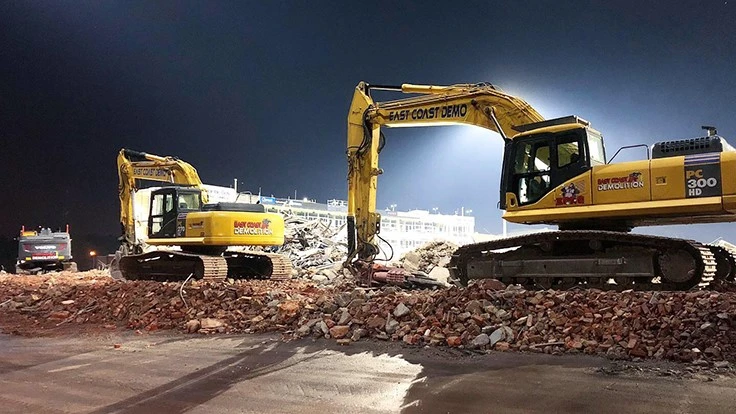
When word got out that Old Dominion University in Norfolk, Virginia, was going to demolish the iconic 82-year-old Foreman Field to pave the way for a new football stadium, demolition companies across the region bid for the job.
North Carolina-based East Coast Demolition was awarded the project, but there was a catch.
“They wanted to have one demolition company handle one side of the stadium and another company do the other,” East Coast Demolition Project Manager Richard Webb III says. “That’s when they told us one of our largest competitors in the area was going to be doing the other side.”
Macsons Inc., headquartered in Norfolk, Virginia, was tasked with tearing down the west side of the stadium. Shortly after fans watching Old Dominion’s final game against Virginia Military Institute cleared the stadium Nov. 19, the companies staged their equipment on-site.
With each contractor boasting more than 30 years of demolition experience, the companies say it wasn’t the size of the project that was a challenge, but the university’s timeline to complete the job. Because the university wanted the new stadium ready for the 2019 football season, the contractors had about a month to tear down Foreman Field, Webb says.
Proper prior planning
Weeks before the start date, Macsons Project Manager Andrew Dunnum coordinated between the company’s other job sites to make sure crews and equipment would be ready for the stadium teardown. Dunnum, who passes by the stadium every day on his way to work, says the company’s employees—many of whom have children who attend the university and go to the football games—felt a connection to the project.
Dunnum laid out 24-hour shifts for workers and planned which pieces of equipment would be used for each phase of the project. Meanwhile, Webb studied drawings of the stadium and calculated how to finish the project within 10 days of starting.
“Every project we do is to exceed the schedule that we put out. This one was no different, but it was one of the most important,” Webb says. “We knew if we ran 50 loads per day, we could move the building in 10 days.”
In planning meetings, Dunnum says Macsons founders Steve and Bill McCloud and Webb’s father, Richard Webb II, who helped found East Coast Demolition, talked like old friends.
“We had all our jokes,” Dunnum says. “‘We’re going to do [the demolition] faster than you’ taunts went back and forth, but at the end of the day, [Webb III] and I both knew to make this successful for the general contractor and Old Dominion, we had to work together as a team.”
No “I” in Team
Dunnum says that both contractors kept in close communication as they reached different phases of the demolition.
“It was actually kind of fun to have someone else in the same club as you are, just on the other side of the fence,” Dunnum says.
While East Coast Demolition and Macsons had the same goal, their approaches to the project were different. Macsons aimed to find a balance between speed and efficiency, while East Coast’s goal was to “get the building down and out.”
To bring down the stadium’s 80-foot walls, East Coast Demolition used a Volvo 480 high-reach excavator paired with a new NPK MP-28 processor, which allowed the company to reach heights of the stadium other equipment couldn’t while “providing the most efficient demolition method.”
Webb III says the company’s DustBoss also came in handy for managing dust from the project.
“Fire hoses don’t provide the best suppression,” he says. “Dust and silica dust is such an issue now, so having that DustBoss out there was a huge help to keep the dust down. We were dropping walls so fast, we had to have enough water to handle it.”
Macsons started in the middle with a Hitachi high-reach excavator and worked its way out with smaller excavators to bring down 10-foot walls on each side. In addition, Macsons had to tear down a media booth and salvage a locker room for reuse. Dunnum says volunteers from the college and community came to help salvage material, but for him, the best part of the job was that almost everyone in his company had a hand in it.
“We pulled some of our abatement guys off a job to help the demo guys out,” Dunnum says. “We told them, ‘You’re a part of the team. Please do your part. Push hard and keep your production up.’”
With residential neighborhoods nearby, noise was a big concern in the project. In fact, Webb III says he had to submit decibel readings from other projects prior to the Old Dominion teardown to show they could work at night; however, he says crews worked so efficiently that they didn’t have to worry about disturbances.
“We were prepared to run 15 guys during the day and 15 guys at night,” Webb III says. “But within the first night, we tore down a fifth of the stadium.”
Finishing the project in just eight days, Webb III credits his crews for staying on task.
“My team did a really good job of keeping the pace of the project without me having to be there every second,” Webb III says. “Our guys are self-sufficient. They knew what had to be done and they took over. They took pride in it and they did a really good job.”
A job well done
Macsons recycled approximately 7,230 tons of brick, concrete and asphalt; 70 tons of debris; and 116 tons of metal from the project. To speed up the job, Macsons’ recycling yard in Bowers Hill, Virginia, processed half the material, while an outside company handled the rest.
With a goal to “clean up as we go,” East Coast Demolition picked and sorted through different materials—aluminum, concrete and brick—to recycle throughout the project.
“Since recycling material reduces costs for disposal, we tried to recycle as much concrete, brick and asphalt as we could,” Webb III says.
Because of the stadium’s rich history and ties to the community, local media covered the project extensively. The university even set up a live webcam of the site to track its progress.
“People don’t always know exactly what we do, so seeing our company in the paper and people posting on social media was neat—especially since we were able to finish early,” Dunnum says. “It’s something you can take pride in.”
With construction of Old Dominion University’s new stadium underway, Dunnum and several other employees have kept a piece of Foreman Field as a token of history.
“I have a brick in the back of my truck bed that I’m going to hold on to,” he says.
The author is digital editor for the Recycling Today Media Group and can be reached at kmaile@gie.net.
Latest from Construction & Demolition Recycling
- Liebherr to exhibit at upcoming IRPT event
- CDE commissions C&D recycling plant for Freehaven Materials
- Midsummer sees flurry of scrap theft alerts
- Louisiana mall could be next on demolition list
- CDRA names new executive director
- Irock promotes service manager
- Vermeer offers new horizontal grinder
- LRS expands into Indianapolis with purchase of GHW