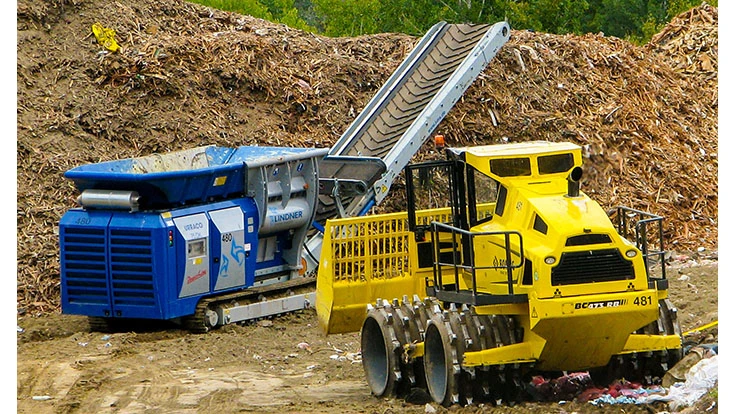
A Urraco 75 DK mobile shredder supplied by the Raleigh, North Carolina Lindner America office of Austria-based Lindner, with the instrumental help of its eastern Canada representative Recycling Equipment of Canada Inc., Waterloo, Ontario, has been on the job since early 2016 at a demolition and nearby landfill site in Ontario, Canada.
The unit has been set up to serve the decommissioning of the Chalk River Laboratories (CRL) site, which was operated by Canadian Nuclear Laboratories (CNL).
According to Lindner, the 75 DK has recently been onsite at the landfill to process noncontaminated waste, shredding wood, plastics and light materials from demolition, renovation and new building work. At the 40 square-kilometer (15.4-square-mile) site with around 160 buildings, the debris includes pallets, construction timber, trees and brush, asphalt, metal containers, plastic pipes and furniture, says Lindner.
In addition to “significantly reducing the volume of the waste,” Lindner says the Urraco is preparing the wood fraction into a compactible bulk product that can be mixed with regular landfill daily cover material and spread over the working face of the landfill at the end of every working day. The preparation of the alternative daily cover (ADC) helps CNL comply with a regulation to cover the waste collected during the course of a day with a 150-millimeter (6-inch) thick layer of wood and soil mixture, thus mitigating the need to bring soil just for this purpose.
CNL operates the 75 DK with a diesel engine and track system and with a nominal shredding capacity of up to 45 tons of wood per hour. James Betts, who is section head of waste management operations at CNL, meaning he is responsible for non-radioactive waste disposal, says, “Even now, we are shredding a volume of over 10,000 cubic meters (13,000 cubic yards) every year, but this is likely to multiply quickly as we expand our work. The mobile self-driving Urraco meets our requirements down to a tee. Its shredding performance gives us the necessary reserves, its track system provides the necessary mobility and its rugged construction means a minimum of maintenance and repair work.”
The Urraco shredder is equipped with a contaminant recognition system designed to respond within fractions of a second. Together with a reversing function, it is designed to protect the tools from damage and to reduce the wear and tear of the shafts and the stress on the drive system. Also standard is the discharge belt, the height of which can be adjusted by remote control through the hydraulic system. In the CNL installation, a magnet is positioned above it to extract nails and other metal components for subsequent recycling.
“The track system reliably prevents the machine from becoming stuck when we maneuver it with the remote control over the rough terrain,” says Betts. “The diesel is very well coordinated to the hydraulic system, which means that it consumes surprisingly little fuel when shredding. In addition, the control software switches it to eco mode with a much lower rpm if no shredding is carried out for a longer period of time. This reduces consumption even further. Especially for our region, where the temperatures vary from over 30 °C in summer to below -30 degrees Celsius in winter, it was also vital that this engine should be completely immune to the influences of the weather in practical operation. Our experience so far with the performance, reliability, operating costs and maintenance friendliness of the Urraco confirms our decision to select Lindner as our supplier without reservations.”
Adds CNL Supervisor of Clearable Waste Operations Jason Ziebarth, “Our Urraco meets the expectations we had of it not only from a technical point of view, as it has also proved absolutely user-friendly. Within a very short time [employees Jonny Layman and Ian Boudens] have become experts in handling the shredder.’
Latest from Construction & Demolition Recycling
- NDA to offer certification test at convention
- Hyster-Yale commits to US production
- World Cement Association highlights challenges facing long-term cement demand
- Tata Steel to supply equipment maker JCB
- Light House embarks on construction site plastic scrap recycling effort
- NDA accepting nominations for safety awards
- Jackson Demolition wins safety award
- Cracking under pressure