Fuel wood markets across the globe are expanding. According to the Boston-based forest products information and data firm, RISI, demand for biomass will likely triple in just the next three years, with Europe leading the way as a major consumer. Large-scale biomass power plants continue to go online around the world, but smaller-scale biomass applications also are growing in popularity. Whether large or small, central to these facilities is high-quality biomass fuel, and that starts with the wood chips.
Micro chips are typically the chips of choice for wood pellet production, as the smaller chip dries quicker and more evenly, allowing for more efficient pellet production with higher energy yields. Most chipper manufacturers offer machines or option packages to produce these specialty chips, but they typically fall short when it comes to performance and efficiency. And they aren’t always capable of producing larger-sized chips, should they be required for other fuel wood markets.
To get the best of all worlds for these ever expanding markets, a machine that can produce micro chips and switch back to standard chips can be a good option.
Runs in the family
Joedy Cahoon, owner of J & R Cahoon Logging in Bellhaven, North Carolina, is a third-generation North Carolina logger, having started in the woods with his dad at age 17. Thirty-seven years later, his operation is stronger than ever, due in part to a Model 3590 whole tree chipper from Bandit Industries, Remus, Michigan, with the micro chip drum that he uses to supply Enviva—one of the largest manufacturers of processed biomass fuel in North America. He was among the first loggers to sign a contract with Enviva to supply one of its North Carolina pellet mills, and with that contract secured he immediately began looking at chippers to supply the mill with the micro chips they needed.
A dryer use for biomass By Ryan Eidson Torrefaction began as an ancient artisanal technique used to enhance the physical and aesthetic features of wood. Today the modern torrefaction process reduces moisture content in biomass to nearly zero so that power plants can use the biomass for fuel and heat. Torrefaction also reduces transportation and aggregation costs. Torrefied biomass, also called biocoal, is a practical replacement for coal.
How does torrefaction turn wood biomass into biocoal? One technology used to torrefy biomass is a rotary kiln dryer system. This rotary dryer heats moist biomass in a low-oxygen environment (at between 200 to 300 degrees Celsius) to dry it down to a very low moisture content. According to Mark Beekes and Marcel Cremers of Renewable Energy World, Nashua, New Hampshire, “Torrefaction temperature must stay below 300 degrees C to keep a large part of the lignin intact, which serves as a natural binding agent for making pellets.”
The rotary kiln cannot rotate too fast or too slow. Carbonization instead of torrefaction will occur if the kiln rotates too slowly. The biomass will not fully torrefy if the kiln rotates too fast. If the temperature is too high, gasification will occur and biocoal will not be produced.
The resulting biocoal will not rot, has a very low risk of fire and repels water. Unlike coal, torrefied biomass (biocoal) will not emit sulfur dioxide or nitrous oxide. Biocoal can stay in open air; silos become unnecessary. Concerning energy density of these fuels, conventional wood pellets contain approximately 8-11 gigajoule (GJ) per cubic meter while torrefied wood pellets contain approximately 15-18.5 GJ per cubic meter. Wood chips have a caloric density of approximately 11 megajoule (MJ) per kilogram, and torrefied material has a density of approximately 20 MJ per kilogram. This means that torrefied wood retains 90 percent of its initial energy content yet shrinks in volume. This reduces transportation costs by 40-50 percent. One can use the torrefied biomass for fuel by itself or blend it with coal in an existing coal-fired power plant without modification.
Biocoal also meets government requirements for fuel in the EU (European Union) and the USA. Martin Henne, senior controller of the HMS-HOLZ Hagenow sawmill facility in Germany, says, “Wood is a good source to meet renewable energy targets,” but for efficient burning, he says, “You have to be aware of moisture, minerals and wood type.” Lower moisture content means a more efficient boiler.
Torrefaction is a good preprocessing step for wood and other biomass material for gasification, bio-oil for fuel, biocoal for wood- or coal-fired plants and general combustion. With an expected $11 billion global market value for biomass by 2020, torrefaction is the solution to economically transport biomass material to market and use it as the next renewable fuel.
Custom-designed and manufactured treatment and drying equipment can help turn biomass into biocoal. Worldwide Recycling Equipment Sales LLC, Moberly, Missouri, works with clients to create built-to-order torrefaction systems, Vulcan Systems, including setup, commissioning, training and maintenance support. The author is a writer for Worldwide Recycling Equipment Sales LLC and can be reached at reidson@wwrequip.com. |
“We were running another machine at the time; Bandit didn’t have a micro chipper out yet when we started,” Joedy explains. “I went and watched a friend with another machine run his, then I demoed some other micro chippers. My local Bandit dealer got in touch with me, told me Bandit had their micro chipper ready so they brought a Model 3590 out to our job site, and I just fell in love with it.”
Joedy’s Model 3590 is a 30-inch capacity whole tree chipper with an 800-horsepower Cat C27 engine. The micro chip drum is equipped with 16 knives, giving double the cuts per revolution compared with a normal chipper. Despite these extra cuts, Joedy says he still packs chip trailers in about 12 minutes and generally throws 20 loads on a set of knives.
When Joedy’s brother Ronnie Cahoon also secured a contract with Enviva, he turned to Bandit as well for a solution and purchased a Model 3590 of his own. Having formerly worked with Joedy at J & R Cahoon Logging, Ronnie branched out seven years ago to form his own company in the area—Cahoon Brothers Logging LLC. They still help each other out, and now that they each have a 3590 micro chipper, they’re both in a position to supply the South’s largest exporter of wood pellets.
“Joedy got his Model 3590 about six months before we did,” says Sharon Cahoon, Ronnie’s wife and office manager for Cahoon Brothers. “We were a bit more skeptical of it all; we wanted to sit back and watch, see how it was all coming out. There’s a big market right now for the chips, and when a couple new contracts opened up to supply Enviva, we knew it would probably be the last chance to get in so we jumped feet first.”
Ronnie also is a veteran of the woods, having worked just like Joedy from an early age. His current operation employs approximately 25 people, and jumping in with both feet on its Model 3590 has been a profitable leap.
While Joedy and Ronnie Cahoon send several truckloads of chips each day to Enviva, another family operation is finding success with Bandit’s Model 3590 a bit further south.
Branching out
Jimbo Nathe of R. J. Nathe & Sons, Dade City, Florida, referring to a tract the family team was working in the central part of the state, says, “The first phase was salvage on some pine where it had a beetle infestation. We cut the salvage area, took everything we could to a roundwood market and chipped the residual. And the rest of the operation is going to be chipping of unwanted hardwoods, trying to restore the area to more of an open pine stand, more like Florida used to be.”
Jimbo is one of the sons in the business. His father, Robert Nathe Sr., started the company with a cousin back in 1957. When his cousin retired, Robert decided he still had work to do, so he kept right at it, forming R.J. Nathe & Sons in 1994. At age 77, Robert Sr. still sweats in the Florida sun every day with the family.
“I stayed in business with my cousin for 37 years, and when he retired I bought him out and changed the name to R.J. Nathe & Sons,” recounts Robert.“We have five boys; they all work with me and the boss lady, my wife Patsy.”
Robert, Patsy and the boys took delivery of their Model 3590 in April 2013 to go after some fuel wood markets that were opening up in the area. Whereas Joedy and Ronnie Cahoon are serving a single customer with a specific chip, Nathe’s machine is flexing its versatility to handle multiple markets.
“Right now our main market is a cement plant, where we started out needing the small chip for their old coal boiler,” explains Jimbo. “The other market we’re dealing with is a local power plant. They don’t necessarily need as small a chip as what we’re producing, but the machine is versatile enough to where the chips still meet their specs. Being able to feed two markets is the reason we went with the 3590, and this machine is capable of going back to an eight-knife system to produce bigger chips for other markets.”
The Model 3590 has quickly become a welcome addition to the family operation. Jimbo says they haven’t had a single issue with the machine since they got it, and though much of their work involves sandy conditions, they still see anywhere from 20 to as many as 40 loads on a set of knives before sharpening.
“I’ve been getting some real surprising knife life out of it for a 16-knife system,” says Jimbo.
Bandit wasn’t the first on the scene with a big chipper dedicated to producing micro chips. But patience does have its virtues, and these three family operations all share the same optimism for the future with their Model 3590 whole tree chippers.
“I’m glad Bandit didn’t have the very first micro chipper to come out because I think they really put some thought into this design,” says Joedy Cahoon.
Biomass markets can range from large scale operations like the Enviva, to universities, municipalities, and smaller local users such as factories looking to convert old coal boilers to wood. And families like the Cahoons and the Nathes are equipped to meet a variety of wood chip needs.
“We were primarily a swamp logging crew for the majority of our existence,” said Jimbo Nathe. “We looked into chipping for several years and about a year ago we decided to make the move and get a chipper. As time went on we realized we needed a bigger chipper, and that’s when we decided to move up to the Bandit. It had everything we were looking for and it allows us to serve multiple markets. I don’t think it could be any better. “
The article was submitted by Bandit Industries, based in Remus, Michigan. More information is available at www.banditchippers.com.
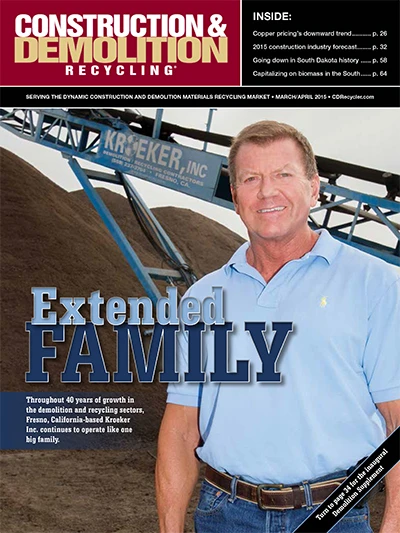
Explore the March 2015 Issue
Check out more from this issue and find your next story to read.
Latest from Construction & Demolition Recycling
- Cielo investor requests annual meeting
- CDE sets up washing plant on Long Island, NY
- NWRA: NIOSH cuts a step in the wrong direction
- Ferrous price hikes could be poised to pause
- Northstar secures 15-year lease extension for asphalt shingle recycling facility
- Greenwave asks for SEC filing extension
- Construction Plastics Initiative lines up projects
- ShearCore adds dealership group in Canada