Ever notice how the winners at NASCAR and Indy races seem to change tires every time there is any slight change on the track? Pit crews have a pile of tires standing by…one for every condition.
That same philosophy can pay off for recyclers trying to maximize loader efficiency. Different tires will perform better under different conditions. Just as different pit bosses will choose different tires for different tracks, recyclers need to decide which tires work well on each job site.
"You need to look at each application—it is always project-specific," says Chuck Berg, industrial sales representative with Coastline Equipment, Long Beach, Calif. "A demolition site will be different from a dirt job. If you are doing concrete demolition and you are generating cement powder, you have to have some tread to give traction. In every case, you have to be sure the machine is under control."
While he defers to equipment reps on which tires to put on which machines, Tim Good, global customer account manager for Goodyear Tire, Akron, Ohio, agrees that the machine’s use will determine the best tire for the job.
"You have to look at the duty cycle—the length of haul from A to B and the number of times the machine makes the run," Good says.
"Once I determine the required tread depth, I look at radial versus bias tires," Good says. Assuming a pneumatic tire, the conditions on the job site will determine whether the loader requires a radial or a bias-ply tire that does not flex as much.
"If the work cycle is fast enough, go with a radial," he advises. "If the job site is pretty clean, a radial tire is a good product," Good says. "If you are getting sidewall puncture, go with a bias tire. Bias sidewalls stand up straighter and don’t bulge out," he explains.
While Goodyear sells pneumatic tires, there are a lot of people who swear by solid or foam-filled tires in tough conditions.
"We do a lot with tires that are puncture-proof, especially in the demolition industry where there is the constant possibility of tire damage due to re-bar, wire and other material on the site," says Al Springer, Cleveland branch manager for Company Wrench. The company also has locations near Columbus, Ohio, and in Plant City, Fla., where it sells Komatsu and Gehl loaders. Springer recommends a solid or foam-filled tire on such applications.
"It depends on the conditions where you will be working, but if there is debris, we’d recommend a solid or a regular tire with foam filling," he says, adding that his company sells a lot of McLaren NuAir and Setco tires.
"If I had to choose one tire to do it all it would be a soft ride, staggered gear load, eight notches per side tire," says Bennie McGill, Midwest sales rep with Setco Solid Tire, Idabel, Okla. "But when you are talking tire or tread design, keep in mind that you are working in all kinds of situations, and no two job sites are the same," he says. "You need enough traction to do the job, but not more than the job requires."
"I try to find out the issues the operator has before talking about tires," says Jerry Bruner, regional manager with Advance Tire, Millstone Township, N.J., which sells TY solid tires, including "soft ride" tires. On C&D sites, cutting and puncture hazards are the big hassles. "Pneumatic or radial tires don’t work well in an environment with broken concrete and steel. They’ll ruin a tire worth several thousand dollars."
Berg notes that re-bar bedevils tires that have any kind of apertures. "You need a solid tire. You don’t want any apertures," he says.
At a landfill site, he cautions against using tires that will cut and chunk out. "No matter what happens, you are going to cut the tire," he says. "But you don’t want it to chunk out on you."
Berg advises recyclers not to consider price alone when choosing tires, as the cheapest option is not necessarily the best for a given application.
McGill, whose company used to make foam filled tires, advocates solid tires over foam filled. "Foam filled is only as good as the container that holds the foam," he says. He notes there are many different quality levels of solid tire. "Invest in a good, solid tire and it will outperform foam filled three-to-one," he says.
"We switch the tires to a solid tire from SG Revolution," says Lee Gibson, Gibson Machinery, Oakwood, Ohio. They sell Doosan equipment (the former Daewoo).
Gibson says that his customers report that the solid tires seem to hold up well. "It seems more people go with the solid over the foam filled since they last longer," Gibson says.
Bruner says that the C&D environment is not a high-wear environment. Nor do operators often face problems like chemicals and oils that often damage tires at a MRF. "There is not a lot of wear. The sad thing is that often 50 percent of tread is left when a tire is ruined." He says recyclers should spend some extra money right at the start to get a good tire and then not have to worry about replacement and downtime later on.
SWITCHING TREAD PATTERNMany sources contacted say no one tire will fit all. In fact, it can pay to switch out one kind of tire for another. The break-even point is probably anything over a couple of days use on one surface.
"It depends on how long you will be on the job site," Springer says. "If you are going to be on a job a long time, using the right tire will give you better wear characteristics," he continues. "You won’t eat up the tires as fast."
He says that many of the recyclers he deals with have a couple of sets of tires and they will switch them out as they move to different work environments.
Berg agrees that the right tread pattern is vital. "If you are moving up a ramp with a chance to slip, you need a modified tread with some grooves," he says. If the job involves a lot of high speed, back-and-forth transport on a reasonable surface, he would stay away from solid rubber. "If you’re just feeding a crusher, you probably don’t need solid rubber," he says. On the other hand, in conditions where damage is a certainty, a solid tire is required, he says.
Good says tire pressure is a key factor—and how much tolerance you have varies with radial and bias tires.
If the job requires moving a lot of heavy material, the tire’s sidewall load can be exceeded by 7 percent on a bias tire or 14 percent on a radial, he says.
Some recyclers look to the general-purpose tire, expecting it will work sufficiently well on solid surfaces, dirt and aggregate bases. "General purpose lugging doesn’t have great wear characteristics on any one type of surface," Springer says. But it has its uses.
"If you are just running the equipment for a day or two, it will not pay to change out tires. "However, if you are running a three-yard loader at a crusher for a month, it definitely will pay to change out the tires," he adds.
McGill says that some people do change tires but it is not standard policy for most C&D workers. "Labor is too costly to shut a machine down to change tires—especially on a loader," he says. While he has customers who will change from a slick to an air tire, he says the reality is that a C&D operation is better off having two machines, each with job site-specific rubber.
If the loader will be run on a smooth pad, like a concrete surface at a crusher, Springer will recommend a smooth tire. "You will find you get better wear than with a lugged tire," he says.
A set of four, lugged 12x16.5 tires for a skid steer might run $1,200, but the investment will pay off. A set of 15-inch NuAirs will cost $3,200. But the switch-outs are worth it, Springer says.
In loose, sloppy conditions, he tells recyclers to go with an L-4 lug type. "If you are operating on aggregate, we’d use an L-5," he continues.
Good notes that a deep tread, like that on an L-5, will be more difficult to puncture than the shallower tread on an L-3 or L-4. "L-5 is meant for a rough surface," he adds.
Slick tires are probably the most cost-effective in many cases but they do not perform well in muddy or sloppy conditions.
Choosing the proper tire and running it properly not only enhances tire life but also means that a tire is a better candidate for retreading. A good casing is required for a tire to be retreaded. However, in the C&D environment, the percentage of tires that make the grade is pretty small.
Bruner says he sees too many tires on the toss-out heap that have 50 percent tread left but which are damaged beyond use. "We encourage our customers to re-cap our tires," he says. However, he would agree with Good, who says that not many C&D tires survive the harsh work environment to make it to a second incarnation.
FUEL SAVINGS?If you are looking for a lively lunch-hour discussion, get a few contractors together and ask whether solid tires or foam-filled tires affect fuel consumption on a wheel loader or skid steer. Given fuel prices today, it is more than idle speculation. Most will tell you that it makes sense that different tires should give different efficiencies. However, few have any empirical data.
"I’ve never heard that there is any fuel savings with different tires," Springer says. "With the right tire, you might get less skidding with a solid tire than with a pneumatic one," he speculates. Berg also points to the efficiency of operation gained with using the right tire as a potential source of fuel savings.
"In theory, there should be a 1 or 2 percent gain for solid tires—but it wouldn’t be much," McGill says. He notes that the figure could drop to minus 1 or 2 percent as the tire gets smaller.
Good agrees that proper tire choice probably effects fuel consumption. However, he says that other factors—such as air pressure and operator habits—have a big effect on fuel consumption, too.
"Most people do not track fuel use," Good says. However, he says he expects that some solid research will be forthcoming.
Bruner says he doubts there is much difference in fuel consumption, unless it comes from running solid tires right down to the nubbins and the loader has to burn a bit more fuel to get those extra revolutions than it would ordinarily.
"The biggest variable is the operator. You get a cowboy operator and machine wear, tire wear and fuel usage all go up," McGill says. Running the machine right makes a bigger difference in fuel consumption than tire type, he adds.
Meanwhile, Good recommends maintaining the proper air pressure in any pneumatic tire as a good way to maximize both fuel consumption and tire life. "Any time the air pressure is down, it will increase rolling resistance," he says. That’s a killer, whether on a loader or the family jalopy.
The author is a contributing editor to C&DR and can be reached at curt@curtharler.com.
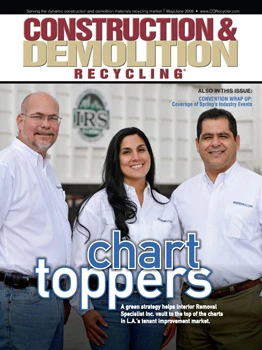
Explore the June 2008 Issue
Check out more from this issue and find your next story to read.
Latest from Construction & Demolition Recycling
- US Senate backs reduced cuts to EPA
- US EPA offers brownfields-related funding
- Sky Quarry seeks crowdfunding support
- Caterpillar releases the new Cat 980 GC Wheel Loader
- NAPA leaders participate in USDOT roundtable
- Yanmar CE launches full line of compact equipment
- Metso reports increased orders after flat H1
- Block Island Recycling Management Inc. aims to promote environmental stewardship