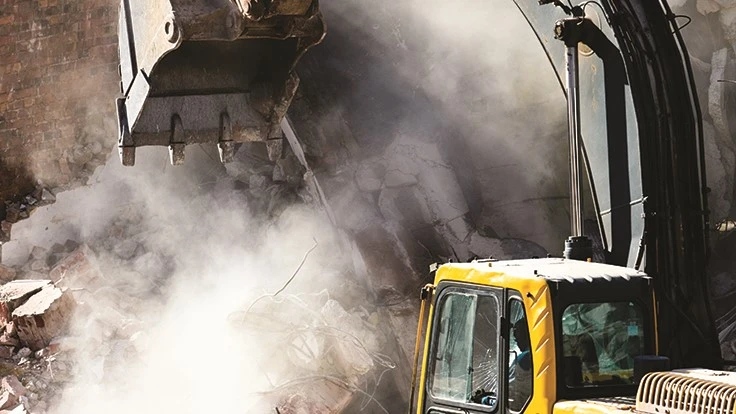
The demolition industry is constantly evolving, and the trends and regulations associated with the remediation side of the industry often appear to be a moving target. Many of the current discussions going on in the industry are centered on two main issues: silica enforcement efforts by the Occupational Safety and Health Administration (OSHA) and how to handle polychlorinated biphenyls (PCBs) in the form of building materials and PCB bulk product waste.
The key to handling each of these issues effectively comes down to what the contractor has done in the planning stages of the project. The more time and effort that is put into the planning stages, the more it will help to keep the contractor out of regulatory danger and simplify execution of the project.
Standards for silica control
The OSHA final rule on Occupational Exposure to Respirable Crystalline Silica was published on March 25, 2016. Silica is a natural substance found in most rocks, sand and clay, and thus in products such as bricks and concrete. The demolition process almost invariably produces dust with silica included.
There has been quite a bit of confusion about this rule, in part because OSHA initially deferred enforcement on the standard, in fact several times, but finally started enforcement on Sept. 23, 2017.
During the first 30 days of enforcement, OSHA provided compliance assistance in lieu of citations for companies showing good faith efforts toward compliance. Effective Oct. 23, 2017, OSHA started to fully enforce the entire standard.
The new rule brought some clarity to the permissible exposure limit (PEL) of crystalline silica by setting it at 50 micrograms per cubic meter (50 µg/m3) during an eight-hour time weighted average (TWA), and an action level (AL) of 25µg/m3.
OSHA also added a specific set of work practices and mitigation techniques in what is referred to as Table 1 in the standard. Contractors who follow the guidance for the practices contained in Table 1 will not need to comply with the rest of the standard as the listed mitigation methods are considered by OSHA to be effective for the hazard. More on this can be found online at www.osha.gov/dsg/topics/silicacrystalline/construction.html#tableOneTasks.
However, contractors must be aware that if the work being conducted or the tools are different than what is outlined in Table 1, they become responsible for complying with the full standard, including producing a written program, medical surveillance, exposure monitoring and setting up regulated areas.
Planning and preparing means and methods to be used and comparing those methods to those listed in Table 1 of the standard can save the contractor compliance headaches.
If contractors are unable to make their practices mirror Table 1, then OSHA provides several helpful documents to guide their compliance efforts. These can be found at www.osha.gov/dsg/topics/silica crystalline.
These programs are similar to lead and asbestos programs used every day by contractors. If this still seems confusing, contractors should seek out a safety professional or consultant.

Passing the series of PCB tests
The PCB issue has been prominent since the late 1970s when the United States Environmental Protection Agency (EPA) banned the use of PCBs in domestically manufactured products.
The emphasis in the early days of the Toxic Substances Control Act (TSCA) was focused on electrical equipment such as the oil in transformers, capacitors and ballasts, but nonliquid PCBs also can be found in building materials.
The EPA has stated that numerous building materials produced before the PCB ban in 1979 must be handled under TSCA guidelines. These products include: cable insulation; thermal insulation material, including fiberglass, felt, foam and cork; adhesives; tapes; paint; floor finishes and caulking.
The management best practices (MBP) for the demolition of buildings that contain or have the potential to contain PCB materials requires that a hazardous building materials assessment be conducted.
This is not limited to the two materials being discussed in this article, and includes asbestos, lead paint, mercury-containing devices and bulbs and ballasts. The testing of caulks, paints and mastics is a must to identify possible PCB contamination.
Building materials found to contain PCBs in an amount greater than or equal to 50 parts per million (50 ppm) in a nonliquid state must be removed and disposed of as bulk product waste. Any materials that have adhered to the PCB-contaminated building material, where PCBs may have leached into the material, must be either cleaned or disposed of as PCB bulk product waste.
Contractors must be careful, however. If the contractor chooses to clean the material and waste is generated during the cleaning process, it will be considered PCB remediation waste and the contractor must follow the specific TSCA disposal requirements. There are currently three options under TSCA for disposal of remediation waste:
- The first is self-implementing cleanup and disposal (40CFR Section 761.61[a]). This method requires contractors to notify their EPA regional PCB coordinator.
- The second is performance-based disposal (40CFR Section 761.61[b]). This method requires disposal in a TSCA landfill or incinerator through a TSCA-approved disposal method. This method generally does not require approval of the EPA.
- The third method is risk-based cleanup and disposal and provides for alternative cleanup or disposal methods not covered in the first two choices (40CFR Section 761.61 [c]). This method requires that the contractor gain approval from the EPA prior to starting work.
The TSCA PCB disposal rules are prescriptive and can cause regulatory headaches for contractors who do not follow the letter of the law. The EPA provides guides to disposal and PCBs in building materials at www.epa.gov/pcbs.
Whenever the demolition industry moves into new territory, it feels uncomfortable, restrictive and even at times nonsensical. But regulations rarely, if ever, regress, and it is important to face these issues head on and work to improve techniques to implement the new regulations and practices.
The best way to accomplish this is through a robust planning process including a hazardous building assessment to help identify issues before regulators do. If a contractor develops best practices and revise current methods, then he or she can breathe easy and execute the job with reduced risk.
The author is a technical director with Environmental Resource Management (ERM) Group Inc., Malvern, Pennsylvania. Contact him at Mike.Casbon@erm.com.
Latest from Construction & Demolition Recycling
- Mazza Recycling adds to transfer station operations
- Michigan awards $5.6M in recycling, waste reduction grants
- Pittsburgh area mall headed for demolition
- RMDAS figures show February surge in recycled steel’s value
- US economic indicators show signs of wavering
- Northstar signs asphalt shingle supply agreement with York1
- Metso’s Lokotrack line turns 40
- Takeuchi adds dealer in Mississippi