When Cleveland area demolition firm Baumann Enterprises opened a mixed C&D materials recycling plant last year, the company’s president, Bill Baumann knew the importance of separating materials by size.
Baumann’s Recycling Center, located on a 25-acre site near Cleveland, uses finger screen and trommel screen technology supplied by Ireland-based Powerscreen and by Terex dealer Agg-corp, Westerville, Ohio.
Once material flows through the screens, employees are stationed at various sorting stations where the material falls. Hand sorters pick out recyclable metals and remove unwelcome contaminants from the clean wood fraction of the stream.
The mixed C&D debris starts its journey through the processing system by being loaded into the three-tiered finger screener. The larger material that does not fall through the screen is conveyed to a sorting line for hand separation. The smaller material falls onto a secondary belt where material also ends up on a hand picking line. The fines are the remaining material.
“Whatever is left that falls through the bottom comes down through a fine screener. Essentially, it is dirt, and it goes off to another stockpile for screening at a later date,” Sean Nowack, plant supervisor, Baumann’s Recycling Center, explains.
Through its process, Baumann’s is able to produce a variety of end products, including wood for mulch and fuel, crushed concrete and red brick, screened soils and fill materials, recyclable cardboard and mixed plastics.
“We are running about 1,200 to 1,300 yards of mixed material per day through the plant with various products [created including] wood, brick, steel, nonferrous et cetera,” says Sean Nowack, plant supervisor, Baumann’s Recycling Center.
Sink or Swim Wet separation is one method used to sort C&D debris. Krause Manufacturing, Bellingham, Wash., manufactures custom-built automated sorting systems for C&D recycling facilities. The company’s Rocket Wet Separator is designed to automatically separate the large quantities of rock and wood typically found in C&D debris. With the Rocket Wet Separator, materials are introduced into a horizontal drum, which is partially filled with water and rotated by a hydraulic drive system. The rotating cylinder sends the high-density material onto a paddle system, which moves it above the waterline and expels it out of the drum. High velocity jets positioned within the drum, and facing the infeed end, shoot water creating a river that washes the wood and other floating debris back out the in-feed end of the drum. A water reclamation system collects and stores the water for reuse, limiting the need for disposal and decreasing costs. More information is available at www.krausemanufacturing.com. |
Three-Stream Separation
The three-stream separation process used at Baumann’s is typical of many mixed C&D recycling facilities. Sparta Innovations, Notre Dame, New Brunswick, Canada, often installs finger screens at C&D recycling facilities. The company describes them as heavy-duty two-deck vibrating boxes that separates material into three sizes: fines (0 to 2 inches); medium (2 to 8 inches); and overs (8-plus inches).
Etienne Lagacé, territory manager for Sparta, says separating materials into “overs” and “unders” fractions means less material going to a landfill, which translates into cost savings and the possibility of more revenue.
Unders of 0 to 2-inch minus products “are very dense and they often can be used as alternative daily cover,” Lagacé says.
Another benefit of sorting out the smaller fraction, according to Lagacé, is it creates an easier picking stream as workers will have less debris to sort.
“There is also a possibility of a medium line (2 to 8 inches), which eliminates once again a good part of the stream onto the overs line for better recycling,” Lagacé adds.
In addition to finger screens and disc screens, which often are used for primary screening at mixed C&D facilities, Lagacé says trommels also can be used as a primary screen. He says, though, that a trommel is “more likely to get beaten by the product and [can be] less durable.”
Star screens and trommel screens are mostly used as a secondary screen and are more effective in that role, according to Lagacé.
Lagacé says even though a facility may use automated sorting equipment, hand sorting plays an important role in the process. “C&D waste being what it is, very uneven flows requires the sorters to target different products and sort them from the stream,” he says.
Sparta usually positions magnets on the fines product line and on the medium product line. “With a nice presort and a good, clean line, we can also see a magnet approximately three-quarters [of the way] down the picking station itself,” adds Lagacé.
End Market Considerations
Size classification can vary from region to region. What end markets the C&D recycling facility can sell its material to will drive how that facility separates its stream and how many end products it ultimately creates.
Dick Reeves of recycling systems company General Kinematics, Crystal Lake, Ill., told attendees of the 2011 C&D Recycling Forum, held in Ellicott City, Md., that in recent years processors of C&D material have tried to either find other markets to enter or to optimize the material they have.
“We have to be a little more flexible with the markets and the commodities that are out there,” said Reeves during the forum’s State of The Industry session. Reeves has seen an increased interest by C&D recyclers in renewable energy from waste. There are more plastics, paper and organics in the waste streams for companies to extract, he says. “With energy prices high, that is definitely a viable option,” Reeves said.
Recovery rates are increasing with capacity down, Reeves told the audience. He explained that processors have more time on their hands to pull additional commodities out to increase recovery rates.
“You have to be creative in this job environment,” said Reeves. “As a custom equipment manufacturer, we are not limited to what has been done in the past, but we like to work with the end user to explore those ideas of what we can provide in the future.”
The author is associate editor of Construction & Demolition Recycling and can be reached at ksmith@gie.net.
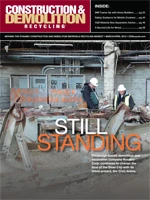
Explore the March 2012 Issue
Check out more from this issue and find your next story to read.
Latest from Construction & Demolition Recycling
- US Senate backs reduced cuts to EPA
- US EPA offers brownfields-related funding
- Sky Quarry seeks crowdfunding support
- Caterpillar releases the new Cat 980 GC Wheel Loader
- NAPA leaders participate in USDOT roundtable
- Yanmar CE launches full line of compact equipment
- Metso reports increased orders after flat H1
- Block Island Recycling Management Inc. aims to promote environmental stewardship