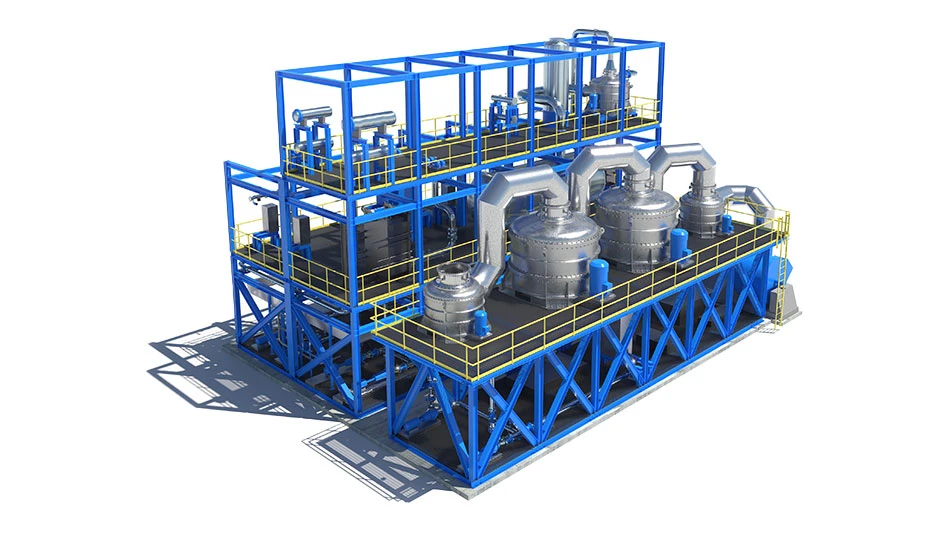
Photo courtesy of Carbon Clean
Carbon Clean, a provider of carbon capture solutions for hard-to-abate industries, including cement, steel, refineries and energy from waste, has launched its CycloneCC C1 series.
The fully modular and columnless CycloneCC C1 series is available in concentrations ranging from 3 percent to 20 percent, capturing up to 100,000 tons of CO2 per year. The CycloneCC C1 achieves a height reduction of 70 percent compared with conventional solutions, according to Carbon Clean, and features rotating packed bed (RPB) technology that replaces every column used in a conventional plant, reducing the steel required by 35 percent and lowering the unit’s carbon footprint.
Its footprint also is up to 50 percent smaller than conventional carbon capture plants, with its largest equipment sizes reduced by a factor of 10, Carbon Clean says. Each unit is prefabricated, skid-mounted and delivered on road truckable modules, cutting the costs associated with transport, logistics, site preparation and installation. CycloneCC C1 uses first-of-a-kind technology to reduce the total installed cost of carbon capture by up to 50 percent compared with conventional solutions.
With its space-efficient design, CycloneCC C1 can offer a viable, cost-effective route to decarbonization, particularly for small-to-midsize emitters, Carbon Clean says. CycloneCC C1 also can be used by emitters of all sizes looking to deploy carbon capture units across multiple flue gas emission sources.
“The launch of the CycloneCC C1 series is a major milestone in the technology’s commercialization,” says Prateek Bumb, co-founder and chief technology officer of Carbon Clean. “Repeatability is key to mass adoption, as demonstrated with solar panels and EV batteries. Carbon Clean is leading a similar transformation through eliminating the columns used in conventional carbon capture solutions. Delivering fully modular, columnless, replicable units with a substantially smaller footprint is a technological breakthrough.
“CycloneCC’s ‘Lego-block’, ‘plug and play’ design makes it simple and cost-effective to install, making carbon capture financially and logistically viable to be deployed at scale. First-mover customers and early adopters will have the advantage of tangible decarbonization results while benefiting from a staggered approach to capital investment due to CycloneCC C1’s modular design.”
The CycloneCC C1 combines two process intensification technologies: RPBs and Carbon Clean’s proprietary APBS-CDRMax solvent. Using RPBs to replace the columns used in conventional carbon capture solutions reduces the size of the plant and accelerates the mass transfer process, increasing CO2 absorption, according to the company.
Carbon Clean says its APBS-CDRMax solvent enables opex savings by outperforming the industry standard solvent, reducing energy demand by 10 percent to 25 percent, corrosion by a factor of 20, degradation by a factor of 10 and has a life span that is five times longer than conventional solvents.
Carbon Clean has more than a decade of experience in designing, building and operating industrial carbon capture systems and 49 technology references around the world. It has more than 105 active patent assets across 18 patent families covering 30 countries.
Headquartered in the U.K. and with offices in the U.S., Canada and India, Carbon Clean has received funding and grant support from the British and U.S. governments and has established partnerships with industry leaders including Chevron and Cemex.
Initial CycloneCC C1 series customers will have the opportunity to influence the development of the fully commercialized product while experiencing the benefits of tangible decarbonization results, Carbon Clean says, and will be priority customers for the fully commercialized product when it is rolled out at scale.
Latest from Construction & Demolition Recycling
- Scrap(yard) Master Magnet
- Suspended Electromagnet Overhead Separators
- Javelin Product – Eddy Current Separator
- Lee Zeldin sworn in as new EPA administrator
- McCloskey dealer expands its footprint in the Midwest
- C&D World session preview: Optimizing Plant Operations with best practices for efficiency and success
- New recycling facility will turn food, beverage cartons into building materials
- C&D waste market expected to reach $49B by 2031