
Since 2008, the demolition industry has seen a recession in projects and revenue, but many companies believe this year is the year of building up, or perhaps, tearing down.
In the Midwest and Southeast, if projects aren’t picking up, they are at least steady. While the Midwest mostly deals with industrial projects, such as power plants and auto plants, the Southeast deals with commercial demolition because of the abundant theme parks and other tourist attractions.
Because of the Midwest’s inclination toward industrial projects, scrap prices are creating a difficult recovery process, while concrete recycling is booming in the Southeast because of its necessity.
In the West, particularly among the Rockies, demolition companies are going through an economic boom with large population growth causing the need for more redevelopment.
“All in all, the industry is changing,” Richard Lorenz, CEO and president of Central Environmental Services, Orlando, Florida, says.
THEME PARKS AND TOURISTS
Central Environmental Services has been a family-owned business since 1964 that specializes in interior strip-outs, residential, industrial and commercial demolition. While business has been rising within the last year in Florida, Lorenz gives the credit to surrounding theme parks that are constantly under construction.
“We’ve reached a tremendous amount of people visiting,” he says. “All the construction, clearing and revamping for theme parks will bring millions and billions of dollars.”
In terms of the other industries, vacant shopping centers, hotels and motels are the biggest contenders. Lorenz says that companies around Orlando are starting to get jobs for hotels that were built when Disney World first opened. The lack of industrial jobs, he says, is because of low scrap steel prices.
Central Environmental Services recycles at least 80 percent of every structure it tears down, Lorenz says. That includes almost all the scrap the company can find, from conduit to brass faucets.
The company has a 30,000-square-foot recycling area where 65 different materials are sorted by hand.
Because of these extremely low scrap prices coupled with the lack of structures, Lorenz says he doesn’t do much with industrial jobs.
“We did some work with NASA and SpaceX, who is buying old NASA buildings and paying us to gut them,” he says.
The most popular material in the South, he says, is concrete. The lack of mines or pits to recover virgin materials for concrete creates the need for recycled products. For big projects, such as the privately funded, $6 million, six-year Interstate 4 (I-4) Ultimate Improvement project, as much as 7 million tons of recycling concrete will be needed.
“In the last two to three years, the guys that are crushing cannot keep up with the demand,” Lorenz says.
Central Environmental Services recently demolished a race track at Disney World and recycled every concrete item it could using portable crushers. They sold the aggregate back to the general contractor and Disney.
But generally, the company likes to keep projects on the smaller scale, Lorenz says, because the smaller projects allow for faster pay.
“We just got done doing a ‘whale,’” he says. “We just finished clearing and wrecking a 500-foot-wide swath so the state can build a highway extension. That was a $3 million to $4 million job and we’re still waiting to get paid in full.”
MIDWEST RESIDENTIALS
While the southern United States focuses on theme parks and commercial buildings, Homrich Inc., Carleton, Michigan, is experiencing an increase in blight demolition.
According to Vice President of Operations Timothy Homrich, the company is currently under contract to demolish around 475 blighted homes in Detroit.
The money comes from the Hardest Hit Fund, where more than $90 million worth of contracts have been awarded to local demolition companies. In the last two years, the funding has allowed 9,375 vacant homes to be demolished.

“It was the mayor’s (Mike Duggan) number one focus,” he says. “To get the funding and run the largest demolition project in the country, mostly with blight demolition.”
Homrich Inc. is usually able to recycle around 90 percent of its materials and melt collected ferrous and nonferrous metals, then sell them to local steel mills. But lately, scrap’s prices have made purchasing unappealing and have kept the company away from industrial projects, which is usually status quo for the Midwest.
“It’s stable, but unstable,” he says. “It came back up here in the last few months, but it’s expected to drop again, and it affiliates with owners not wanting to dig out of their own pocket.”
The company works primarily throughout the Midwest, down to the Tennessee Valley where it is a preferred contractor for the Tennessee Valley Authority. The company also is currently wrapping up the demolition of Cleveland Heights High School in Cleveland, which is a selective demolition where the new school will be built around historic remnants. But the busiest area for the company remains in the Detroit area.
“When you work closer to home, you don’t get too aggressive or get too far away,” Homrich says. “We didn’t notice anything that would drive us away from other markets.”
CHICAGO STEEL
In Chicago, both Brandenburg and Hayden Wrecking are experiencing similar patterns. Both companies focus on industrial demolition and have seen the impact of ferrous metals prices on their businesses.
“Ferrous has been on a slow decline until five or six months ago,” Dennis McGarel, vice president of sales for Brandenburg, says. “It’s leveled off pretty steady and had an uptick, but there’s word that it’s coming back down.”
That creates a challenge for companies that count on ferrous metals as revenue, he says. Meanwhile, owner of Hayden Wrecking, Brian Hayden, says that ferrous metals have been stronger this year while other materials like concrete have been level.
McGarel cites the U.S. Environmental Protection Agency’s (EPA) coal combustion residuals (CCR) regulations as one reason for an increase in the industrial sector. The CCR regulation aims to reduce the residual fly ash, bottom ash or boiler slag created from coal boilers in industrial applications.
“I can’t tell you how many bids come out for power plants because of the EPA regulations,” McGarel says. “Mining sites have closed down. There’s multiple facilities for each company, and a lot of them are going down at the same time.”
Brandenburg cleans up the mining sites and creates a track record that appeals to facilities owners when the time comes to demolish. Hayden wrecking in currently working on dismantling precipitators and dryers.
WHERE METRO MEETS FRONTIER
While the Midwest experiences difficulties with materials and projects hold-ups, Fiore & Sons Inc.’s Business Developer Tim Mangnall says the Denver-based company has its fingers in all the pies.
“There’s a lot of demolition going on in all facets, from schools to residentials, to multifamily development and warehouses,” he says. “It seems like the Denver economy is strong and growing very fast.”
Millennials and their desire to move to the downtown Denver area keep the company busy, with the city growing by 9,000 to 10,000 people per month. This keeps Fiore & Sons busy in the metro area, but Mangnall suspects the future of the company will lie in the suburbs of the city.
“As [the millennials] get older, they’ll want to start families and move out into neighborhoods,” he says.
The company recycles about 70 percent of its materials, he says, and much like everyone else in the United States, the West is feeling the scrap metal price drop. “But it’s a matter of supply and demand,” he says. “We try to recycle anything that is recyclable and that is cost effective to recycle.”
POLITICS IN DEMOLITION
The largest concern among the demolition industry, though, is the upcoming election. Come November, the economy could be changed completely, or it could stay the same, depending on who wins the election. Because of that uncertainty, many building owners are putting projects on hold.
“The biggest deal is seeing what happens in November and after November,” Mangnall says. “Who knows how that’s going to affect everything.”
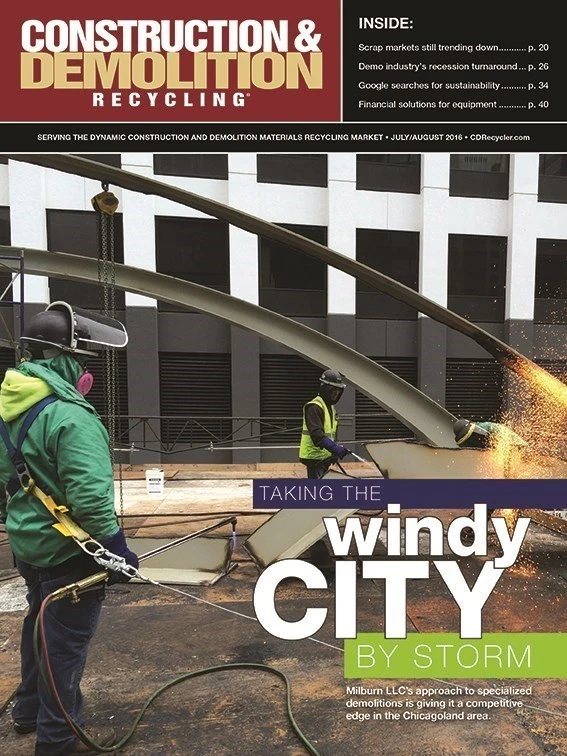
Explore the July 2016 Issue
Check out more from this issue and find your next story to read.
Latest from Construction & Demolition Recycling
- Radius to be acquired by Toyota subsidiary
- Pacific Steel selects Danieli as EAF equipment supplier
- Viably, Turmec partner on Ohio installation
- EPA plans to revisit numerous environmental, climate regulations
- Connecticut recycling facility looking to accept C&D faces local pushback
- Fornnax wins Green Innovation of the Year award
- ABC: Construction backlog inches lower, staffing levels expected to grow
- Former detention center in Cleveland set for demolition