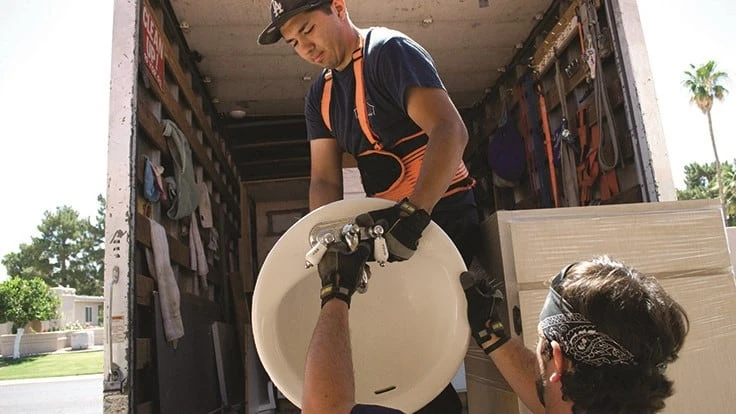
Photo by Matt Fulton
Lived-in buildings can contain a treasure trove of items. From cabinetry and countertops to flooring and furniture, a multitude of items within a structure's walls are often salvageable either for reuse or recycling.
But when these buildings are remodeled, the wealth of salvageable materials and furnishings can be lost to landfill if entire rooms are haphazardly demolished.
Arizona philanthropist Jerry Bisgrove, the founder of the Scottsdale-based Stardust Companies group of organizations, recognized the value of items in his home. Before undertaking a complete home remodeling and demolition in the mid-1990s, he told a friend to take whatever she wanted from the house. To his surprise, she had cleared out nearly everything usable, from cabinets and plumbing fixtures to lighting and electrical supplies.
The experience inspired Bisgrove to found Stardust Building Supplies in 1997. Stardust is a nonprofit organization based in Mesa, Arizona, that provides deconstruction services. After a building is deconstructed, Stardust sells the salvaged material in its two reuse centers. Every year, the organization not only diverts 5 million tons of material from landfill, says Stardust CEO Karen Jayne, but also works to advocate for the wider acceptance of deconstruction practices.
“Not only does it save [customers] money, but it really does help people in the community who might not have access to full-price home remodeling materials. And then it also helps reduce the waste that goes into our landfill, especially with things that are in good condition and great to reuse,” Jayne says.
Sorting through material
Stardust owns two reuse centers in Arizona where it stores its material—a 44,000-square-foot warehouse in East Valley and a 27,000-square-foot warehouse in Glendale.
There, the organization houses its material that comes in from both donations and its deconstruction services. On any given day, material at the facilities can range from traditional construction and demolition (C&D) material, like brick, concrete block and hardwood flooring, to interior and exterior fixtures, like appliances, plumbing, fencing, furniture and electrical supplies.
The organization employs 32 people, 10 of whom work daily to either to deconstruct buildings, pick up donations or sort through material in the warehouses. Those working in the warehouse require meticulous attention to detail to determine which items they can accept and the value of each. Typically, two staff members work in each receiving area to help unload donations. They then assess each item for its quality, style, size, age and functionality. Employees scrap items that don’t work and assign prices to those that do.
“They use a price book we have established that identifies a grading process that goes through what the price would be for that item,” Jayne says. “We use a point of sale system, so they enter the donations into the point of sale system and make what we call a receiving voucher. And then that spits out the tickets that actually go on each item. So the receiving staff tags the items, and then the materials are moved out onto the sales floor.”
Jayne says on top of working with low-income housing owners and other nonprofit organizations to find homes for the material, more than 3,000 customers shop through the warehouses each month.
“There are individuals who are renovating their homes, so they use us for materials that are more economically priced for them. There are also a large number of landlords who use us as a resource to repair and maintain their properties. Then there are some general contractors and handymen that actually do maintenance repairs for homeowners, and there is a group of reuse folks that use our materials for various creative projects,” Jayne says.
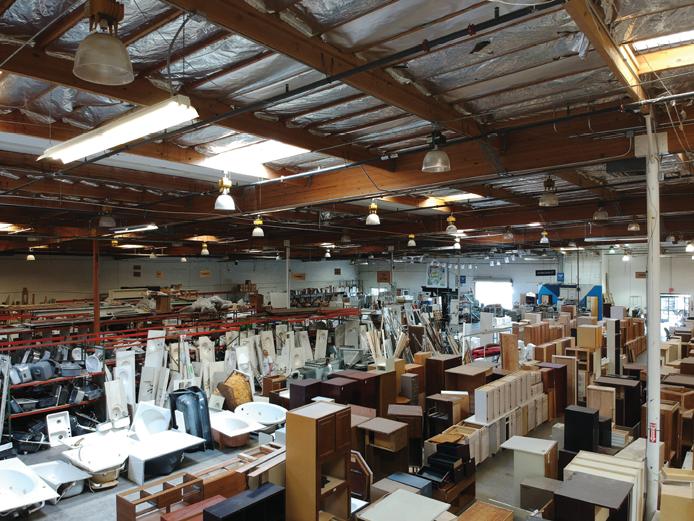
Deconstruction at your service
On top of accepting donations, Stardust also offers deconstruction services for homeowners and commercial properties at a low cost. Jayne says a typical deconstruction costs about $200. In 2018, the Stardust crew performed nearly 750 deconstruction jobs, which normally take between one to four hours each.
“Monday through Friday, we have deconstruction teams that are out in the community removing usable material, mostly from homes that are being remodeled, and they do up to four jobs a day,” Jayne says.
The organization typically receives calls for services from individual homeowners. More recently, however, Stardust has begun collaborating with contractors to remove valuable material before they sweep through the area to provide heavier demo services. In an initiative called “Starve the Landfill,” Stardust has begun publicly recognizing the contractors it works with in these endeavors in an attempt to encourage more to participate.
“They get recognition on our website, and we do social media posts about them. We also link from our website to their website or social media [pages], and we also share that in press releases, especially when they're new to the program,” Jayne says. “When they need us to come pick up a donation or if we're deconstructing for them, they'll also get special treatment to get on [our] schedule.”
Stardust owns a fleet of five box trucks that the deconstruction crew uses to transport material to and from the site. The organization’s deconstruction services are fairly limited, as it can’t provide heavier services like removing flooring or drywall. Its crew primarily uses handheld tools like crowbars, hammers and screwdrivers. Additionally, crews can’t deconstruct any homes built before 1978 due to Environmental Protection Agency (EPA) lead paint rules.
The material they do recover, however, can be high in value.
“There are pockets of areas here that have very high-end, multimillion dollar homes. We've definitely deconstructed large homes with multiple kitchens and multiple buildings on-site. We've removed solid gold plumbing fixtures, and we've removed an elevator from one job—also things like solid marble, fireplace mantles, large chandeliers and all those kinds of things,” Jayne says.

An important step
Though demolition is often still needed after Stardust's deconstruction services, it’s an important step that can both make demolition easier and provide a variety of benefits to the community and environment.
The city of Portland, Oregon, has set up an online deconstruction calculator tool to calculate the benefits associated with deconstruction versus demolition. According to a recent calculation of a 2,800-square-foot home, deconstructing saves more than 1,800 kilowatt hours of electricity, releases 24 fewer tons of carbon dioxide into the atmosphere and generates six jobs for every one job in demolition. Deconstruction also requires less dust suppression than traditional demolition, saving hundreds of gallons of water per job, according to Build Reuse (previously the Building Materials Reuse Association), which advocates for turning C&D waste into local resources.
Thanks to its benefits, communities have started to recognize the importance of deconstruction. Portland and Milwaukee, for instance, now require some structures to be fully deconstructed rather than mechanically demolished to salvage material and reduce waste. The city of Palo Alto, California, has similar regulations that are set to take effect in 2020.
Additionally, Stardust is working with the city of Phoenix as well as the state of Arizona in an attempt to promote deconstruction practices locally. Jayne says the organization will soon be launching a campaign with a video that educates the public about deconstruction and its benefits. Stardust is also working with local planning committees to explore ways to incentivize the practice throughout the state.
“People don't know about deconstruction, so it's always a challenge to educate folks on the benefits and how important it is—not only how it saves them money in their remodeling projects, but also how it keeps usable material out of the landfill that someone else can use and benefit from,” Jayne says. “I think people don't realize that it's expensive for a large segment of our community to maintain their homes, and reuse really provides that avenue for a lot of people.”
This article originally appeared in the Nov./Dec. issue of Construction & Demolition Recycling magazine. The author is the assistant editor for Construction & Demolition Recycling magazine and can be reached at tcottom@gie.net.
Latest from Construction & Demolition Recycling
- US Senate backs reduced cuts to EPA
- US EPA offers brownfields-related funding
- Sky Quarry seeks crowdfunding support
- Caterpillar releases the new Cat 980 GC Wheel Loader
- NAPA leaders participate in USDOT roundtable
- Yanmar CE launches full line of compact equipment
- Metso reports increased orders after flat H1
- Block Island Recycling Management Inc. aims to promote environmental stewardship