// Company News
WM to Open C&D Recycling Facility in Toronto
Waste Management (WM), Houston, has plans to establish what it calls a technologically advanced facility in Toronto dedicated to processing scrap materials from building construction and demolition (C&D) sites.
The facility, scheduled to be in operation by the third quarter of 2012, was acquired by WM in late 2011. The company says the facility will undergo extensive upgrades, which are expected to exceed $16 million. The semi-automated single-stream recycling plant is expected to process an estimated 87,000 metric tons of C&D material in its first full year in operation.
Brad Muter, WM vice president for Eastern Canada, says the site was selected, “because continued strong construction activity and population growth are anticipated in Toronto.”
// Green Building
Starbucks Builds Drive-Through Store with Shipping Containers
Starbucks has opened a drive-through store in Tukwila, Wash., which was built out of four used shipping containers. The 448-square-foot location will be applying for Leadership in Engineering and Environmental Design (LEED) certification from the U.S. Green Building Council (USGBC).
According to Starbucks’ corporate website, www.starbucks.com, it has helped lead the work with other retailers and the USGBC to create a system to certify retail stores and store prototypes. This volume-certification process allows pre-certification of green stores at the design, construction and operational strategy level. Starbucks will then be held accountable through spot checks and continued review to ensure it is meeting the standards it has set.
“This is a huge opportunity for the USGBC and for retailers. Traditionally, LEED certification has been accomplished one building at a time, making it difficult for retailers with hundreds of stores to participate,” according to the website.
Starbucks says it will use shipping containers for short- or long-term cafes on properties awaiting development and in areas where there is a high volume of automobile traffic.
// Conferences & Events C&D Recycling Forum Heads to the West Coast
After two successful shows in the Baltimore area, organizers Recycling Today Media Group, publishers of Construction & Demolition Recycling magazine, say changing locations can give C&D recyclers and demolition contractors an opportunity to learn more about efforts being done nationally in C&D recycling.
“California has made great strides in its efforts to promote the recycling of C&D materials, so it only makes sense to host a show in an area that really embraces diversion and recycling of these sometimes challenging materials,” says James R. Keefe, publisher, Recycling Today Media Group. “The organizers of the C&D Recycling Forum are committed to bringing to the forefront the issues that are facing the industry on a national basis and to helping provide solutions through unmatched programming and networking opportunities.”
Sessions will cover a wide range of topics, including case studies, and are designed to provide information essential for building successful C&D recycling businesses. “For those companies that handle these materials, there really is no other conference that provides the level of industry-specific programming that you will find at the C&D Recycling Forum,” adds Keefe.
|
// Green Building
USGBC’s LEED Program to Open for Public Comment
The third public comment period for the proposed 2012 update to the U.S. Green Building Council’s (USGBC), Leadership in Engineering and Environmental Design (LEED) green building program opened March 1, 2012. The comment period, which will close March 20, marks the start of the LEED 2012 program delivery process.
“LEED sits at the core of the green building movement, and is critical in realizing our collective mission,” says Scot Horst, senior vice president of LEED, USGBC. “LEED’s strength comes from its continuous evolution. This continuous improvement is the outcome of thousands of technical volunteers working to develop the program and the adaptability of the program to technological and market changes.”
The third draft of LEED has been refined to address technical stringency and rigor, measurement and performance tools, and an enhanced user experience, says the USGBC. The technical changes have been informed by market data, stakeholder-generated ideas, expert engagement and advances in technology, according to USGBC. The council adds, additional performance-based management features will help projects measure and manage energy and water usage, site and building material selection, and indoor environmental quality.
“LEED 2012 is the next step towards a global, performance-based application,” Horst says. “In LEED 2012, a project’s engagement with LEED will represent an ongoing commitment that is supported by a suite of performance management tools.”
LEED 2012 extends itself as a long-term engagement tool for organizations and projects, enabling a focus on continuous improvement. Programs aimed at helping organizations use LEED to benchmark building performance in preparation for certification and for tracking performance of their building’s post-certification provide opportunities for ongoing engagement between project teams and USGBC both before certification and after the plaque is awarded.
For LEED projects outside the U.S., LEED 2012 will offer a new global perspective. Through modified language, new requirements and options that increase flexibility, LEED 2012 is designed to make it easier for the international community to engage.
In an effort to redefine and enhance the user experience, the USGBC says LEED credit requirements have been rewritten to better align with documentation already required by the architecture and construction fields. Improvements to submittals, documentation paths and LEED Online are designed to improve LEED usability.
As the LEED program evolves to address the needs of the building industry, the development process is based on principles of transparency, openness, and inclusiveness, and includes multiple comment periods where input received is incorporated into the program. The third public comment documents, including technical refinements, scorecards and responses to comments from the previous public comment period, are available at usgbc.org/LEED2012. Members of the public can comment on any substantive changes made since the second public comment period, which ran from Aug. 1 through Sept. 14, 2011.
LEED 2012 will be balloted in June and launch in November. To vote in the ballot, USGBC members must opt-in to the Consensus Body beginning April 2, 2012. The Consensus Body is made up of employees of USGBC national member organizations in good standing.
// Demolition Update
MagneGas Retained for Large Dismantling Project
MagneGas Corp., based in Tarpon Springs, Fla., has been retained by King Metal Recycling & Processing, Miami, in partnership with Marathon Construction and Demolition, Fort Lauderdale, Fla., to supply the cutting fuel needed for the dismantling of a 13.3 million gallon oil tank in Port Canaveral, Fla.
MagneGas develops technology to convert liquid waste into a hydrogen-based metal working fuel and natural gas alternative.
The fuel for the project will be delivered from MagneGas’ headquarters in Tarpon Springs.
The company estimates that more than 1,000 cylinders of MagneGas will be required to complete the demolition project.
King Metal and Marathon Construction and Demolition also have agreed to use MagneGas’ product later in the year for another large joint venture project the companies are working together on in Alabama.
“After seeing a demonstration of MagneGas, we recognized immediately that this environmentally friendly alternative fuel is the ideal choice for this assignment,” says Pete Amador, president of King Metal.
Amador continues, “By using the MagneGas fuel on this project, we will be able to complete the demolition of the oil tank much faster, more efficiently and at a lower cost when compared to other metal cutting fuels.
“As we continue to successfully execute on our growth strategy, new customers are beginning to see the advantages and effectiveness of using MagneGas,” says Scott Wainwright, president of MagneGas.
“We are excited to be partnering with King Metal Recycling & Processing and Marathon Construction and Demolition on such an endeavor and look forward to a fruitful ongoing business relationship,” Wainwright adds.
// Company News
C&D Recycling Facility Opens in Wisconsin
Landfill Reduction & Recycling Center, a construction and demolition (C&D) recycling facility based in Appleton, Wis., officially opened for business Feb. 14, 2012, at a site that was formerly a paper recycling facility owned by StoraEnso.
Landfill Reduction & Recycling has been licensed by the Wisconsin Department of Natural Resources as a C&D recycling facility.
The plant is located on more than 5 acres in an industrial park. The facility features a 30,000-square-foot total enclosed area, including a 7,800-square-foot tipping building with two 30-foot tall overhead doors, a 7,000 square-foot drywall recycling area, a 14-person sorting station and 44,000-pound sorting screen.
Landfill Reduction & Recycling’s capabilities include sorting, aggregating, and resizing of a variety of C&D materials including wood, drywall, shingles, aggregates, metal, cardboard, carpet, carpet pad, mattresses, plastics and landscape material. The company accepts presorted and mixed C&D debris.
// Company News
Cherry Opens Stabilized Material Plant in Houston
Cherry, a recycling and demolition firm headquartered in Houston, has opened its fifth stabilized material plant in the greater Houston area. The plant produces stabilized sand and base material for companies located primarily in counties near Houston.
The new stabilized (pug mill) plant will be capable of producing 500 tons per hour.
“With the new pug mill plant and our existing Crawford Rd. plant, we have doubled our monthly production capacity to approximately 160,000 tons per month for the northwest region,” says John Conyer, general manager of Cherry’s Stabilized Materials Division.
“With the combination of all of our pug mill operations, Cherry is the largest, privately owned stabilized materials company is Texas,” Conyer says.
// Waste to Energy C&DR Publisher Launches New Magazine The publishing company says the new periodical, Renewable Energy from Waste, will address how “waste and residues of consumers and industry are [increasingly] viewed as resources.” Harnessing the energy value of these streams continues to make sense both economically and environmentally, according to the Recycling Today Media Group. Four issues of Renewable Energy from Waste will be produced in 2012, says the Recycling Today Media Group, as well as a monthly e-newsletter. Subscription information to the complimentary magazine is available at www.RecyclingToday.com/subscribe-REW.aspx. |
// Regulatory Issues
Connecticut Agency Grants Tentative Approval to C&D Facility
The Connecticut Department of Energy and Environmental Protection (DEEP) has made a preliminary decision to approve a permit application for Milford, Conn.-based Recycling Inc. to construct and operate a solid waste processing, transfer and recycling facility in Milford.
DEEP’s Notice of Tentative Determination, the first step in the decision making process on permit applications, would allow for an expansion of current recycling operations at this site.
The proposed permit will allow Recycling Inc. to eventually receive up to 700 tons per day of solid waste from commercial and industrial activities, construction and demolition activities, clean wood and various types of recyclables. The primary activities under the proposed permit are for receipt and processing of certain solid wastes to reclaim and recycle various materials, and to consolidate for transfer off-site by truck, rail and barge.
The proposed permit requires the construction and operation to be done in phases.
At the completion of each phase, the facility must supply to DEEP a statement certified by a professional engineer that all activities were completed in accordance with the conditions outlined in the permit.
Recycling Inc. must also submit a health and safety plan approved by the Milford Fire Department to DEEP.
The permit requires Recycling Inc. to control odors, water discharges and noises resulting from the construction and operation of the facility in accordance with applicable state and federal regulations.
According to DEEP, Recycling Inc. must maintain a certified operator at all times during operation, post a financial assurance mechanism to ensure proper closure of the facility at the conclusion of operations, and to submit to DEEP quarterly compliance audits performed by a Professional Engineer.
Additionally, the facility must construct a chain link fence and create a 600-foot “green buffer zone” around the entire facility.
// Association Activities
New Advocacy Group for Recycled Aggregate Launches in Canada
Eliminating large piles of concrete and asphalt removed from demolition sites and road reconstruction projects by re-using these materials is the immediate focus of a new Ontario organization. At a forum held Dec. 15, 2011, involving municipal engineers, aggregate users/producers and environmental groups, Aggregate Recycling Ontario (ARO) launched its campaign to encourage the use of more recycled aggregate in infrastructure projects.
“There is an immediate crisis in the GTA (Greater Toronto Area) surrounding recycled aggregate,” Adrian Van Niekerk, ARO chair, says. “Recycling yards are filling up to capacity with broken concrete and asphalt, yet not nearly enough is leaving the site to be used again in new construction. Some facilities have had to close their yards to new deliveries, because there is just no more room.”
ARO estimates nearly 3 million metric tons of recyclable concrete, asphalt and aggregate recovered from GTA construction sites are currently sitting in piles to be processed. Although ARO was formed to bring attention and find a solution to the growing aggregate piles, it says its mandate goes well beyond that issue. Organized by the Ontario Stone, Sand & Gravel Association, and the Toronto and Area Road Builders Association, ARO brings together 17 companies, and seven associations that produce and use recycled aggregates.
Members are interested in expanding opportunities for recycling aggregates by permitting more recycling facilities and through research and trial projects. More information is available at www.aggregaterecyclingontario.ca.
// Forecasts & Statistics
Construction Materials Prices Rise Moderately in January
The cost of construction materials is showing signs of accelerating after moderating in January, according to an analysis of producer price index figures and recent market information released by the Associated General Contractors of America (AGC), Washington, D.C. Ongoing price increases underscore the urgency of funding public construction projects promptly, association officials say.
“Cost increases have slowed in recent months but haven’t disappeared,” says Ken Simonson, AGC chief economist. “In fact, today’s producer price index report may be the low point, as manufacturers and commodities markets are signaling that bigger increases may be just around the bend.”
Simonson noted that the price index for construction inputs — a weighted average of all materials used in construction plus items consumed by contractors, such as diesel fuel and tires on equipment — rose 0.4 percent from December to January and 4.5 percent over the past 12 months. Those increases were slightly higher than the rise in the overall producer price index for finished goods and the smallest year-over-year change for construction materials since 2010, the AGC says.
“Unfortunately, this slowdown has already ended for some key materials,” Simonson warns. “Crude oil and diesel prices have moved up significantly since the January price index data were collected. Producers of plastic pipe have notified customers of 8 percent increases, effective March 1. And copper futures have jumped from levels of a few weeks ago, making increases in pipe and wiring prices likely.”
AGC officials say the acceleration in materials costs adds to the urgency of getting a long-term federal highway and transit funding bill enacted, saying Congress and federal officials should make transportation a #1 priority.
“Each month that Congress puts off providing long-term funding for needed infrastructure projects costs taxpayers double,” says Stephen E. Sandherr, AGC chief executive officer. “They pay now in congested and deteriorated roads, and they’ll pay more when materials are finally purchased. Congress should get a bill to the President without further short-term extensions, and he should sign it.”
// Association Activities
AEM Select Aggregates Statistics Committee Head
The Association of Equipment Manufacturers (AEM) has selected Yankton, S.D.-based KPI-JCI and Astec Mobile Screens marketing manager, Lisa Carson, to serve as the head of the association’s Aggregates Statistics Committee for 2012.
The Aggregates Statistics Committee, which consists of 13 reporting brands, works to provide the most accurate and timely industry data available for market share calculation, forecasting and resource planning. As chairwoman of the committee, Carson is responsible for leading each meeting, webinar and teleconference, as well as providing agendas and minutes.
Debbie Carson, statistics manager for AEM, says Lisa Carson’s experience and enthusiasm made her the prime candidate for the position. “Lisa’s confidence and knowledge in the aggregates industry makes her the perfect choice to lead the committee,” Debbie Carson says. “I am grateful to be working with such a cheerleader of our industry.”
Lisa Carson, who has led KPI-JCI and Astec Mobile Screens marketing department for the past four years, says she is eager to take on additional responsibilities in the industry and work together with other manufacturers to provide important industry data. KPI-JCI and Astec Mobile Screens is a manufactures equipment for the aggregate, construction, paving and recycling industries.
“The Association of Equipment Manufacturers does a fantastic job of uniting manufacturers and creating a strong voice for its members and the industries it represents,” she says.
“I hope to contribute strong organizational skills and knowledge of the industry to create a successful committee that provides valuable content to other manufacturers,” adds Carson.
// Legislative Issues
EPA Issues Permit for Stormwater Discharges from Construction Sites
The U.S. Environmental Protection Agency (EPA) has issued a new permit, in accordance with the Clean Water Act, which will provide streamlined permitting to thousands of construction operators, while protecting the nation’s waterways from discharges of polluted stormwater from construction sites.
The permit will be effective in areas where EPA is the permitting authority: Idaho, Massachusetts, New Hampshire, New Mexico, Washington, D.C., and most U.S. territories and in Indian country lands.
According to the EPA, stormwater discharges from construction sites can contain harmful pollutants that contaminate waters, increase drinking water treatment costs and damage aquatic ecosystems. The new permit was shaped by input from the public and stakeholders to ensure that it provides important protections for waterways, while also providing flexibility to operators.
The 2012 construction general permit (CGP) is required under the Clean Water Act and replaces the existing 2008 CGP, which expired on February 15, 2012. The new permit includes a number of enhanced protections for surface waters, including provisions to protect impaired and sensitive waters. Under the Clean Water Act, national pollutant discharge elimination system (NPDES) permits are typically issued for a five-year period, after which time EPA generally issues revised permits based on updated information and requirements, as is the case with today’s announcement.
NPDES permits control water pollution by including limits on the amount of pollutants that can be discharged into waterways by specific sources. The permit is designed to provide new flexibilities for operators.
The 2012 CGP updates include steps intended to limit erosion, minimize pollution sources, provide natural buffers or their equivalent around surface waters, and further restrict discharges to areas impaired by previous pollution discharge.
// Forecasts & Statistics
US Construction Employment Increases
Construction employment increased in 148 out of 337 metropolitan areas between December 2010 and December 2011, decreased in 128 metropolitan areas and stayed level in 61 metropolitan areas, according to an analysis of federal employment data released by the Associated General Contractors of America (AGC), Washington, D.C.
The construction employment increases were likely fueled by a 4.3 percent increase in total construction spending between December 2010 and December 2011, driven largely by growing private sector demand, association officials note.
Lake County-Kenosha County, Ill.-Wis., added both the most and the highest percentage of new construction jobs (33 percent, 3,900 jobs). Other areas adding a large number of jobs included Edison-New Brunswick, N.J. (3,700 jobs, 11 percent); Portland-Vancouver-Hillsboro, Ore.-Wash. (3,600 jobs, 8 percent); Louisville-Jefferson County, Ky.-Ind. (3,100 jobs, 13 percent) and San Jose-Sunnyvale-Santa Clara, Calif. (3,100 jobs, 10 percent), according to the AGC.
The largest job losses were in Philadelphia, Pa. (-4,800 jobs, -7 percent), followed by New York City (-4,600 jobs, -4 percent); Dallas-Plano-Irving, Texas (-4,500 jobs, -4 percent) and St. Louis, Mo.-Ill. (-4,300 jobs, -7 percent). The Logan, Utah-Idaho area (-23 percent, -700 jobs) lost the highest percentage. Other areas experiencing large percentage declines in construction employment included Wilmington, N.C. (-20 percent, -1,800 jobs); Montgomery, Ala. (-17 percent, -1,100 jobs) and Bridgeport-Stamford-Norwalk, Conn. (-14 percent, -1,500 jobs), The association reports.
“Many communities are benefitting from growing demand from the private sector for new construction activity,” Ken Simonson, AGC chief economist, says.
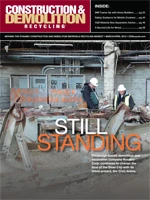
Explore the March 2012 Issue
Check out more from this issue and find your next story to read.
Latest from Construction & Demolition Recycling
- Deadline extended: ‘C&DR’ seeks industry participation for 2025 Largest C&D Recyclers List
- Algoma Steel seeks government funding
- US Senate backs reduced cuts to EPA
- US EPA offers brownfields-related funding
- Sky Quarry seeks crowdfunding support
- Caterpillar releases the new Cat 980 GC Wheel Loader
- NAPA leaders participate in USDOT roundtable
- Yanmar CE launches full line of compact equipment