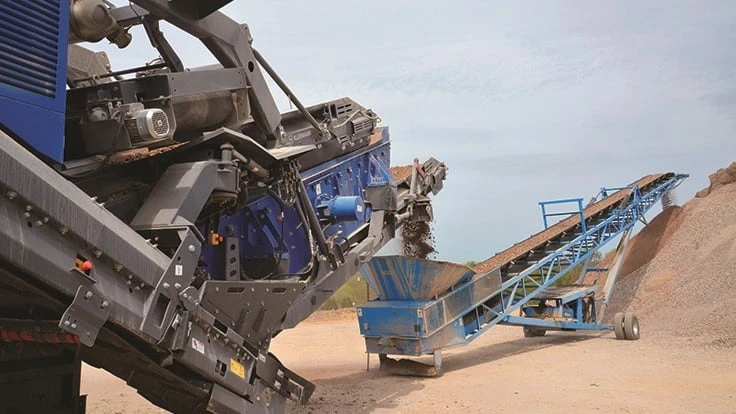
GreenRock Recycling LLC, Clinton, New Jersey, is a construction and demolition recycling company serving residential, municipal and commercial customers throughout the state.
The company, which is a division of the Brian Plushanski Construction Company, started out in 2012 offering standard and dyed mulch, topsoil, mason sand and screenings.
However, sensing an opportunity, the company invested in a Kleeman Mobirex MR 110 ZSi EVO2 impact crusher, manufactured by the Wirtgen Group, in late 2016 to help it process stone and aggregates.
Thanks to its investment, the company has been able to produce a New Jersey Department of Transportation-certified recycled concrete aggregate (RCA) and processed reclaimed asphalt pavement (RAP) product that has a robust market with contractors in the Garden State, the company says.
“Our Kleemann crusher makes a very nice, clean RCA that compacts well, looks like 1 1/2-inch-minus dense graded aggregate, yet is less than half the price,” Mike Plushanski, general manager of GreenRock Recycling, says. “And our RAP is used mostly as a base material, which also is highly compactable and affordable.”
Plushanski explains that the crusher was pivotal in helping the company evolve from its initial emphasis on wood processing.
“Our permitted recycling [operation was] initially wood—as in tree parts only, including stumps, wood chips and logs,” Plushanski says. “But now we receive brick, blocks and concrete, which we commingle to make recycled concrete aggregate. And we receive clean asphalt to make RAP. We balance the cost of processing by charging tipping fees in addition to the product sales.”
In addition to recycling, GreenRock has a small shale quarry on its property in Clinton, which it rips to produce certified clean fill.
“We’re just trying to bring our site down to road grade, so we have one nice level property. The shale can be used very much the same way as RAP, except that shale has more uses, as New Jersey is very strict on how RAP is used. But as a certified clean fill, shale can be used anywhere,” Plushanski explains.

Finding a replacement
GreenRock’s Kleemann crusher replaced a small 1,000-ton per day jaw crusher, which was inherited from an existing construction business, that the company originally used to crush incoming material.
“[We were growing] like crazy, and that little crusher was going 40 hours a week and not putting a dent in the stockpiles,” Plushanski says. “Concrete was coming in so fast that the piles grew even as we were crushing. It also did not have a screening system, and that was part of the problem; we weren’t able to sell material, as flat ‘pancake’ pieces larger than 2 inches would just drop through the jaw. We were unable to meet size specs, and we could not get DOT certification for 1 1/2-inch material, which a lot of contractors need for big jobs. We needed a higher capacity crusher, and we needed to meet DOT standards, so the Kleemann impact crusher was the way to go.”
According to Plushanski, Kleemann’s touch screen control system was one asset of the machine that sold GreenRock on the MR 110 Z Si EVO2.
“The Kleemann is so much more advanced than the other machine we were using,” he said. “With its remote control, I can adjust everything, including the distance of the curtains off the blow bars, or open up the return conveyor. If something goes wrong, you can shut down faster and diagnose the problem and correct it. With the other machine, you had to walk up to a difficult-to-navigate computer screen. With the Kleemann, you just touch the part of the machine on the screen. It’s user-friendly.”
Another aspect of the Kleeman crusher Plushanski liked was how its diesel-electric drive system helped the company manage costs. “Our old jaw crusher was burning 11 gallons per hour,” Plushanski says. “We demoed [another crusher that] was upwards of 14 gallons an hour. The Kleemann burns 6.5 gallons an hour, with a 500-horsepower motor running. The fuel savings are huge.”
The independent prescreen functionality of the Mobirex hopper also was a plus for GreenRock since the company leaves all the fines in its mix. Allowing the fines to bypass the crusher increases wear part longevity, Plushanski says.
“The prescreen [that is situated] ahead of the impactor is so much more efficient than the simple [hole design] of the other machine we looked at,” he says. “Now, being able to adjust the speed of it and making sure we were dropping all the fines out, we don’t have an ounce of fines more than should be going through the rotor. They are dropping right down to the main conveyor and out to the 1 1/2-inch screening system, and not beating up our blow bars.”
Alternatively, GreenRock processes RAP to 1 1/4-inch-minus size, and it’s often used as parking lot or driveway base material. For RCA and RAP, fines are retained to create a product similar to a dense graded aggregate, Plushanski says.
“We want a compactable base material, and for now, we choose not to remove fines out the side conveyor off the prescreen,” he explains.

All about savings
Plushanski says that starting up the crusher in the morning has been made easier thanks to its automated capabilities, especially its automatic closed-side gap setting adjustment.
“You can do the zero-point adjustment all electronically,” Plushanski says. “Whatever size I set the curtain from the blow bars, I know it’s accurate. We no longer crush 40 hours a week as we did with our old crusher. Instead, we only need to crush one or two days a week, so every couple of days, when [we start for the day], I will check the bars and set a new zero point.”
The fact that so much of the Kleemann machine is computer-controlled is a benefit to GreenRock, Plushanski notes.
“The computer operation is a major purchase point,” he says. “The other crusher we demoed had all mechanical adjustments. With the Kleemann, one morning when I was firing it up, I realized I was still set up for RAP. I changed the curtain distance as we idled up for concrete. I changed the prescreen vibrating and hopper speed. I was able to do all three adjustments from the touch screen on the machine, whereas with the other crusher, this meant having to shut down and climb up the machine with a wrench. I would have been up there a half hour trying to dial it down.”
“With the Mobirex, it takes me 30 seconds to adjust three parts of the machine versus not being able to adjust the three parts all at once with the other machine,” he added. “You couldn’t do the prescreen adjustment [with the other machine], and to just do the hopper and blow bar adjustment would have taken me a half hour with the machine off. With the Kleemann, we are up and running without having to stop.”
Kleemann’s diesel-electric drive system also helps the company save time at start-up, especially on cold days.
“It’s nice not having to wait for the hydraulics to warm up,” Plushanski says. “It’s freezing cold up here half the year. In the mornings, we don’t have to wait 25 minutes for the hydraulics to warm up. With the old crusher, we’d start it up, run a conveyor and go back to the office to finish our coffee while it warmed up. When we demoed the Kleeman crusher … it was 9 degrees outside, and it was up and running in 15 minutes.”
Another time-saver for the company is made possible by the machine’s ability to be set up and dismantled seamlessly. “It’s easy to set up and take apart,” Plushanski says. “The conveyor-mount secondary screen system unplugs with quick disconnects. In 15 to 20 minutes, I can drop it, change all the screens and put it back up, and recycle a different product.”

Plushanski says the mobility of the machine also helps the company save time. Since GreenRock moves the impactor to different stockpiles as it produces different products, the ability to change screens quickly and move from pile to pile is a major asset for the company.
Besides time savings during setup, the machine’s design also allows GreenRock to spend less time on upkeep and maintenance.
Aluminum shields around the crusher’s magnet keep the scrap steel and iron discharge, such as from nails or wire, from jamming up the equipment.
“Nothing builds up because it can’t stick to the aluminum, but our old crusher would have had thousands of nails stuck to the frame where it had become magnetized. It was difficult to clean every day,” Plushanski says.
Scrapers on the belts are another advantage from a maintenance and cleanup perspective, Plushanski says.
“It’s the little things that make a difference, like scrapers at the tops of each of the conveyors,” he notes. “No adjustment is needed for them, and they get all of the material off of the belts. As a result, I don’t have a 2-foot-high mound of dust under the machine that I have to clean up each day.
Further, a steel pan feeder located under the crusher intercepts crushed material in advance of the conveyor, absorbing the shock and protecting the conveyor. This saves the company from having to replace belts.
“We use to pierce belts like there was no tomorrow on our old jaw,” he says. “We’d spend $10,000 a year on belts that we otherwise would have no problem with. But these belts never get that abrasive impact. And side rubber skirts keep the material trimmed and centered, and that keeps dust out of the machine.”
In addition to Kleemann staff, product support is provided by GreenRock’s distributor, Komatsu Northeast, which makes ensuring uptime easier for the company.
“I usually call … our Kleemann technical representative when I have a question, and he’s always there for me,” Plushanski says. “But our family has dealt with our distributor for 30 years, and they are awesome. If we need a visit on-site, they are here in two hours.”
Whether it is the ability to market new products, increase efficiency on the job or save money due to more intuitive design, the Kleeman product has been a rock-solid investment for GreenRock Recycling as it continues to grow its operations.
This article appeared in the May/June issue of Construction & Demolition Recycling magazine. Matthew Graves is the director of marketing communications for Wirtgen America Inc. He can be reached at matt.graves@wirtgen-group.com.
Latest from Construction & Demolition Recycling
- Cielo investor requests annual meeting
- CDE sets up washing plant on Long Island, NY
- NWRA: NIOSH cuts a step in the wrong direction
- Ferrous price hikes could be poised to pause
- Northstar secures 15-year lease extension for asphalt shingle recycling facility
- Greenwave asks for SEC filing extension
- Construction Plastics Initiative lines up projects
- ShearCore adds dealership group in Canada