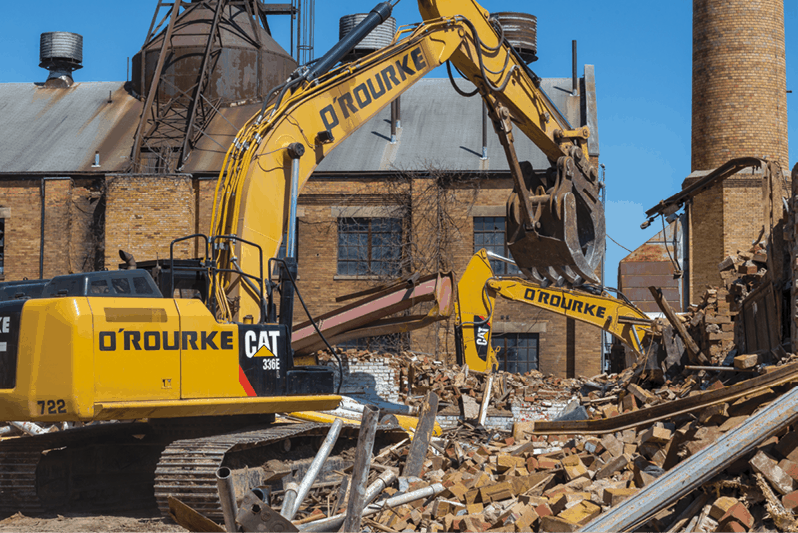
Looking back
O’Rourke says the company’s emphasis on safety was one of the most important aspects of the job.
“The health and safety of demolition employees, project management and oversight staff, various site visitors, adjacent facility activities and the neighboring general public was a critical consideration for the successful completion of this project,” he says.
The company met its safety goals, as the project, which was completed in September 2020, ended with no incidents or injuries. O’Rourke credits his detail-oriented crews for this achievement.
“By implementing a site-specific demolition strategy that focused on protection of adjacent properties and businesses, the general public and the surrounding environment, it made this project successful for both O’Rourke, and importantly, the owner. Our multi-layered demolition approach and top-notch crews delivered the site in a safe, efficient and timely manner and clearly exceeded industry standard practices and requirements,” O’Rourke says.
This article originally appeared in the Nov. Dec. issue of Construction & Demolition Recycling magazine. The author is the editor of Construction & Demolition Recycling magazine and can be reached at aredling@gie.net.
Latest from Construction & Demolition Recycling
- Bomag to showcase innovations on the National Mall
- NWRA, SWANA to partner on safety, education and advocacy
- Caterpillar announces collision warning system, other technology for medium wheel loaders
- ABC: Nonresidential construction adds jobs in April despite headwinds
- Demolition underway at former SC steel mill
- Turkey neglects US scrap in favor of Russian shipments
- Results of New Hampshire waste study reveal missed opportunities for diversion
- Alterra, Eco Materials open soil remediation facility in PA