After decades of abandonment and neglect, more than a dozen structures on the historic South Dakota Human Services Center campus are being demolished, recycled and repurposed.
The demolition of any historic property comes at a cost, both financially and sentimentally. As the oldest institution in South Dakota, the Human Services Center opened 10 years before South Dakota even gained statehood. This led to the campus’ 2009 listing as one of America’s 11 Most Endangered Historic Places. But after extensive consideration, the price tag of rehabilitating the properties turned out to be too measurable to ignore, and state officials felt they could no longer stand idly by as the neglected buildings slowly decayed.
The castles of South Dakota
Spearheaded by the pioneering Dr. Leonard Mead in 1891, the campus that housed the “Dakota Hospital for the Insane”—later changed to the South Dakota Human Services Center (HSC)—grew to include a wide variety of buildings, many of which emphasized neoclassical, art deco, Italianate, prairie and neorenaissance architectural styles. Mead became renowned for his forward-thinking philosophy that mental illness patients should be treated compassionately in a peaceful environment, unlike many of the institutional asylums of his day.
Mead’s understanding of mental illness far surpassed many of his contemporaries, noting that mental illness is “a misfortune which may come to any of us.” His attitude that patients deserve conditions that “he would wish for himself and his family” was continued by his successors, who erected ornate buildings full of architectural hallmarks on the scenic campus. Due to Mead’s concerns for fireproofing after a fire broke out at the original hospital in 1899 and killed 17 patients, the structures were built to last and constructed from stone and steel with 12- to 24-inch-thick walls, clay tile roofing and concrete.
Coined by preservationists as “the castles of South Dakota,” the campus buildings were not just sturdy but statuesque, featuring wide porches, fan and Palladian windows, pedimented porticos, balustrades, bracketed eaves, arches, pillars, coffered ceilings and terrazzo floors. Many of the buildings’ facades utilized local Sioux Quartzite, a unique reddish-pink quartzite only found near Sioux Falls, South Dakota.
But recent years have not been kind to the once-grand campus. In 1991, then-South Dakota Gov. George Mickelson conducted a study to determine whether the campus could be renovated for modern medical use. Upon the committee’s conclusion that it would be more cost-effective to build a new center, most of the buildings became permanently abandoned as newer buildings were constructed. When funds became tight, maintenance for the unused properties was sacrificed, and repairs were ignored.
Although current South Dakota Gov. Dennis Daugaard sought proposals for reuse of the buildings, none came to fruition. Daugaard deemed the dilapidated buildings a “liability to the state,” noting the time was long past for “us to be good stewards of this property.” While no one questioned the campus’ historic value, the estimated cost of the proposed restoration project, which ranged from $10 million to $50 million, hindered the economic viability of the campus.
Ultimately, a $1.87 million contract was awarded to Runge Enterprises to demolish 13 structures on the campus, with an additional $148,000 to demolish a smokestack for an old boiler plant and a root cellar.
Salvaging products
The demolition by Runge Enterprises began in early October 2013 with the Haas building completed in August 2014. Roads, sidewalks and lights will be reinstalled along with landscaping. Runge Enterprises is a Sioux Falls, South Dakota-based contractor that offers a variety of services for residential, business and industrial and governmental agencies, including grading and excavating, heavy highway construction, demolition and land development. The company also offers concrete recycling on the grade, and pioneered the use of blended crushed surfacing in the subgrade to provide a superior performing grade for new surfacing.
Runge Enterprises is supported by General Equipment & Supplies, an authorized dealer for Yankton, South Dakota-based KPI-JCI and Astec Mobile Screens (KPI-JCI/AMS). In order to recycle the concrete and other material on site, Runge Enterprises used the new KPI-JCI/AMS FT2650 jaw crusher with optional grizzly prescreen, which is designed to prevent plugging and blinding, and optional tramp iron relief system, which provides overload protection from uncrushable events. Both of these features prove beneficial in recycling applications, according to Gerry Liesinger, job superintendent for Runge Enterprises. The company currently owns a 2006 model of the FT2650, and the improvements in the new-generation model are “very, very good,” he says.
“This system is much more refined and user-friendly. It’s very elementary—anybody can run it,” Liesinger says.
Extra effort Most crushing and screening projects performed on a job site happen after buildings are torn down, but crews at a new large housing and community development project in Colorado have decided to crush and screen material as they prep the site for construction. The extra effort is saving Fiore & Sons and its customer money. Candelas is a 1,500-acre planned community in west Arvada, Colorado. The land, located at the intersection of Candelas & Coal Creek Canyon Road is the only planned community to share property lines with the former Rocky Flats Plant nuclear weapons production facility, a former Superfund site. By processing the rocky dirt at the site with crushing and screening equipment, Denver-based demolition and site preparation firm, Fiore & Sons, can salvage various sizes of rocks, which can then be used for landscaping and other products in the development. All this earthen material would have otherwise been hauled off site and potentially landfilled. Wyatt Ball, foreman on site for the screening and crushing operation for Fiore & Sons, says that to make usable products from the excavated material, the company is employing screens, impact crushers and a wash plant. Material is loaded into screens and from there it travels into the crusher, which sizes it to a 1-½-inch base. “After that process is completed, we move it down here to this wash plant and wash the rock off so it gets all the silt and any fines off of it, so it is a quality material,” says Ball. “[That way] it can be used for landscape or anywhere else where we need it.” Landscape material, road base and riprap bedding are all being produced from the rock on site. Ball estimates crews are processing 2,000 yards per day of material. In addition, Fiore & Sons has about 26 scrapers moving about 35,000 cubic yards of dirt material per day to prep the site for housing and community facilities. Learn more about the work being performed by Fiore & Sons in a video report at www.CDRecycler.com/fiore-candelas-screening-video.aspx. – Kristin Smith |
With the HSC job site being mere blocks away from KPI-JCI/AMS’ South Dakota manufacturing facility, Liesinger had the unique experience of working with the first prototype of the new-generation FT2650 and offering his feedback as the end user, which was then implemented into the final design. Bob Frohreich, project manager for track-mounted equipment for KPI-JCI/AMS, says while there are more features with the new FT2650, the goal was to streamline and simplify.
“We have made improvements to the customer interface to make things easier to operate and more reliable,” he says. “We have made structural improvements in the way of the main chassis as well. All of the conveyor belts on this machine are now endless, so you don’t see problems with belt splices. We have improved many components, and have made many of our purchased components common with other track-mounted plants at our three manufacturing locations. This makes it easier for our customers to get parts.”
It’s that type of customer service relationship KPI-JCI/AMS prides itself in, according to Frohreich.
“When we design equipment, we are designing the best equipment for our customers,” Frohreich says. “We have a lot of experience and can get close to what is needed, but it truly comes down to how well a piece of equipment works for the customer. Our customers are king when it comes to their feedback. When traveling to customer sites, we always come back with new ideas. Our engineering department works very closely with our service department, and this is another way that we get feedback from our customers. If we have an issue, we are very proactive in getting it resolved.”
A high-caliber customer service is crucial to Liesinger, who knows downtime is dead time. “Downtime is huge. When something goes down, I’m sitting dead in the water. If you can count on service to get the equipment running right away again, it makes all the difference in the world. It makes that piece of equipment so much more valuable,” he says.
The FT2650 also emphasizes mobility on the job site, enabling contractors to eliminate any unnecessary set-up time, according to Mike Runge, president of Runge Enterprises.
“We can walk the machine off the lowboy and begin crushing operations within minutes,” Runge said. “We can also maneuver around a job site or pit so we don’t have to have equipment pushing the raw material to the jaw.”
Liesinger has run approximately 23,000 tons of recycled concrete through the FT2650. With a wide assortment of sizes and types of material, processing the recycled concrete, steel contaminants and rebar can be tricky, Liesinger says. The material is sized to 1 ½-inch-minus and 3-inch to 1 ½-inch and sold primarily to local farmers.
“You’ve got small material and large material, sometimes fine and sometimes not,” he says. “There’s debris in it, rebar, wire and pipes—all kinds of stuff. Some of the concrete is mushy and soft because it’s from the 1920s, when they didn’t put a lot of cement in it and used dirty gravel. You’ve got all kinds of different variables, and it’s one reason I’m glad we’re using the FT2650. With it, you can set any size of material you want to make by pushing a button — it takes seconds to do and then you’re back up and running.”
Life beyond the landfill
While 13 buildings were deemed unsalvageable, four of the most historic structures were able to be saved and will be rehabilitated to last for many more years to come. Most notable of these is the Mead Building, a massive early-1900s building featuring a stunning Carrara marble staircase with coffered ceilings and high arched porches, which is currently being renovated by the Yankton County Historical Society to become a museum and cultural center.
And by recycling the material, Runge Enterprises is ensuring 20,000 tons of concrete has a life beyond the landfill.
“All of the salvaged product would have gotten buried and wasted,” he says. “The FT2650 allows us not to bury the waste, while at the same time making some money off of the material. It’s a win-win situation – good for the environment and good for the pocketbook.”
The author is media relations manager, KPI-JCI & Astec Mobile Screens, Yankton, South Dakota. More information is available at www.kpijci.com.
Get curated news on YOUR industry.
Enter your email to receive our newsletters.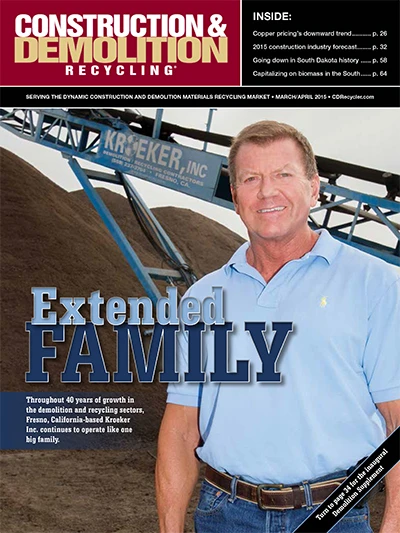
Explore the March 2015 Issue
Check out more from this issue and find your next story to read.
Latest from Construction & Demolition Recycling
- Cielo investor requests annual meeting
- CDE sets up washing plant on Long Island, NY
- NWRA: NIOSH cuts a step in the wrong direction
- Ferrous price hikes could be poised to pause
- Northstar secures 15-year lease extension for asphalt shingle recycling facility
- Greenwave asks for SEC filing extension
- Construction Plastics Initiative lines up projects
- ShearCore adds dealership group in Canada