// Legal issues
DOJ sentences employees of Tennessee salvage firm to prison
U.S. District Judge Ronnie Greer has sentenced five employees of A&E Salvage, Morristown, Tennessee, to prison terms ranging from six months to five years for conspiring to commit Clean Air Act offenses. The sentences are in connection with the illegal removal and disposal of asbestos-containing materials at the former Liberty Fibers Plant in Hamblen County, Tennessee.
In announcing the sentencing, the Department of Justice (DOJ) reports that A&E Salvage had purchased the plant out of bankruptcy in order to salvage metals that remained in the plant after it ceased operations.
U.S. District Judge Greer sentenced Mark Sawyer, a former manager of A&E Salvage, to the statutory maximum of five years in prison, to be followed by two years of supervised release. A&E Salvage Manager Newell Lynn Smith was sentenced to 37 months and two years of supervised release.
A&E Salvage Manager Eric Gruenberg received a 28-month sentence. Armida and Milto DiSanti each received sentences of six months in prison, to be followed by six months of home confinement.
The judge ordered all the defendants to pay restitution of more than $10.3 million, which will be returned to the U.S. Environmental Protection Agency’s (EPA’s) Superfund, which was used to clean up the plant site contamination.
In sentencing the men, Judge Greer heard expert testimony that noted the exposures of A&E Salvage’s workers to asbestos resulted in a substantial likelihood that workers would suffer death or serious bodily injury as a result of their exposure.
“These co-conspirators took unacceptable and illegal risks with workers’ lives and the community’s health,” says Assistant Attorney General John Cruden of the DOJ’s Environment and Natural Resources Division. “These significant sentences should send a message that illegal asbestos removal can have serious consequences, including a prison term for those responsible.”
According to court documents, all five defendants pleaded guilty to one criminal felony count for conspiring to violate the Clean Air Act’s “work practice standards,” which is salient to the proper stripping, bagging, removal and disposal of asbestos.
According to the charges, the conspirators engaged in a multiyear scheme in which substantial amounts of regulated asbestos-containing materials were removed from the Liberty Fibers plant without removing all asbestos prior to demolition.
The charges state the defendants allowed the stripping, bagging, removing and disposing of asbestos in illegal manners and without providing workers the with necessary protective equipment.
// Association activities
Asphalt pavement association names new chairman
The National Asphalt Pavement Association (NAPA), Lanham, Maryland, has named Michael Cote its 2015 chairman. The association announced Cote’s new position at NAPA’s 60th Annual Meeting, held Jan. 25-28 in Marco Island, Florida.
Cote is executive vice president and chief development officer for The Lane Construction Corp., based in Cheshire, Connecticut. The company specializes in heavy civil construction services and products for the transportation, infrastructure and energy industries. Lane Construction has nearly 60 asphalt plants and 12 quarries scattered throughout the eastern United States.
During the ceremony, Cote said, “It is an exciting time for the asphalt pavement industry. We face many challenges—from uncertainty in Washington about how to fund needed investment in our national infrastructure to a strong competitive threat from alternative paving materials—but I am certain we are well aligned to ensure drivers continue to enjoy smooth, safe, easy-to-maintain asphalt pavements for the foreseeable future.”
Cote has served on multiple NAPA committees and task forces that are focused on industry innovations and best practices, including the Warm-Mix Asphalt Task Force, which helped bring energy-saving warm-mix asphalt technology to the U.S., according to NAPA. Most recently, he served as a leader of an industry tour of Japan that sought to understand how Japanese road builders are making quality pavements from mixes that incorporate high levels of reclaimed asphalt pavement.
“Being the leader for the industry and putting innovation into practice is something NAPA has always done and will continue to do,” said Cote. “I am proud to be a part of that, as are all NAPA members.”
// Demolition projects
Collapsed Cincinnati bridge was undergoing demolition
A sizable section of a bridge made of concrete and steel collapsed onto an interstate highway in Cincinnati on Jan. 19. The bridge was undergoing demolition at the time of the collapse, according to the Cincinnati Enquirer, and one demolition worker was killed in the incident.
The collapsed bridge had formerly carried Hopple Street across Interstate 75 in northwest Cincinnati. When the section of bridge fell onto the highway at approximately 10:30 p.m., it fell just in front of a moving truck that would have been crushed if it had traveled just a few feet farther, according to reports from the scene. Interstate 75 in north Cincinnati was closed for a period of time following the incident.
According to the Enquirer report, a demolition crew assigned to take down the Hopple Street bridge was on site at the time of the collapse. The victim was a crew worker who reportedly was on that section of the bridge when it collapsed. The cause of the collapse is under investigation.
// Legislation & regulation
OSHA updates reporting requirements
The Occupational Safety and Health Administration (OSHA), Washington, has updated reporting requirements for employers. Beginning Jan. 1, 2015, covered employers are required to report all work-related fatalities within eight hours of an incident and all in-patient hospitalizations, amputations and losses of an eye within 24 hours of finding out about the incident.
Previously, employers were required to report all workplace fatalities and only when three or more workers were hospitalized in the same incident.
OSHA says the updated reporting requirements enable employers and workers to prevent future injuries by identifying and eliminating the most serious workplace hazards.
Employers have three options for reporting severe incidents to OSHA, including:
- call their nearest area office during normal business hours;
- call the 24-hour OSHA hotline at 1-800-321-OSHA (1-800-321-6742); or
- report online at www.osha.gov/report_online.
// Association activities
Carpet associations introduce voluntary product stewardship program
The Carpet and Rug Institute (CRI), which is focused on educating customers and the industry on carpet, and Carpet America Recovery Effort (CARE), an organization focused on advancing market-based solutions for postconsumer carpet, have introduced a voluntary product stewardship (VPS) program to assist sorters of postconsumer carpet diverted from landfills.
The two organizations, both based in Dalton, Georgia, say the VPS program is market-based and has been designed to accept and manage all applicable postconsumer carpet, regardless of polymer type or primary materials or construction.
The program’s goal is to provide financial assistance to qualified domestic sorters who divert postconsumer carpet from landfills, according to the groups.
“CRI is pleased to offer financial support for the VPS program,” says Dan Frierson, chairman of CRI. “Our members are participating voluntarily as part of our government relations activities and have committed $4.5 million for the program’s initial year. The VPS program will be a bridge for sorters as new technologies and applications are developed to increase market-driven demand for all postconsumer carpet.”
The VPS program launched in January 2015. Sorters who qualify for financial assistance are expected to begin receiving funds by the end of June 2015.
Sorters may qualify for funds by completing all required documents and submitting quarterly reports on their business results to CARE.
More information on the program is available at https://carpetrecovery.org/home/voluntary-product-stewardship-program.
// Green building
Reuse and recycling emphasized in Edmonton, Alberta, redevelopment project
One of the largest sustainable developments in the world is being developed at the former City Centre Airport in Edmonton, Alberta. Since its last flight, the city of Edmonton, Alberta, has begun construction at Blatchford with a focus on reducing the environmental impact during the first stage of development.
The recycling and reuse initiatives happening on site include:
- Buildings – The former airport hangars are being deconstructed instead of demolished. Through the deconstruction process, a building is slowly dismantled to allow the building materials to be sorted for recycling, reuse or waste management. This differs from standard demolition, where the building is taken down as fast as possible with the materials likely ending up in a landfill. A minimum of 85 percent of the waste created from the buildings in Blatchford will be diverted from the landfill.
- Runways – All runways will be removed and recycled on site. The materials (concrete, asphalt and gravel) will be used to construct the roads in the community. Any excess materials will be sold for reuse elsewhere.
- Stormwater Ponds – Rather than hauling the earth that is dug up to create the stormwater ponds off site, the soil will be used to build a large hill in the community.
In addition to the recycling and reuse initiatives happening during construction, the city is still investigating the feasibility of a district energy system to significantly reduce greenhouse gas emissions in the community. If feasible, the system could provide heating and cooling for all buildings in Blatchford using 100 percent renewable energy.
Blatchford will be home for up to 30,000 residents when the development is complete.
// Legislation & regulations
Maryland governor issues waste reduction goals
Maryland Gov. Martin O’Malley has issued an executive order affirming statewide waste reduction goals, directing state government to increase recycling, composting and waste diversion, and limiting new or expanded landfills to help drive innovation and achieve those goals.
“While we know that climate change is real, and Maryland is vulnerable, we also know that we can take steps to ensure the sustainability of our Maryland communities and our environment,” says O’Malley. “Today’s action is the right thing to do for our environment—and it creates opportunities for the jobs and business activity that we need to ensure the environmental and financial health of our communities.”
The executive order, effective immediately, states:
- Maryland shall endeavor to ensure that all waste generated in the state is increasingly reduced and reused rather than discarded in a manner that would adversely impact health and environment.
- Maryland shall have a goal of 85 percent waste diversion and 80 percent recycling by 2040. To ensure progress toward these statewide goals, state government shall have a mandatory recycling rate of 65 percent by 2020 and shall divert at least 60 percent of its organic waste through recycling, composting or anaerobic digestion by 2020.
- Maryland Department of the Environment (MDE) will create a source reduction checklist to track and encourage waste reduction. Additionally, in accordance with Maryland’s green purchasing guidelines, state government shall consider source reduction in procurement, including by avoiding unnecessary packaging and returning reusable packaging to vendors.
- Except for permit applications submitted to the MDE before Jan. 19, 2015, the department will not issue a permit for any new municipal or land-clearing debris landfill capacity in the state.
- MDE will provide local governments with information on alternatives to landfilling.
// Demolition projects
Boston bridge demolition begins
Work has started on a $20.6 million railroad bridge demolition project in Boston, according to a report in the Boston Globe.
Chicago-based Walsh Construction Co. has been selected as the contractor for the demolition of the Long Island Viaduct, which connects the island of that name in Boston Harbor to Moon Island and that then connects to the mainland.
The demolition project is expected to be completed by the end of April 2015, although the most visible aspects of the demolition were completed by February.
The two-lane steel bridge was constructed in 1951. It closed in October 2014 after bridge inspectors expressed concern about its condition. The city of Boston has issued a request for proposal for the design of a new bridge to take its place. While the 1951 structure was built at a cost of $2 million, the design selection process alone for the new bridge is expected to cost $9 million. The cost for the overall project is estimated at $80 million, according to the Boston mayor’s office.
The 225-acre Long Island in Boston Harbor was at one time home to a military fort. During the 20th and 21st centuries it has housed hospitals and social services facilities. Those enrolled in programs on the island have temporarily been relocated.
// Legislation & regulations
EPA, USDA highlight benefits of spent foundry sands
The U.S. Environmental Protection Agency (EPA), in conjunction with the U.S. Department of Agriculture (USDA) and the Ohio State University (OSU) have released a risk assessment concluding that silica-based spent foundry sands from iron, steel and aluminum foundries, when used in certain soil-related applications, are protective of human health and the environment and yield environmental benefits.
“There is potential for substantial growth in the recycling of silica-based spent foundry sands,” says Mathy Stanislaus, assistant administrator for EPA’s Office of Solid Waste and Emergency Response. “Our risk assessment concludes that the evaluated reuses are environmentally appropriate. Advancing the environmentally sound, beneficial use of industrial materials, such as spent foundry sands, provides substantial opportunities for addressing climate change and air quality, enhancing state, tribal and local partnerships, reducing costs, and working toward a sustainable future.”
Based on the assessment, the EPA and the USDA are coming out in support of the beneficial use of silica-based spent foundry sands in manufactured soils, soilless potting media and as a foundation layer in road construction. The EPA’s risk assessment of the evaluated uses concluded that they are environmentally appropriate because the constituent concentrations in the sands are below the agency’s health and environmental benchmarks.
The EPA says it estimates the environmental benefits from using silica-based spent foundry sands in the specific applications studied, at the current use rate, results in the following savings in one year:
- the energy savings equivalent to the annual electricity consumption of 800 homes;
- carbon dioxide emissions reductions equivalent to removing 840 cars from the road; and
- water savings of 7.8 million gallons.
More information on the risk assessment is available at www.epa.gov/epawaste/conserve/imr/foundry/index.htm.
// Company news
Dem-Con obtains recycling rate certification from Recycling Certification Institute
Dem-Con Cos., Shakopee, Minnesota, has received Certification of Real Rates (CORR) from the Recycling Certification Institute (RCI), Sacramento, California.
CORR is designed to ensure Dem-Con customers that its recycling rates have been verified by a certified third party and are real, verifiable and reasonable. RCI develops protocols specifying eligibility criteria and detailing steps to monitor and verify recovery and recycling rates achieved by specific recycling facilities.
Dem-Con is now eligible to offer the new Leadership in Energy and Environmental Design (LEED) pilot credit point available to LEED 2009 and LEED v4 projects for using a verified construction and demolition (C&D) recycling facility.
“Being able to offer the additional point means a lot to our customers and adds value to any USGBC (U.S. Green Building Council) project,” states Jason Haus, CEO of Dem-Con. “Satisfying the certification requirements with RCI allows our customers to rely on our facility’s recycling rates. Transparency and reliability means a lot in our industry, and the third-party certification with RCI helps us achieve that.”
Dem-Con says it is the only facility in the Twin Cities marketplace and one of four facilities in the United States to be certified and able to offer the additional LEED point. Dem-Con operates a residential single-stream material recovery facility (MRF), a C&D MRF, a shingle processing yard, a wood processing facility and a landfill.
Additional information about RCI and CORR is available at www.recyclingcertification.org.
Stat Snapshot:
Employment in the waste and recycling industry increased by 8,700 during 2014, bringing total sector employment to a new high of 383,300. [Source: U.S. Bureau of Labor Statistics]
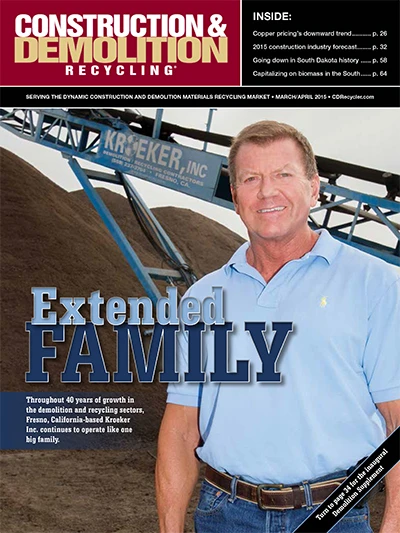
Explore the March 2015 Issue
Check out more from this issue and find your next story to read.
Latest from Construction & Demolition Recycling
- Crush costs and lift output with Komatsu crushers
- Komatsu excavators made for demolition and recovery
- New Komatsu wheel loaders
- Trump copper tariff includes potential scrap export restrictions
- CDE publishes sustainability report
- AED opposes 'right to repair' language in federal bill
- UP reaches agreement to acquire Norfolk Southern
- Eco Material Technologies opens cement alternatives plant