The work performed by Interior Removal Specialist Inc. (IRS), South Gate, Calif., is often performed for demanding clients, and almost always takes place on a tight deadline.
The primary mission of IRS involves converting one or more floors of constructed corridors, common areas, and offices found in office towers and facilities all over Southern California into a "plain vanilla shell," in the words of IRS owner Carlos Herrera.
He and the nearly 200 associates of IRS have become a leading provider of this type of demolition service in Southern California not only by performing outstanding work in amazingly short periods of time, but also by maximizing the recycling of materials that do not always lend themselves to easy recycling.
THE GROUND UP
"I’ve been recycling my whole life," states Herrera, who says that when he was growing up his mother involved the whole family in the collection and sale of recyclable cans, bottles and newspaper.
His mother supported the family with her recycling ventures, often making
Furnishings With Heart |
Recycling materials, such as drywall, carpet and ceiling tiles, is one way Interior Removal Specialist Inc. (IRS), South Gate, Calif., has attained a 72 percent recycling rate. Another way the company diverts material from the landfill is by saving and storing the furniture and equipment left behind by former tenants. The company stores such items and makes them available to not-for-profit organizations. "We’ve built churches and chapels in Mexico with our materials," says Carlos Herrera of Interior Removal Specialist Inc. (IRS), South Gate, Calif. Adds the company’s Richard Ludt, "We sent an entire industrial kitchen to a Romanian orphanage." Other recipients have included Hindu monks, housing projects in South Central Los Angeles, and film school students, who can help furnish their sets with IRS’ inventory. The undertaking is not profitable, and the company does not even attempt the accounting process of tracking and writing-off tax deductibility for the donations. While the financial rewards may be limited, there is a spiritually satisfying aspect to IRS’ activities. "One of the favorite parts of my job is going back to our warehouse with a non-profit representative, and they walk into what is basically an Office Depot without a cash register—it’s a great feeling," says Ludt. "Certainly being there when the man who was trying to furnish the Romania orphanage saw our kitchen equipment, and he fell to his knees and cried, that was a terrific moment." |
Starting his career as an elevator operator with Westgroup Partners, a Seattle-based real estate developer, Herrera gradually learned how to perform on-site demolition work where he noted the value of the scrap materials. Herrera informed Westgroup they were overpaying for projects based on the recyclability of the materials and their worth at the back end of the job. His observations and honesty enabled Herrera to work his way up to being a crew leader and then site superintendent. "I learned about building management by day and worked with retrofit crews by night."
When the Seattle-based developer sold its Southern California properties, he used his severance pay to enter into a partnership and start his own demolition company. When that partnership dissolved, Herrera started Interior Removal Specialist Inc. in 1994.
With a crew of 20 hard workers, one truck and an office located in a shipping container, the journey to position IRS as the market-leading tenant improvement (TI) interior demolition specialist in Southern California began.
The management team at Interior Removal Specialist now includes family members such as his sister Vicky Herrera, who oversees all company operations, and Ernesto Herrera, Carlos’ son who works in the estimating and worksite safety departments of the company.
More recently, a key part of the management team has been Waste Management Administrator Richard Ludt, who came to IRS in a roundabout way. Ludt previously worked in the film industry as a key grip and dolly grip on various film crews until 2001 when much of the film work had moved out of Hollywood and into Canada and neighboring states. Ludt heard that Herrera was interested in hiring someone to put together a corporate video and a new Web site for the company. During that process Herrera offered Ludt full time employment with IRS. Says Herrera "At first I brought him in to do the video, but I knew in my heart and in my gut that Richard was a person that I wanted to have work at IRS."
As Ludt remembers it, the transition wasn’t completely smooth. "Two months after I was hired by Herrera, I got a call to work on location for a video shoot. I fell off of a ladder and shattered my foot. Carlos paid me for nine months to sit behind a computer and learn about Assembly Bill (AB) 939 and other California recycling laws," Ludt recalls. "I was way overpaid to sit there and get the equivalent of a college education on Carlos’ time."
Ludt says that experience is indicative of the way Herrera has recruited and managed the IRS team. "He believes in his team," says Ludt. "It doesn’t matter who you are or where you come from, if you believe in yourself and in the vision that Carlos has for IRS then we can achieve our goals together. Nobody at IRS is better than anybody else, and that includes Carlos. Carlos breeds loyalty." A large percentage of the IRS workforce has been with the company for more than 10 years, and many from the original 20-member workforce are still with IRS.
When hiring Ludt and others at IRS, there was a lot of up-front training involved before such people yielded a return for IRS, but Herrera followed his instincts to achieve the payoff. "Our people are everything. Our success is really more about them then it is about me. We couldn’t do what we have done without the pride of ownership we all feel, from the receptionist to the guys in the field. It’s a big part of what we’re about—if the attitude is right, we can teach you the skills," says Herrera." His approach to recycling has been similar.
TOUGHEST TASKS FIRST
The interior renovation activities of IRS yield about 900 tons of gypsum drywall per month and 240 tons of acoustical ceiling tiles per year, as well as considerable amounts of carpet, padding, and laminate materials such as counters and desks. The company’s materials stream is not rich with the structural steel and concrete that can yield tons of commonly recyclable material to create an impressive landfill diversion rate. Many recyclers seek out materials with the most reliable, established markets and tend to avoid handling or deferring action on materials with emerging markets. Partly because of the nature of tenant improvement work and partly because of the determination shown by Herrera’ staff, that has not been the IRS approach.
The foremost benefits of IRS’ recycling efforts thus far have been positive public relations and what could be termed spiritual rewards. "Most of the stuff we’re recycling does not earn revenue," according to Herrera. "On drywall, we just about break even; ceiling tile is labor intensive and probably costs us, even though Armstrong has honored us as a leading recycler."
"We have won several international awards for recycling from organizations like SWANA and ISWA (International Solid Waste Association), plus awards from the California Resource Recovery Association and a Governor’s Award—all for basically doing what’s right," says Ludt.
IRS is a member of the Construction Materials Recycling Association (CMRA), the United States Green Building Council, and the Solid Waste Association of North America, where Ludt currently sits on the International Board as the Corporate Director of Recycling and Material Recovery. IRS seeks out LEED (Leadership in Energy and Environmental Design) projects and has become known for their ability to achieve real diversion from the interior C&D waste stream.
Earning LEED points on a tenant improvement project is not easy, without that low-hanging scrap metal and concrete portion. But tapping into the LEED market has been critical. "LEED and the environmental focus is the driving force behind so much of what’s going on in the market," notes Ludt.
The company’s crews and employees largely keep materials separated on the job site and can perform further sorting at its 7-acre site in South Gate. The IRS facility is the only facility in California that is concentrating on strictly interior debris, and the 73 percent diversion rate they have achieved did not come from the traditional concrete and dirt, which makes up only about 10 percent of their incoming debris by weight.
"As the old saying goes ‘It’s not about the money, but it’s the money’" says Ludt, who became a LEED Accredited Professional in January of 2005. "It’s the right thing to do, and if we’re serious about recycling these materials, we need to get past the low-hanging fruit. That’s the only way we can create new markets in this industry. We have proven that you can recycle this waste stream and still remain profitable."
The company’s new 7-acre site may allow it to add automation aspects to its recycling efforts. "We’re still very much in the infant stages of creating a recycling facility," says Ludt. "We’re permitted to handle 500 tons per day, and we have added two scales, a wheel wash system, and a radiation detector to help handle the inbound material from our jobs. When our ramping up period is over, we will be able to take in the full 3,000 tons per day we are permitted for."
The company’s ability to handle the hard-to-recycle portion of the C&D stream is also drawing outside interest. "The day after we received our full solid waste facility permit, someone from the L.A. County Sanitation Department wanted to know when they could send trucks," Ludt says. "Other cities have expressed an interest in our opening date because they have been impressed with our diversion and our unique approach to the tenant improvement waste stream."
The facility operates around the clock. "Even though our current sort line is small, we have the ability to run two separate streams," says Ludt. IRS is achieving a 73 percent recycling rate on its interior demo (also known as "soft demo") stream. If it accepts loads with a more traditional C&D mix, that can only help. "If we start seeing more metal and clean wood, I fully expect that we can hit a 90 percent recycling rate."
Another way IRS diverts material from the landfill is by saving and storing the office furniture and fixtures that are left behind by former tenants and finding worthy homes for it. [See the sidebar "Furnishings with Heart" on page 34.]
PRACTICING WHAT IS PREACHED
It can take time for the nuts and bolts operations to catch up with the foresight and philosophy that managers envision in their long-range plans.
To an observer of Interior Removal Specialist, it is difficult to separate the broader philosophy from what takes place each day.
From the start, Herrera has offered people the chance to be rewarded for hard work, and has led by example by pouring his own energies into the company seven days a week. "I’m a workaholic. My hobbies? They’re demolition and recycling," quips Herrera. Ludt adds, "It seems like I get a call at least once a night from Carlos with one of his new ideas for the company."
Often times employees are engaged in a tough job where work is done with hand tools and usually involves kicking up dust (for which containment systems are brought onsite) and a lot of scraping, sawing and lifting. Herrera acknowledges. "These guys should be on ‘Dirty Jobs. We work nights, weekends and holidays when other tenants are not in the building." [See the online sidebar "Quick Change Artists" at www.CDRecycler.com.]
The IRS approach is for its crews to be as clean as their jobsights. Everybody in the field wears the same uniform: green IRS T-shirts, always tucked in, along with white hard hats. The politeness of crews as they work is stressed. "Good morning, thank you, you’re welcome,’ that’s important," says Herrera. "This is all stuff we learned by the second grade, common courtesy and manners go a long way."
Herrera and Ludt are always on the lookout for workers who can take on added responsibilities and who deserve to be rewarded. "Carlos has always said, ‘We don’t have employees, we have co-workers, and every member of the team knows that they are an integral part of the company. If you work hard and do your best, you will be rewarded,’" notes Ludt.
IRS’ operating methods have allowed the company to quickly become the leader in the Southern California tenant improvement market. "We demolished nearly 12 million square feet of space in 2007 and earned $16 million in revenue," says Ludt. "We have approximately 200 coworkers, yet we’re still run like a family company."
Associates at IRS credit Herrera for his ability to manage and motivate loyal people in order to provide customers with results that create customer loyalty. Ludt explains it this way, "What a lot of people say about Carlos is, ‘Nobody’s that nice—people like that don’t exist.’ He inspires people to give their best—you want to do your best because you want to see Carlos smile. You want him to be proud."
He continues, "Carlos doesn’t expect perfection, but he expects your best work. He gives people the freedom and power over their own surroundings to make them want to do their best. It’s not about someone standing over their shoulder; it’s about them looking in the mirror."
Herrera adds, "Seeing our people excel is part of what keeps me going. Sometimes I motivate them by asking them to meet a tough goal, but ultimately I believe in taking care of people."
Working together to achieve tough goals has been a strategy that has allowed IRS to flourish for more than a decade, and new challenges seem just as likely to keep Herrera and his co-workers going strong.
"The easiest way to get something done is to tell Carlos he can’t," says Ludt. "Other people told Carlos he couldn’t build this company this fast or recycle the materials we generate, and it hasn’t slowed him down at all."
The author is editor in chief of C&DR and can be contacted at btaylor@gie.net.
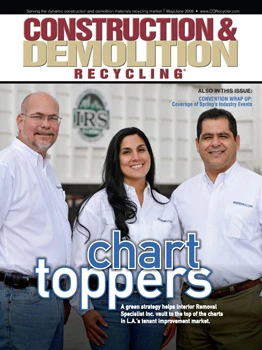
Explore the June 2008 Issue
Check out more from this issue and find your next story to read.
Latest from Construction & Demolition Recycling
- Sky Quarry seeks crowdfunding support
- Caterpillar releases the new Cat 980 GC Wheel Loader
- NAPA leaders participate in USDOT roundtable
- Yanmar CE launches full line of compact equipment
- Metso reports increased orders after flat H1
- Block Island Recycling Management Inc. aims to promote environmental stewardship
- SDI’s earnings rise quarter on quarter
- Complaints prompt relocation of concrete recycling plant