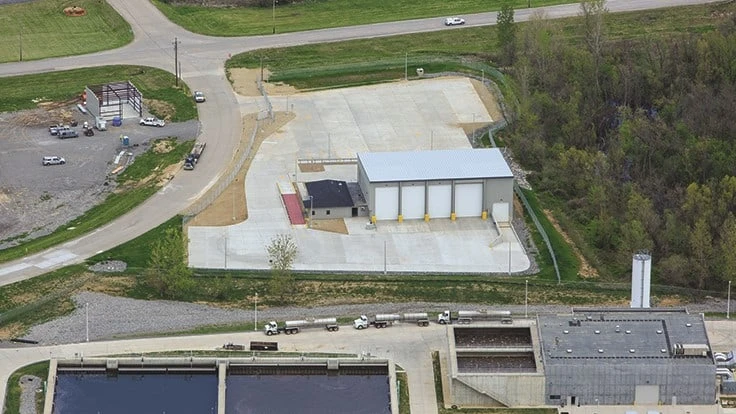
Photo Credit Cambridge Companies
I hear it all the time: “I’ll get an architect to design my transfer station, and then it will be easy to just find anyone to build it.” I’m here to tell you it’s not that simple. Some people think these facilities are just concrete and steel—they can’t be that difficult to build, right? Well, there are myriad factors that come into play during construction where the intent of the design just can’t be made clear enough. During these times, experienced and knowledgeable professionals are needed to take the lead.
The tipping floor
While many people think the tipping floor is just a concrete floor with rebar, so much more goes into the design and the makeup of the concrete itself. I would venture to say 99 percent of the architect and engineering firms out there don’t know how to design a tipping floor to withstand the abuse it takes on a daily basis. On top of that, 99 percent of contractors don’t know how to properly pour the concrete or place the rebar in these facilities. By using a general contracting firm to design or build transfer stations, it is highly likely that a basic tipping floor installed by inexperienced contractors will wear down too fast (sometimes within three to seven years) and cost a lot of money in inefficiencies and repairs over the life of the facility. By contrast, a proper concrete mix design can keep tipping floors intact for over 15 years without the need for repairs.
In terms of pouring the floor, the contractor must have experience with the right mix in order to do it correctly. Contractors need to understand how many control joints should be placed and where, why the floor should slope a certain way, how the rebar needs to be placed, why testing is important and how many tests are necessary for the mix during placement, how to cure the floor to limit stress cracks, and various other considerations. With all these job-specific requirements, being able to rely on a building team that has specialized in transfer station construction or other similar types of jobs is critical.
The cast-in-place walls
Similar to the exacting nature of pouring floors, transfer station walls require steel embeds placed in specific locations. Whether it be for push, scrape, curb or pit walls, these require placement at precise locations for a very specific purpose. The contractor must have experience with these walls since they are responsible for the guidance and verification of the placement on all embeds and must understand the reasons why they are to be placed in specific locations. Otherwise, general concrete contractors who don’t have experience with them may arbitrarily change steel placements because they don’t understand why a wall was designed in that particular way.

During building, I have heard of inexperienced contractors advocating for using tilt-up, precast walls instead of pouring the embeds in place. This is never the answer, as these will not hold up or take the abuse of the facility. Additionally, contractors must understand the pour sequence and placement of the cold joints in order to maintain the integrity of the wall. This kind of information is not included in the design drawings and is another reason why operators must hire a competent, experienced contractor for designing and building their facility.
The metal building
Metal buildings are another transfer station component that require a more nuanced construction process than what some might expect. The primary objective of the metal building is to construct a safe space away from the daily operations, while constructing it so that there are no pockets where trash can accumulate. This is why having a dialed-in set of parameters is a must during construction. For these reasons, straight columns are preferred. Some other metal building design best practices include ensuring there is a maximum depth on the columns, using straight girt conditions on some walls and bypass on others, having specific girt locations for the closure plate to sit on, installing a piece of tube steel to support the pit deflector that is specifically designed for that purpose, and galvanizing the secondary members for long-term durability.
Contractors should also order overhead door jambs that are heavier duty in nature than their standard counterparts so they can handle the weight and operations of the large coiling doors. Upgrades like these aren’t always known or conveyed properly within the architect’s design, but contractors must know these requirements in advance for them to be built into the facility design operation. The metal building is a key component to the long-term success of a facility, and as such, it is important that these are built correctly the first time.

Choosing a contractor
The operator’s goal when picking a design and build team should be to find one with the experience needed to construct a facility that is operationally efficient, durable and requires as little long-term maintenance as possible. Most owners don’t have experience building these sites, so they haven’t developed the expertise required to tell an architect and contractor how it should be done. Moreover, owners don’t have the time to go over the fine details of the build because they have to focus on their daily operations. Owners put their trust in architects and contractors and should expect that they know what they are doing relative to the project. However, it seems all too often, people in the industry have architects and contractors who don’t even know what a transfer station is when beginning the project. These are not the people who can be trusted with taking on the responsibilities of the task at hand.
Finding the right fit
These facilities are a major investment. Operators need to trust the team they hire and know these professionals understand the operations of the facility and why certain site-specific building specs are important. Undergoing a qualifications phase before selecting a team can be helpful. During this process, it is wise to engage several architects and contractors, bring them in and ask for their statements of qualifications for similar projects, references and resumes of the team members who will be working on the project. Then, select the best fit for your needs. While price is an important part of any decision for businesses, this shouldn’t be the deciding factor when thinking about transfer station construction. This will be one of the most important decisions of your career, and it needs to be managed accordingly.
This article originally appeared in the October issue of Waste Today. Jeff Eriks is a vice president of business development & marketing at Cambridge Companies in Griffith, Indiana, a design-build firm working with the waste industry for more than 20 years. He can be reached via email at JeffEriks@CambridgeCoInc.com.
Latest from Construction & Demolition Recycling
- US Senate backs reduced cuts to EPA
- US EPA offers brownfields-related funding
- Sky Quarry seeks crowdfunding support
- Caterpillar releases the new Cat 980 GC Wheel Loader
- NAPA leaders participate in USDOT roundtable
- Yanmar CE launches full line of compact equipment
- Metso reports increased orders after flat H1
- Block Island Recycling Management Inc. aims to promote environmental stewardship