The United Kingdom-based National Federation of Demolition Contractors (NFDC), together with Demolition Publications and with sponsorship assistance from equipment maker Sandvik, has issued a document titled “Guidance on the Safe Use of Mobile Crushers in the Demolition Environment.”
Following are excerpts drawn from the 16-page document, which can be viewed in its entirety at http://issuu.com/thedabbler/docs/revised_crusher_guidance or accessed through the NFDC website, which is www.demolition-nfdc.com.
Critical Prevention
Track and wheel-mounted mobile crushers are now commonplace on demolition and recycling projects up and down the country. As the demolition industry embraces the need to process and recycle materials that were previously regarded as waste into a potentially valuable commodity, so the popularity of the highly versatile and productive mobile crusher has spread.
Accidents involving these highly specialized items of equipment are thankfully rare, and the NFDC has yet to record a single fatality deemed to have been caused directly by such an item of equipment.
However, crushing equipment has been involved in a number of fatalities in other industry sectors, and as the use of these machines becomes ever-more widespread in the demolition business, the NFDC has initiated a drive to improve practices related to the application and use of mobile crushers.
This guide has, therefore, been produced in recognition of the need to improve the approach to the provision of these machines and to their use on site.
The Lay of the Land
Mobile crushers are normally fed from loading shovels, backhoe excavators or from other processing machinery (a conveyor, for example).
In its simplest form, it will be a stand-alone machine fed directly with the material to be crushed and discharging to a stockpile.
If the material to be crushed is reinforced concrete, a magnetic separator will often be positioned over the discharge conveyor to remove the metal and prevent it from contaminating the production run material.
If the mobile crusher is to be fed directly by a loading shovel or excavator, then:
- Excavator standing pads should be suitable (stable) and should be high enough for the operator to be able to monitor the feed hopper from the cab. Safe access to the excavator must be provided for the operator.
- Where wheeled loading shovels are used, then the ramp should be wide enough to allow for adequate edge protection (minimum 1.5 meters or 4.9 feet high) on either side of the ramp as well as for the travel of the machine.
- The maximum gradient of the ramp should be within the capacity of the loader (a maximum gradient of 1:10 is recommended).
- The last few meters of the ramp should be level so that the machine is not discharging uphill, thus enabling operators to more easily monitor the feed. The loading shovel will also be more stable.
- Ensure pedestrians and obstructions are excluded from the bucket operating are.
If the crusher is to be fed directly by a conveyor:
- All dangerous parts of the machinery should be suitably guarded.
- Failure to replace guards (on crushers and conveyors) after cleaning or maintenance work is a major cause of injury on these machines.
Around the Blocks
Causes of crusher blockages can be grouped under two main headings.
These include stalling, which can be caused by:
- Electrical or mechanical failure
- Material jammed in the chamber, causing an overload
- Overfeeding of material
- Entry of tramp metal or wood
- Excessive clay or other fines in the crushing cavity, preventing small material from passing through the crusher.
The other cause is bridging, which is, attributed to:
- Oversized feed material
- A foreign body in the crusher feed or discharge chamber obstructing the feed materials.
Working on the premise that prevention is better than the cure, every effort should be made to prevent oversized material or tramp metal from entering into the crusher feed hopper.
This can be accomplished by:
- Reducing oversize material by hydraulic breaker, pulverizer, drop ball or other means
- Training and instructing the loader driver not to load oversized material
- Following the manufacturer’s recommendations on the rate, presentation of feed and crusher settings
- Instituting a program of good housekeeping to prevent scrap steel from entering shovel buckets
- Ensuring the size of buckets is appropriate to the capacity of the crusher
- Regular inspection of metal parts (e.g. bucket teeth and dumper wear plates, etc.) to ensure they are unlikely to break off and enter the crusher feed
- The strategic placing of electrical magnets and/or the installation of metal detectors to prevent tramp metal from entering the crusher
- Using level indicators for feed control
- Maintenance of drive systems.
A properly designed mobile crushing operation should not need any person to be present on the crusher access platform during normal crushing operations. Being on the access platform during normal operation presents the following risks:
- Being struck by objects ejected from the crusher. This includes pieces of stone or metal as examples.
- Being pulled into the crushing chamber when attempting to pull out contaminants (e.g. reinforcing bar)
- Being struck by the loader bucket if the access platform is within the working radius of the loading machine (for 360-degree excavators)
- Exposure to dust, especially in the case of crushing concrete or bricks or any other high silica-content material. Breathing silica dust can cause serious respiratory diseases.
- Whole body vibration; anyone on the platform could be subjected to constant low-frequency vibration.
It may be necessary for a person equipped with the appropriate personal protection equipment (PPE, which includes ear plugs, dust mask, eye protection, hard hat, protective footwear and a high-visibility outer garment) to spend a few minutes setting the speed initially if there is no remote facility.
The feed should be controlled from the machine feeding the crusher by varying the loading rate into the feed hopper.
Taking Action
When a crusher becomes blocked, steps should be taken to minimize risks. These include:
- Have a nominated person to supervise the activity and call for assistance as necessary
- Stop the feed at the earliest opportunity and isolate the plant to ensure all processes are stopped
- Remove excess material by mechanical means where possible before the cause of the blockage can be dealt with; in some cases, however, an amount of removal by hand will be involved, and when this occurs the crusher and associated plant must be stopped and isolated
- Manual removal should only be carried out by suitably trained and competent people
Hazards encountered may include:
- Poor or difficult access
- Accidental start-up of feeder, crusher or adjacent plant
- Being struck by material from the feeder, chute or projected material
- The movement of any material present inside the crusher
- Slipping and falling
- Manual handling of rocks and equipment
- Unexpected movement of crusher components. In the case of an impact crusher, ensure that the rotor has stopped and is secured before opening the crusher chamber
- Damaged electrical cable
- Noise
- Stored energy from electrical, hydraulic, compressed air, mechanical sources and gravity
- Unsafe placement of material removed from the crusher.
The preferred method of clearing a bridged crusher is by the use of a breaker boom fitted with a hydraulic breaker. An alternative could be a hydraulic excavator fitted with a quick hitch with a pick and/or breaker, where the boom is operated remotely, by radio control, the use of closed-circuit television (CCTV) may be employed to assist the operator.
Depending on the result of your risk assessment, clearing a bridging blockage with a hydraulic breaker boom or similar implement can be carried out with or without the crusher still operating—but the former is not recommended because of the risk of equipment damage.
When a hydraulic breaker boom or excavator is not available, then other methods such as cranes with slings and hooks may be employed.
If it is necessary for a person to enter the crusher to position hooks or slings, the crusher, feed and main conveyor must be stopped, isolated and locked off (per manufacturer instructions and safe working practice). A safety harness also should be worn.
The NFDC Working Group that produced this document consisted of John Netheny and Alan Matchett of Sandvik Mining and Construction and Mark Anthony of Demolition Publications. Anthony can be reached at manthony@markanthonypublicity.co.uk.
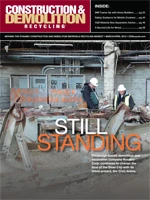
Explore the March 2012 Issue
Check out more from this issue and find your next story to read.
Latest from Construction & Demolition Recycling
- US Senate backs reduced cuts to EPA
- US EPA offers brownfields-related funding
- Sky Quarry seeks crowdfunding support
- Caterpillar releases the new Cat 980 GC Wheel Loader
- NAPA leaders participate in USDOT roundtable
- Yanmar CE launches full line of compact equipment
- Metso reports increased orders after flat H1
- Block Island Recycling Management Inc. aims to promote environmental stewardship