Editor’s Note: This feature was compiled from a case study by DPR Construction Inc., Redwood City, Calif. Additional reporting was done by Jackie Gubeno.
To LEED or not to LEED? That is the question that seems to be in the minds of owners and developers across the country as they evaluate the benefits and challenges of high-performance green building.
As part of DPR Construction Inc.’s core values, it made perfect sense to pursue the U.S. Green Building Council’s (USGBC) Leadership in Energy and Environmental Design (LEED) certification for its 52,300-square-foot Sacramento, Calif., office building, owned in conjunction with ABD Insurance and Financial Services Inc., for several primary reasons:
• Walking in the customers’ shoes. As a builder of sustainable projects, DPR gained an even greater understanding of the development process from an owner’s perspective and the ability to proactively address any potential concerns or issues.
• Generating revenue through savings. DPR used the project as an opportunity to further enhance its LEED Preconstruction Cost Analysis Tool to evaluate first costs versus potential life cycle savings, making informed decisions regarding which credits to pursue and anticipated return on investment. For example, DPR determined that the additional outlay for the new building will be paid back within two-and-a-half years through water and energy savings, with an anticipated overall return of $359,758 in 2013.
• Employee health and safety. High performance green buildings are known to improve the overall health and well-being of their occupants. A recent Lawrence Berkeley National Laboratory study reported that feasible and commonly recommended improvements to indoor environments could reduce health care cost and work losses from communicable respiratory diseases by 9 to 20 percent, from reduced allergies and asthma by 18 to 25 percent, and from other nonspecific health and discomfort effects by 20 to 50 percent.
• A good corporate citizen. The basic principle of sustainable design and construction is to produce a high-quality facility that significantly reduces or eliminates the negative impact of buildings on the environment. In the U.S., we withdraw more than 1.2 billion gallons of fresh water per year from rivers, streams, reservoirs and wells. By installing innovative water-use reduction technologies and water efficient landscaping, the DPR/ABD building will reduce water use by more than 45 percent, saving more than 340,000 gallons of potable water per year.
• Practice makes perfect. Established as a technical builder committed to ongoing collaboration and innovation, DPR continuously looks for ways to advance the delivery process, demonstrate value and maximize efficiency. High-performance green building projects require detailed upfront planning, extensive technical expertise, and active participation from all members of the team throughout the project.
Based on these key factors and many others, DPR decided "to LEED" and received Silver certification for the first privately owned office building in Sacramento, Calif.
From the LEED Score based on the cost analysis generated from the LEED preconstruction management tool, DPR determined that to get the most "green for green" the project team would aim for 38 credits out of a possible 69 points, placing the project in the Silver category (33-38 points). And, of the 38 credits, 20 of them were achieved without an additional first cost. Those credits included such items as:
• Site Selection
• Public Transportation Access
• Light Pollution Reduction
• Use of Local/Regional Materials (20 percent manufactured locally)
• Use of Low Emitting Materials (adhesives and sealants, paints, carpet, composite wood)
• Indoor Chemical and Pollutant Source Control
• Daylight and Views (views for 90 percent of spaces)
• Transportation Management Plan
• LEED Accredited Professional
The team pursued another credit for Construction Waste Management—through the county’s job waste recycling program, as well as donated some of the wood temporarily used for concrete forms to a local preschool and to another construction job site.
During construction, DPR diverted debris from landfills and redirected
Triple Crown |
DPR Construction Inc., Redwood City, Calif., made sustainable building a priority with the construction of its own office building in Sacramento, Calif. The structure is already certified at the Silver level for the U.S. Green Building Council’s (USGBC) Leadership in Energy and Environmental Design (LEED) for New Construction program and at the Gold level for LEED-Commercial Interiors. The company is looking to add a third certification to its name, having recently applied for LEED-EB (Existing Building) certification at the Silver level. Some of the sustainable building features and practices DPR has incorporated toward earning LEED-EB certification include: - Having a program in place that requires any construction or renovation projects in the building to recycle at least 75 percent of the C&D debris generated; - Performing a waste audit that found 47 percent of the building’s waste was being recycled; - Achieving an Energy Star rating of 91 (91st percentile for similar buildings) for building design, HVAC efficiency and lighting controls; - Separating, collecting and recycling paper, glass, plastics, OCC, metals, batteries and fluorescent light bulbs; and - Recycling landscape debris. More information is available online at www.dprinc.com. Sponsored Content American-made Products by America HandsUnified Screening & Crushing is a family-owned manufacturer of screening and sizing media. We are proud to manufacture in the United States. Domestic weaving and a regional presence at our 14 facilities across the U.S. allow us to maintain the largest woven wire cloth inventory in North America. |
The company worked with Waste Management on its construction materials recycling, says Peggy Fischer, project manager. She says the team would comingle C&D recyclables and that Waste Management would issue a monthly recycling report for the material. Some 33 tons of wood was donated to other DPR job sites, Fischer says.
In addition, several credits are often already accounted for in the project budget due to various city, county and state regulations. For example, in Sacramento, bicycle storage is required for office buildings, gaining a point for Alternative Transportation (Bicycle Storage and Changing Rooms), and in California, smoking in buildings is not allowed, covering the Environmental Tobacco Smoke Control prerequisite. Some municipalities, such as Fairfax, Va., even offer expedited building permits for facilities seeking LEED certification, which to some owners and developers could be of great value depending upon the goals of the project.
In total, DPR and ABD spent an additional $85,112, including architect and engineer design costs, on their new $6.2 million facility (averaging $2,182 per credit), which in 10 years will generate more than $359,758 in savings based on an annual 5 percent energy and water inflation rate and a three percent maintenance inflation rate.
In addition, to reduce the environmental impacts associated with the transport of materials and to support the local economy, a minimum of 20 percent of the materials used for the project were manufactured within a 500-mile radius from the job site and did not accrue an additional first cost. In fact, depending upon the materials and location of the job site, transportation delivery costs can potentially increase overall material costs. Some of the regional materials include structural steel, concrete, metal studs, casework, aluminum storefront, paint and drywall.
GREEN THINKINGA sustainable project does not necessarily have to cost more, especially if the planning starts early, an experienced project team is in place and the goals and objectives are clearly identified and communicated.
With 54 LEED-accredited professionals on staff,
DPR began planning the project well before the November 2002 construction kickoff. Including a majority of the project team, DPR hosted a design charrette and used its own LEED preconstruction analysis tool to weigh each possible credit against the overall project budget, additional estimated first cost, and projected 10-year building life cycle return.
Following the charrette, DPR also conducted:
• Green preconstruction analysis.
• Life cycle analysis of building options.
• Environmental value analysis, including a matrix of weighted environmental attributes, such as recycled content vs. locally manufactured and rapidly renewable materials vs. harvested locally, that helped shape decision making.
The result was a comprehensive LEED scorecard and cash flow analysis diagrams that outlined the agreed upon credits and provided a working vision for a successful project, achieving Silver LEED certification for new construction. The project is also one of 30 projects nationwide participating in a pilot program that will help define a new LEED certification category for commercial interiors.
Get curated news on YOUR industry.
Enter your email to receive our newsletters.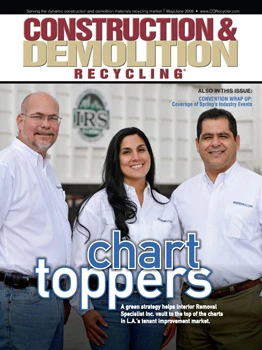
Explore the June 2008 Issue
Check out more from this issue and find your next story to read.
Latest from Construction & Demolition Recycling
- Louisiana mall could be next on demolition list
- CDRA names new executive director
- Irock promotes service manager
- Vermeer offers new horizontal grinder
- LRS expands into Indianapolis with purchase of GHW
- Superior Industries adds project sales director
- Evraz NA rebrands as Orion
- Michael Bros. announces leadership promotions