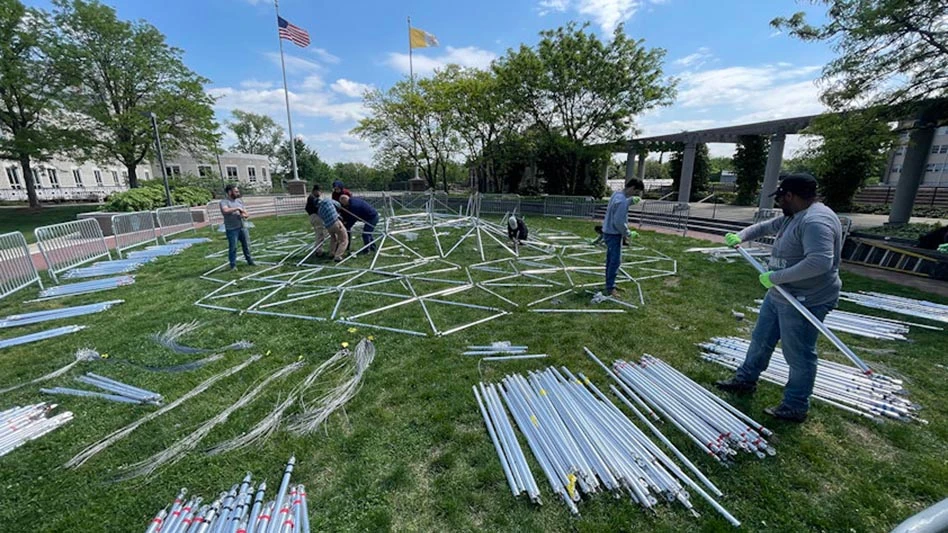
Photo courtesy of Norsk Hydro
Aluminum producer Norsk Hydro, which is based in Norway but has growing operations in the United States, is providing recycled-content extruded aluminum to a team from Catholic University in Washington that is reconstructing a R. Buckminster Fuller geodesic dome inside the Smithsonian’s National Museum of American History.
The firm supplied the project with structural members made from its Circal aluminum, a certified product containing at least 75 percent-recycled postconsumer scrap.
The dome, known as Weatherbreak 8C270, might have been the world’s first such structure when it was built on the outskirts of Montreal in 1950.
The student-led reconstruction of Weatherbreak at the Smithsonian’s National Museum of American History began in early July and will remain on exhibit through the end of the month. Museumgoers will be able to watch the construction project and, after it is built, to walk through the dome as part of an exhibit.
“Thanks to Hydro, we can participate in the restoration of a truly historic piece of architectural history,” says Tonya Ohnstad, assistant professor at Catholic University’s School of Architecture and Planning. “This project is a great learning experience for our students and the use of varied materials is an integrated part of their architecture education. We are looking forward to learning more about the benefits of aluminum as a sustainable building material through the partnership with Norsk Hydro.”
Hydro formed the recycled material into the extruded profiles at its extrusion facility in Elkhart, Indiana. “By increasing the use of postconsumer scrap and driving toward 100 percent-recycled content, aluminum can play a vital role in decarbonizing the building industry,” says Charlie Straface, president of Hydro Extrusion North America.
“By taking end-of-life aluminum scrap and transforming it back into building components, we feel this project highlights the potential of aluminum to address climate change in unique ways.”
In addition to providing replacement pieces for the original structure, Hydro says it is providing enough material for Catholic University to construct a replica dome for a traveling exhibit in the future.
“Hydro is pleased to partner with Catholic University to assist the Smithsonian in helping revive this historic structure," says Trond Gjellesvik, president of Hydro Aluminum Metals USA. "The team at our Henderson, Kentucky, recycling plant was able to produce extrusion ingots for this historic project almost entirely from postconsumer scrap, the reuse of which is critical to improve sustainability.”
Using the theories of renowned American architect, inventor and futurist Buckminster Fuller, Jeffrey Lindsay, a former student of Fuller’s and director of the Fuller Research Foundation’s Canadian Division, designed the innovative 8-frequency hemispherical icosahedron and oversaw all aspects of its manufacturing and installation.
The original dome, now part of the museum’s collections, originally consisted of nearly 1,000 pieces, many of which were damaged or lost over time. Hydro is helping replace these missing pieces by providing extruded aluminum made with Circal, which it says offers the lowest carbon footprint of any aluminum product manufactured in the world today.
Latest from Construction & Demolition Recycling
- Trump copper tariff includes potential scrap export restrictions
- CDE publishes sustainability report
- AED opposes 'right to repair' language in federal bill
- UP reaches agreement to acquire Norfolk Southern
- Eco Material Technologies opens cement alternatives plant
- Nucor still chasing 2024 profit levels
- Deadline extended: ‘C&DR’ seeks industry participation for 2025 Largest C&D Recyclers List
- Algoma Steel seeks government funding