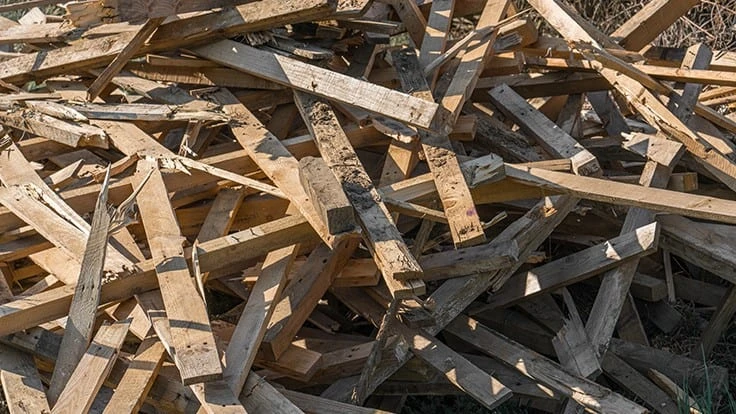
Adobe Stock Image Credit: Ralph
Converting fines and less desirable fractions of the wood stream into marketable products is an ongoing challenge for C&D recyclers. However, new research from the University of Florida shows the potential benefits of using biochar and biochar-blended fines in landfill applications to neutralize both odorous hydrogen sulfide (H2S) and hazardous per- and polyfluoroalkyl substances (PFAS).
Timothy Townsend, professor at the University of Florida’s Department of Environmental Engineering Sciences, gave a presentation titled, “Opportunities with C&D Fines and Wood-Derived Biochar” on March 22 at the Construction & Demolition Recycling Association’s (CDRA’s) C&D World convention.
Townsend, whose research focuses on identifying beneficial uses for waste materials, has partnered with the CDRA to specifically identify opportunities for C&D wood and fines.
C&D wood is typically derived from dimensional lumber, pallets, land clearing material, and engineered and treated wood. Townsend says that dimensional lumber, or what recyclers may refer to as A-line wood, often can be sold to those creating landscaping products or other markets without much difficulty. Engineered and treated wood, however, can present more of a challenge due to the potential presence of glues, paints and chemicals.
Fines, which are the shake-like byproduct of screening and sorting processes, are commonly composed of a variety of materials. Common markets for fines include use as landfill cover, fill material, and as soil and agricultural amendments. However, similar to C&D wood, fines can be difficult to market since the composition and quality varies based on a recycler’s waste stream and screening and sorting processes.
“If you’re looking to market fines as landfill cover, and you have gypsum in the fines composition, you can have hydrogen sulfide that's produced that limits the number of areas around the country where this material can be used,” Townsend says.
“In terms of using fines as fill material, I’ve spent a lot of time working with CDRA members trying to figure out if there was a way to make those fines a better product,” he continues. “I would encourage recyclers to explore opportunities to process and create better products. I think, on the horizon, you’ll have opportunities to create fines that would be a stronger material that might be suitable for some type of base course or some more structural material, or even material that is better suited for agriculture. But the big challenge if you want to go use fines out in the environment, like all waste products, there can be small amounts of chemicals, such as arsenic, lead and sulfate, that can be a concern.”
Because of these environmental issues, Townsend says recyclers can run into problems when trying to market fines “as is” but, “if recyclers recognize what the concerns are potentially, they can create a better product” through investments in new technologies. He says that this requires recyclers to shift their mindsets from “managing byproducts to developing products.”
Townsend says that air separation, screening and washing processes can be especially useful in separating aggregate, wood, paper, plastic and drywall concentrations in the fines. By better sorting this material, recyclers can market fines in a way that may help overcome regulatory challenges.
Once recyclers fully understand what the composition of their fines is, they can make strategic decisions and investments to finetune this mix to appeal to different end markets.
By being more selective on the waste that is processed, the size fractions that are generated, and by embracing washing and blending solutions, operators can overcome some limitations that often exist when looking for markets for C&D fines, Townsend notes.
Benefits of biochar
Townsend says that recyclers have begun to explore converting less marketable wood from their B and C lines into biochar. Biochar, which is a charcoal produced from the pyrolysis of wood in a low oxygen environment, can be used on its own or mixed with fines in landfill cover applications to mitigate H2S generation that naturally occurs at landfills and in some gypsum-containing fines.
Townsend says his research has shown that the more biochar you add to fines, the more H2S you sequester. However, he concedes that having a mix of 90 percent biochar to 10 percent fines, for example, defeats the purpose of trying to find an economical use for fines.
He says that a mix with 15 percent biochar reduces H2S by 1 to 2 orders of magnitude in lab testing. At 30 percent biochar, H2S is reduced by 2 to 3 orders of magnitude or more. The sweet spot for both economical and effective use probably lies in biochar blends of 10 to 20 percent, he says.
Townsend says that because moisture content can exacerbate H2S generation in drywall-containing fines, fines used as cover material in wet climates can have the propensity to generate more hydrogen sulfide than in drier locales.
In initial field tests where fines were used as alternative daily cover at landfills, Townsend says that measurable H2S concentrations were periodically detected, although at low levels. However, when the fines were blended with biochar, H2S levels were uniformly below detection in the field tests. Townsend conceded that these studies, which were delayed due to COVID-related shutdowns at the university, were still ongoing.
A word on PFAS
In addition to mitigating H2S generation at landfills, Townsend says biochar shows promise for capturing PFAS chemicals. These chemicals have been subject to scrutiny from the EPA and other regulators in recent years due to their health-related risks that include liver damage, thyroid disease, and cancer, among other issues.
“PFAS is not a lot of fun to talk about because there are not a lot of good implications because it's a new chemical. [It’s like] if we were now just discovering lead-based paint or asbestos or something like that,” Townsend says. “For the C&D recycling industry, PFAS is not going to be as big of a deal as those issues, but the idea is that it is better to become educated now and then be able to think a little bit on how the industry can position itself with some of its markets to perhaps be able to address the issue. There are some in the industry who are already working on doing that.”
Townsend says that these PFAS “forever” chemicals, which are used to make an assortment of commercial and consumer products such as nonstick cookwear, water-resistant clothing, stain-resistant fabric and carpet, and packaging and firefighting foam, are found in leachate at every landfill in the world.
“If you look at C&D landfills, you find PFAS in the leachate—it’s not that different than regular MSW landfills. … In terms of bulkier C&D-type items where you might see PFAS are mattresses, furniture, clothing, tents, umbrellas, carpet and carpet padding. The good news is that with concrete, drywall, wood, most of the products C&D recyclers deal with, overall PFAS concentrations should be pretty low,” he says.
Townsend says that even though PFAS isn’t found in quite the same concentrations as in MSW streams, the EPA’s emphasis on identifying and mitigating the substance requires C&D recyclers to be at least aware of possible materials that may contain these chemicals.
Townsend singles out carpet, fines and asphalt shingles as primary sources of PFAS that C&D generators should be mindful of.
In discussing how PFAS could influence shingle recycling markets, Townsend says that recycled shingles in hot mix asphalt concentrations likely wouldn’t lead to an issue, whereas ground shingles used in road pavement could raise the issue of environmental contamination due to its potential to leach into the groundwater.
Despite the environmental concerns with PFAS, Townsend says there are some potential opportunities for recyclers.
“With biochar, we know it can help [sequester] H2S, but can it take up PFAS? Absolutely it can, because a lot of the PFAS remediation sites across the country use activated carbon [that is similar to biochar] to remove that,” he says.
During his presentation, Townsend shared lab results that showed how biochar mixed with fines helped greatly neutralize PFAS concentrations found in test samples. According to University of Florida tests, the inclusion of biochar in a sample equated to a greater than 80 percent reduction in PFAS found in leachate.
“Just like with using biochar to neutralize H2S, C&D recyclers would have to be investing in technologies and equipment to make the biochar from a fraction of their wood stream [for PFAS mitigation], but then there could be the ability to market that as a product,” Townsend says.
“Landfills need soil products. [MSW landfills] need this because it is part of Subtitle D. And in a lot of cases, they need to pay to get soil in because they don’t always have big borrow pits,” he says. “So, imagine that the soils that recyclers could provide to them would be such that they could help control the H2S problem, but also help absorb and trap material like PFAS. … If you integrated some of these fines with biochar or just used the biochar itself from C&D-derived sources … you have the ability to bind these chemicals up. This might have more applicability in some markets than others, but for C&D recyclers, it is something to think about. C&D-derived biochar continues to show a lot of promise.”
WANT MORE?
Enter your email to receive our newsletters.
Latest from Construction & Demolition Recycling
- Sky Quarry enters LOI with Southwind RAS to advance shingle recycling
- Owens Corning successfully manufactures shingles from extracted asphalt
- McClung-Logan Equipment Co. joins Tana’s authorized dealer network
- ‘C&DR’ seeks industry participation for 2025 Largest C&D Recyclers List
- Wood recycling market to reach $30B by 2032
- Deeper Insights: Ron Tazelaar and Dan Rudman
- Nexwaste acquires 3 Texas businesses
- Metso says HRC crushers offer circular benefits