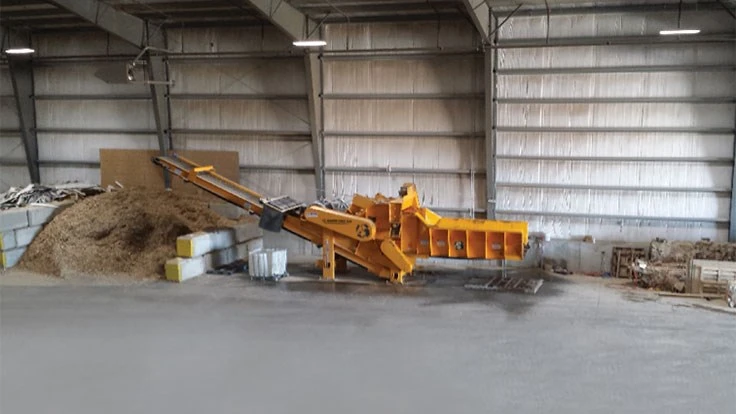

Landfill-Environmental-Diversion-Reclamation (LEDR) Recycling opened an indoor material recovery facility (MRF) in spring 2015. Positioned just across the river from St. Louis in a northwest suburb, the construction and demolition (C&D) recycling center processes concrete, aggregate, drywall, plastic, metal, shingles, vinyl siding, granite tile, wood scrap and more. Its stationary processing system was custom designed and manufactured entirely by Continental Biomass Industries (CBI), Newton, New Hampshire.
Instead of waiting upwards of nearly an hour between loads, trucks now resort to LEDR’s 3-acre concrete plot to drop off debris without any wait. Phase I of the custom-built system features an Action Taper-Slot screener, fines conveyor, fines magnet, incline conveyor, mezzanine, picking conveyor and an in-line electromagnet.
CHOOSING THE RIGHT TOOLS

New construction and demolition in metropolitan St. Louis and St. Charles County created an emerging demand for wood scrap processing in the area, with more and more debris ending up at LEDR’s tipping floor.
“We get loads from downtown St. Louis, and St. Charles County is still the largest area where new homes are going up,” says John Davis of LEDR. “We have a lot of new homes, a lot of industry, a lot of old farmland that’s being transformed into business parks and commerce centers around us, and then there’s also a lot of new building going on in downtown St. Louis.”
St. Louis saw one of its highest construction increases in the last decade in the fiscal year of 2016, with the city’s building division issuing nearly 5,000 building permits for residential and commercial construction.
LEDR’s estimated on its website, www.ledrrecycling.com, that construction of the average new home in America generates 3 to 6 tons of material. Building permits equaled more than $700 million dollars over the period, representing a 12 percent annual increase in office projects including rehabs, new lofts, hospital construction, single-family and multifamily residential construction and new commercial construction.
Wood scrap became overwhelming for LEDR’s 35,000 square-foot facility. Plywood, wall studs, two-by-fours and pallet-type material proved difficult to keep on-site and costly to haul out.
“The wood is so bulky that you couldn’t store the amount of wood we get for more than a day if you didn’t have a way to grind it and condense it into mulch,” says Davis. “We were hauling it out. Really up until that point we struggled because we had the wood and no place to go with it.
He adds, “We don’t have any biomass around here, so we were stuck hauling it up to a tree service yard for them to grind—but that’s not feasible, you’re lucky to get 6 to 7 tons of raw pallet-type wood onto the tractor trailer.”
Recognizing that about 40 percent of his inbound material was wood, Davis scheduled the installation of a specialized CBI Magnum Force 5400SE-SA stationary electric grinder to downsize material and save on energy costs.
The CBI Magnum Force 5400SE-SA horizontal grinder is for customers looking for a smaller production rate than CBI’s standard 5400SE. The 5400SE-SA grinds pallets, C&D debris, storm debris, slash, regrind or yard waste.
REAPING THE BENEFITS
From the beginning, Davis was steered away from diesel machines because his operation is indoors, but he’s also been impressed by the energy saving benefits.
“It’s an electric-powered machine, which is the best for our application inside. A diesel motor creating exhaust would be a burden inside our facility,” says Davis.
As for the operation of the machine, Davis says, “We turn on the 5400 in the morning and it runs all day long.”
Even though it runs for long periods of time, Davis says the machine doesn’t use much power. “It’s just sitting there free-wheeling, very little power, and you don’t have to worry about diesel fumes or the air being so bad that a motor with a radiator would be a bad situation.”
With wood making up around 40 percent of the company’s inbound material, LEDR needed a machine to grind high amounts of wood, and the 5400SE-SA has kept up. It has been able to work in the tough conditions of a C&D recycling facility, according to Davis.
“We’ve got the big C&D block type teeth on it, and we’ve been running the machine for about a year-and-a-half now; we haven’t even switched a tooth directionally yet,” says Davis. “We haven’t changed a tooth, and we haven’t lost a tooth. Plus, now we’re getting paid for it where in the past we were paying to get rid of it.”
Grinding the processed material allows LEDR to maximize the payload for transportation. Pallets and two-by-fours can now be consolidated and loaded into a trailer at full capacity.
“We haul out usually 200 to 300 cubic yards of mulch a day,” says Davis.
After having the new electric grinder for a year and a half, LEDR processes 60 to 80 tons of wood scrap daily, limited only by its ability to load the machine.
Rather than paying to haul out the wood, LEDR grinds the C&D debris down to raw product and sells it to one of the biggest mulch yards in the area. The mulch yard regrinds and recolors the material to fine landscaping mulch.
“It’s a great industry to work in because it’s the right thing to do for the environment,” says Davis. “Everybody works to recycle more efficiently while making sure their plants are also operating as efficiently as possible.”
LEDR’s investment in green recycling has proven to be a highly efficient solution from a business standpoint, while driving massive reductions waste going to the landfill.

Explore the July August 2017 Issue
Check out more from this issue and find your next story to read.
Latest from Construction & Demolition Recycling
- Mazza Recycling adds to transfer station operations
- Michigan awards $5.6M in recycling, waste reduction grants
- Pittsburgh area mall headed for demolition
- RMDAS figures show February surge in recycled steel’s value
- US economic indicators show signs of wavering
- Northstar signs asphalt shingle supply agreement with York1
- Metso’s Lokotrack line turns 40
- Takeuchi adds dealer in Mississippi