When Denver Public Schools (DPS) began renovations on a 14-story office building it was converting into a vertical campus in downtown Denver, everyone involved had sustainability on their minds.
With the adoption of its 2012 Sustainability Management Plan (SMP), DPS made a commitment to practice an “ethic of sustainability” in all of its operations to reduce the impact the district’s 185 schools have on the environment.
A major focus of the plan calls for measurable improvements in landfill diversion rates and reduced greenhouse gas (GHG) emissions from solid waste throughout the 87,398 student urban school system.
Renovating the former office building to accommodate its new use as an educational facility required the interior of the 415,000-square-foot building to be completely demolished and rebuilt.
Upon completion of the $31.4 million renovation, the building—featuring 13 floors with an additional mezzanine level and two levels of underground parking—will serve as a shared campus for a new elementary school, a high school, a technical college and several of the district’s administrative offices.
Meeting goals
Early in the design process, DPS met frequently with the design build team made up of Denver-based firms SlaterPaull Architects and PCL Construction to establish sustainability goals for the project.
“Sustainability is very important to us,” says Adele Willson, a principal of SlaterPaull. “So it’s important to have that conversation early on about how to incorporate sustainable strategies into the project.”
Recycling and repurposing construction materials that came out of the building during demolition was high on the list. “We knew there was going to be a huge amount of construction waste coming out of that building and we wanted to keep a lot of it out of the landfill,” says Katheryn Zeeb, DPS construction project manager.
By the time interior demolition of the building began in March 2013, DPS had found homes for much of the material collected from the 52-year-old building.
Tons of tiles
Ceiling tiles that had been torn out of the building during renovation made up a large part of the construction debris. Kevin Welch, PCL Construction senior project manager, recommended that DPS recycle the ceiling tiles through the Armstrong Ceiling Recycling Program. The program enables commercial building owners and contractors to ship discarded ceiling tiles from demolition and renovation projects to the nearest Armstrong plant as an alternative to landfill disposal. The discarded tiles are then used to manufacture new ceilings in a closed-loop process.
“When we’re doing a demolition project, we’re always looking to recycle, repurpose or reuse as much material as we can, so we were really glad this program is in place,” says Welch.
Welch says the process for recycling the used ceiling tiles was simple. After removing the old tiles from each floor, subcontractor Black Bear Demolition stacked the tiles on pallets, shrink-wrapped and labeled them, and transported the material via elevator to the ground floor. Once on the ground, the tiles were stored until there were enough pallets to fill a semi-trailer truck.
“Once we had a full truckload, Armstrong would come and pick up the materials and transport them back to one of their ceiling plants free of charge,” says Welch. “A lot of companies are willing to come and haul the materials away for a price. It was refreshing to see that the Armstrong program was a free option.”
Through its participation in the Ceiling Recycling Program, DPS recycled 131,571 square feet of used ceiling tiles, diverting approximately 67 tons of construction debris—the equivalent of about 6,579 tires—away from landfills.
By recycling the old ceilings, the school district was able to avoid the carbon dioxide equivalent of nearly 30,000 kilograms of GHG—similar to not driving about 244,722 miles in a car—and move closer to its long-term sustainability goal of zero-waste schools.
Ceiling recycling can help building owners and contractors save money on container costs and landfill fees and also can contribute to LEED (Leadership in Energy and Environmental Design) credits for construction waste management.
“This recycling program has proven to be advantageous from so many different levels, from savings on container costs and landfill fees to stewardship of resources for future generations,” says DPS Construction Services Director James Allen. “It’s been a good experience. Now that we’ve done it once, we’ll continue to do it. We’re a school district and we are life-long learners.”
Planning projects
The Armstrong Ceiling Recycling Program requires the contractor to develop a construction waste management plan that makes provisions for ceiling recycling in the project specifications.
“This is something we put in place for every project,” says Welch. “We never just throw things away. Even though this project doesn’t have a LEED requirement, we typically follow green building processes and recycle as much material as possible.”
The construction waste management plan for DPS’ project included specifications for recycling the used ceiling tiles and salvaging many of the other materials that came out of the building.
During demolition, individual dumpsters were designated for metal, wood, ceiling grid, carpet tiles and any other potentially reusable or recyclable materials. As these materials were removed from the building, the demolition crew separated them from the rest of the construction debris and placed them in the appropriate dumpster.
The project team quickly found homes for the 115,000 square feet of carpet tile that was removed from the building. The school district donated 65,000 square feet of used carpet tile to Habitat for Humanity of Metro Denver. The remaining 50,000 square feet was reused as flooring in the offices of another school district building.
Wood cabinets, window coverings, sinks, faucets and other plumbing fixtures also were donated to Habitat for Humanity. “Habitat came out to the job site with their trucks and hauled away the materials they were interested in, including 30,000 square feet of metal window blinds,” says Welch.
In addition, DPS recycled 240,000 lineal feet of ceiling grid and 35,000 cubic feet of steel through a local metal recycler. The group donated 20,000 square feet of raised computer access flooring to a local public library where it now serves a purpose in the computer room.
Welch estimates 28 percent of the materials removed from the building during demolition were either recycled, repurposed, reused or donated, diverting approximately 139 tons of construction debris from landfills.
“This helps the school district meet its sustainability goals for waste reduction, and it just makes sense environmentally,” says Welch. “We’re just being good stewards of the environment.”
The article was submitted on behalf of Armstrong World Industries Inc., Lancaster, Pennsylvania. Armstrong designs and manufactures ceilings and floors. In 2013, Armstrong consolidated net sales from continuing operations totaled approximately $2.7 billion. Armstrong operates 35 plants in eight countries and has approximately 8,700 employees worldwide. More information is available at www.armstrong.com.
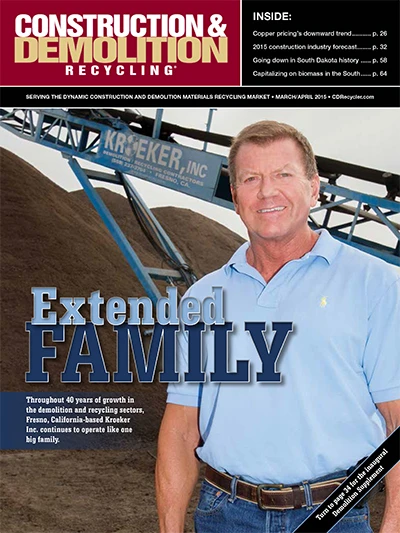
Explore the March 2015 Issue
Check out more from this issue and find your next story to read.
Latest from Construction & Demolition Recycling
- Cielo investor requests annual meeting
- CDE sets up washing plant on Long Island, NY
- NWRA: NIOSH cuts a step in the wrong direction
- Ferrous price hikes could be poised to pause
- Northstar secures 15-year lease extension for asphalt shingle recycling facility
- Greenwave asks for SEC filing extension
- Construction Plastics Initiative lines up projects
- ShearCore adds dealership group in Canada