The Armed Forces Retirement Home tower in Gulfport, Miss., was imploded on Oct. 25, 2007, to make way for a new home for military retirees. More than 400 veterans lived at the AFRH Gulfport facility prior to Hurricane Katrina. The veterans were evacuated and relocated after the destructive winds and storm surge forced the closure of their home in August 2005. The 11-story high rise that overlooked the sandy beaches of the Mississippi Gulf Coast is now only a memory.
STEP-BY-STEP
The Home was established in 1851, the first national soldier’s home in the United States and the only one of its era in operation. The property served as a Civil War hospital and signal station and was the summer retreat of U.S. presidents from the 1850s through the 1880s. President Abraham Lincoln is thought to have penned much of the Emancipation Proclamation in the "Lincoln Cottage."
The first phase of the AFRH project was the asbestos abatement. It took CST Environmental Inc., headquartered in Brea, Calif., four weeks to complete the abatement. More than 150,000 square feet of asbestos-containing materials were removed.
The second phase of the project was the interior gut of the first floor and demolition of approximately 75,000 square feet of surrounding structures. A lot of work goes into preparation before the explosive engineer, Dykon Enterprises of Tulsa, Okla., can place the first charge. The interior walls, ceilings and doors were stripped away leaving nothing but the structure. Taking out the first floor to weaken the structure was most critical in getting the building to collapse. The charges placed on the upper floors helped control the direction and break up debris for easy removal of the 360,000-square-foot-structure. During this phase, CST removed and recycled the majority of the ferrous materials.
The third phase of the project was preparation for the implosion.
BLAST-OFF
After the building was sufficiently stripped and pre-weakened, CST drilled holes for the explosives. Heavy equipment was brought in to bore through the solid concrete columns. Jim Redyke, president of Dykon Enterprises explains, "Placement of the holes was critical, as the charges must be precisely placed to ensure a successful implosion. The project required approximately 300 pounds of explosives."
CST prepped the interior beams for linear copper clad shape charges. Dykon Enterprises precisely placed each shape charge. A linear shaped charge (LSC) is a continuous explosive core enclosed in a seamless metal sheath. The LSC’s continuous linear explosive produce a linear cutting action. Each LSC was wrapped in a reinforced box with layers of reinforced chain and a heavy geo-textile fabric. The heavy fabric kept flying debris to a minimum. This was necessary to ensure that other nearby charges were not harmed. The reinforcement was necessary to force the energy of the shape charge to cut the steel beam. The explosives were set on time delays to minimize the shock wave. Conventional explosives were placed vertically on the columns to shift them out of position. The precise placement of LSCs and conventional explosives brought the 11-story building down in less than 10 seconds. "The most challenging aspect of this project was the elevator shaft and the stair towers. They were poured in place concrete and very unique for this type of structure. Typically the elevator shafts and stair towers are on a steel frame. We took extra measures to ensure this implosion was a success," explains Redyke.
The fourth phase of the demolition project is final clearing of the implosion debris and site grading. This phase of the project is currently underway. CST will separate the remaining scrap metal and construction debris and process the remaining concrete for offsite recycling. Finally, once the slab is removed, CST will grade the site.
CST mobilized initially with asbestos abatement and salvage crews with small equipment. At the height of demolition, five excavators, one track loader, three skid-steer loaders, two sheers, grapples, two 25-foot man-lifts, a fleet of hauling trucks and a crew of up to 60 laborers will be utilized to complete the project.
CST hopes to recycle approximately 70 percent of debris weight of material including masonry brick, concrete, ferrous and nonferrous metals at the completion of this project.
According to the City and Regional Planning Program College of Architecture Georgia Institute of Technology, construction and demolition waste is currently recycled at a rate of 20 percent to 30 percent. Project-based studies indicate that the potential for recycling is more than 70 percent.
The entire environmental abatement and demolition schedule will take 135 days to complete. "This is a very aggressive schedule, but CST is up for the challenge," explains CST’s Vice President John Jenkins.
This article was submitted on behalf of CST Environmental Inc., Brea, Calif.
Get curated news on YOUR industry.
Enter your email to receive our newsletters.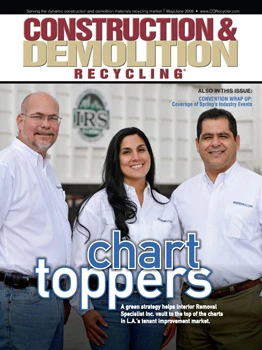
Explore the June 2008 Issue
Check out more from this issue and find your next story to read.
Latest from Construction & Demolition Recycling
- WasteExpo transitions to biennial format for enhanced experiences
- Case adds dealer locations in Western US
- RMDAS April figures show recycled steel price setback
- Metso’s profits narrow, but crusher orders solid
- New recycling grant program launches in Massachusetts
- Greenwave closes 2024 books with red ink
- Steel Dynamics nets $217M on record shipments
- Massive Chinese steelmaking rebound recorded in March