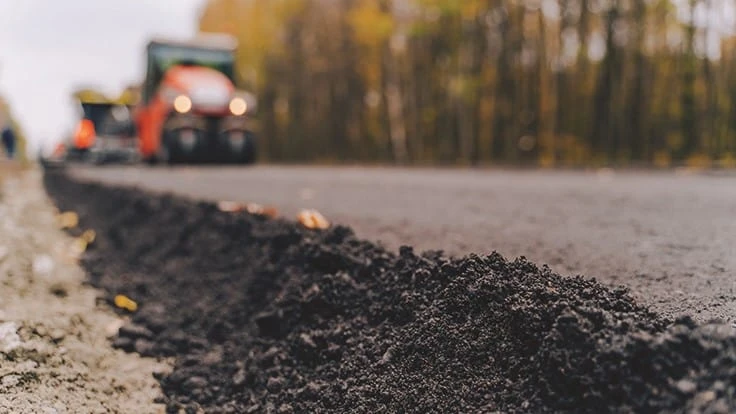
The use of recycled asphalt shingles (RAS) in asphalt pavement has become increasingly popular among paving contractors seeking a cost-efficient alternative to virgin materials. Consisting of asphalt cement, aggregate and fiber, the composition of RAS can make it an ideal substitute for the virgin asphalt and fine aggregate routinely used in hot mix asphalt (HMA) formulations.
According to the National Asphalt Pavement Association (NAPA), asphalt mixture producers used more than 1 million tons of RAS in asphalt pavement mixtures during the 2018 construction season, and in the process, diverted about 10 percent of the total available supply of waste shingles from landfills.
While this was a 12.5 percent increase from the 980,000 tons used in 2017, it is only a fraction of the approximately 11 million tons of asphalt shingles disposed of each year.
In an effort to further the sustainable practice of utilizing RAS in asphalt mixtures, NAPA released an updated report in 2019 on the use of reclaimed shingles in asphalt pavements. The report, which was an updated version of the association’s “Guidelines for the Use of Reclaimed Asphalt Shingles in Asphalt Pavements,” laid out a number of best practices associated with RAS usage.
“I think the big thing that we just have to encourage is if you’re going to use this material, then you’ve got to do your homework,” Richard Willis, vice president for engineering, research and technology at NAPA, says. Willis was also a co-author of the report. “You have to know your material properties, such as your typical aggregate and binder, as they become even more important [when using RAS in mixtures].”
COMPOSITION
Although the composition of asphalt roofing shingles can vary depending on the manufacturer, shingle age, product line and roofing application, most contain a basic mix of asphalt binder, filler, fine aggregate or granules, and fiberglass or organic felt.
“[Practically] every asphalt mixture that we make has two of those same ingredients in it. You’ve got the asphalt binder and you’ve got some kind of fine aggregate that’s involved in the fines system,” Willis says. “When you’re looking at using the shingles in an asphalt mixture, we use them in very small dosages because your typical shingle is going to be somewhere between 20-30 percent asphalt binder depending on how old it is and what type of fiber was used with it.”
The aggregate or mineral granules on the surface of the shingles are often very durable and angular, which can be desirable for incorporation in asphalt mixtures. In addition, the surface aggregate in shingles can create added voids in mineral aggregate (VMA) in the asphalt mixture.
According to NAPA, achieving proper VMA in asphalt mixtures is a key part of meeting the volumetric properties needed to ensure a strong aggregate skeleton, the ideal amount of asphalt binder and proper air void space to provide optimal performance against cracking, permanent deformation and aging.
“When using shingles, it all comes down to ensuring these mixtures are engineered well,” says Willis.

SOURCES
Waste shingles used for the production of RAS are usually sourced from two major categories—post-consumer asphalt shingles (PCAS) and manufacturing waste asphalt shingles (MWAS).
MWAS, which is typically generated from manufacturers scrap, is often preferred by processors because it is free of many contaminants such as nails, wood and asbestos that might compromise PCAS composition. However, with sources of MWAS limited by geographic availability, many producers are left with only PCAS as an option.
According to NAPA, processors of RAS end up using PCAS volumes 10 times greater than that of MWAS thanks to its availability, which is usually derived from reroofing activities.
While NAPA recommends shingle recycling operations consider local, state and federal requirements when addressing contamination, the association has identified two basic modes for acceptance of PCAS.
Source separating requires the roofing contractor to deliver only clean PCAS to the recycling facility. According to the report, the shingles should be free of wood, plastics, large scrap metal, dirt, rocks, adhesives, solvents, petroleum contamination, other trash, and other substances deleterious to the shingle recycling processes.
“Most of the specifications when you look at them do have a requirement for what we would call ‘deleterious materials,’ and that’s basically our way of assessing contamination,” says Willis. “We have pretty tight specifications and requirements that states set out to ensure that these materials are clean, but it is a continual process as we figure out how to make them cleaner.”
Mixed roofing waste loads, on the other hand, require sorting the PCAS from the waste at the recycling facility. These can vary from simple “dump and pick” operations to more elaborate systems with screens, conveyor systems, and elevated picking stations to remove non-shingle materials.
PROCESSING
To produce RAS, sorted shingles are fed into a grinder or shredder to be processed. The ground or shredded shingles then pass through a screening process where material of a specified size is stockpiled for use in asphalt pavement mixtures.
NAPA states there can be some variance with what grinders or shredders may be used to process shingles, with each manufacturer utilizing a unique combination of material-handling and size-reduction designs.
In general, the grinder will include a loading hopper, a feeding drum to move the shingles into the grinding chamber, a grinding chamber with cutting teeth, a sizing screen and an exit conveyor.
To combat the excessive heat generated during the shredding or grinding of shingles, Willis recommends adding water to the shingle material as it is fed into the grinding chamber.
“Because you’ve got very stiff material that you are grinding at very rapid speeds, one of the challenges that you see is you have a lot of heat that’s developed,” he says. “With asphalt binder, as it’s exposed to heat, it gets softer. So, to really prevent it from gumming up the system, they use the water to process and keep it cooler to help the system stay active and running smoothly.”

MIXTURE
RAS contains stiffer asphalt binder, fibers and filler, as well as hard, durable and angular aggregates. With this is mind, several studies have illustrated the importance of accounting for recycled binder properties when incorporating RAS into an asphalt mixture design.
According to the American Association of State Highway and Transportation Officials (AASHTO) Standard Specifications and Standard Practices for using RAS in asphalt mixtures, there are three areas to address when utilizing recycled shingles: shingle aggregate gradation and specific gravity, binder quantity requirements for effective asphalt, and binder quality requirements for binder embrittlement.
Of these guidelines, some research has found that increasing the VMA requirements will increase the total and effective asphalt binder in the asphalt mixture. This is because the asphalt binder in RAS does not fully liquefy during asphalt production, leaving a portion of RAS asphalt binder that does not become effective during production.
In addition, the AASHTO MP 23-15 specification requires RAS be processed so that 100 percent passes the 3/8-inch sieve to optimize blending. Variations in processed RAS gradations have resulted in a range of RAS asphalt binder effectiveness when mixing with new asphalt binders. Generally, finer RAS gradations lead to higher effective asphalt contents.
“States and areas are starting to look at not just developing a recipe for these mixtures, but also starting to incorporate some tests that will allow people to have higher confidence that these mixtures are going to perform,” Willis says. “That may allow people to open up their specifications of their standards a little bit.”
This article originally appeared in the July/August issue of Construction & Demolition Recycling. The author is the assistant editor for Construction & Demolition Recycling magazine and can be reached at hrischar@gie.net.
Latest from Construction & Demolition Recycling
- Liebherr appoints managing director of Liebherr USA Co.
- Construction hiring slowest since early pandemic
- Metal roofing sector sees growth opportunities
- Liebherr brings heavy iron to NDA convention
- Viably named authorized Diamond Z distributor in California, Arizona and Nevada
- New York legislators propose resolution to revoke landfill operating permit
- Smarter, faster, safer
- Case adds dealer in Alabama