Company Wrench Awarded Patent
Company Wrench, Carroll, Ohio, and its owner Brad Hutchinson have received a patent for the CP100 Magnet Combo heavy equipment attachment invented by Hutchinson.
The attachment is described as a versatile product that can both pulverize concrete and collect the metal using just one attachment.
“We finally have a product where one operator can sit safely in the seat of the machine,” Hutchinson says. “They can pulverize the concrete and mag the rebar. They don’t need to leave the safety of the excavator cab and [can] stay out of harm’s way.”
The CP100/Mag Combo consists of a 65,000-pound excavator with an attachment to pulverize concrete at the end of a long arm. The bucket also contains a magnet, which the operator runs over a pile of crushed concrete to pull out the metal rebar within.
Hutchinson and the Company Wrench engineering department spent about 18 months devising and refining the CP100 and received the patent from the United States Patent and Trademark Office on Dec. 27, 2011.
The patent is valid for 20 years and prevents anyone else from marketing or building the same type of equipment.
The Komatsu PC270 excavator with the patented combo unit is available for sale or rent from Company Wrench.
Dust Control Technology Goes to Work in Illinois
A Midwest demolition company has employed high-performance dust suppression technology from Dust Control Technology, Peoria, Ill., in the remediation of the former Northwestern Steel & Wire riverfront facility in Sterling, Ill. The control measures are intended to prevent dust from becoming airborne and migrating from the site.
IronHustler Excavating (IHX) and ELM Consulting, both based in Peoria, Ill., teamed up to develop a demolition and environmental remediation plan for the 20 acre site of Plant 1, which is being implemented in three phases. Phase 1 includes demolition and recycling of materials from the six buildings on the site, with IronHustler bringing down the buildings using excavators with grapple, shears and pulverizer attachments. ELM Consulting coordinated the project with IHX, providing soil boring, materials testing, inspections and monitoring to prevent the release of asbestos from rubble piles and deteriorating buildings. IronHustler uses the data to determine and verify contamination and ensure proper material handling.
The demolition and recycling process has the potential to generate large amounts of fugitive dust, so IronHustler is using a DustBoss DB-60 from DCT to blanket the area to mitigate complaints and possible health hazards with. Sterling city officials have noted the lack of nuisance dust from the site, and visiting EPA representatives have been impressed by the results, according to DCT.
IronHustler president Dave Schielein says he began investigating alternative methods of dust suppression on demolition and recycling projects due to frustrations with a common dust management technique: manually spraying the area with a hose. “It was an expensive approach, having workers spend an entire shift spraying the site,” he says.
Schielein also mentions issues with the manual approach. “The powerful spray would actually dislodge dust from the ground and send it airborne, and the sheer volume of water quickly soaked the debris, turning it into a muddy mess. If we had to haul any material to a landfill after completing a job, we were actually paying extra for the water weight.”
Schielein compared equipment from several manufacturers, ultimately specifying the DB-60 over other candidates.
One of the things that he says impressed him was the technical acumen of the manufacturer. “Most people don’t realize that dust suppression is a technical issue,” Schielein says. “We liked the fact that DCT concentrates only on dust suppression, and they’re not concerned with selling a wide range of equipment. Dust management is all they do.”
Schielein says the results were immediately apparent. “The effectiveness was the first thing we noticed. The DB-60 covered a huge area with a very fine mist. Even the large oscillating models from competitors couldn’t match the coverage area,” he says.
IronHustler estimates that the company saves a net six hours of labor per day during demolition and recycling, allowing employees to concentrate on core activities and avoid potential worksite hazards. “The DustBoss started paying back from the first day we used it,” Schielein says. “It’s easy to operate and can run unattended all day.”
The Northwestern Steel and Wire plant, once owned by the Dillon family of Sterling, was founded in the late 1800s and grew to employ almost 5,000 workers at the height of its success in the 1970s. The plant closed operations in 2001. The city of Sterling has begun the planning process for the land’s redevelopment, a project aided in part by a $1 million interest-free loan to pay for the mitigation of asbestos at the site.
McLanahan Acquires Universal Engineering
McLanahan Corp., a heavy-duty equipment designer and manufacturer based in Hollidaysburg, Pa., has acquired Universal Engineering Corp., Cedar Rapids, Iowa. Universal Engineering manufactures equipment for the aggregate and mining industries.
McLanahan says the acquisition brings hard rock crushing and apron, pan and wobbler feeders to the company’s product offering.
“It is our hope to grow the sales of Universal equipment around the world,” says George Sidney, McLanahan president and COO. “We are excited to have Universal’s high quality, respected machines in our line-up, but we are more excited to have a professional, highly-trained group of people join our team.”
In a press release, the company states, “As we enter into this new acquisition, McLanahan is committed to providing new products to customers and we look forward to expanding into new markets. As always, McLanahan will continue to provide cutting-edge innovation, engineering expertise and the highest quality pieces of equipment.”
Gibson Machinery Opens Western Pennsylvania Location
Gibson Machinery, based in the Cleveland suburb of Oakwood Village, Ohio, has opened a second location in Oakdale, Pa., near Pittsburgh. The 8,500-square-foot building situated on two acres offers equipment, parts and service.
“We just think there is a lot of potential in that area,” Owner and President Lee Gibson says. “That branch will end up surpassing what we do in Ohio.”
Mike Keremes is the vice president of sales in Oakdale. Bob Decker is parts and service manager.
Gibson Machinery represents Sennebogen, Doosan, Doppstadt and Genesis equipment. It recently began selling Chicago Pneumatic hammers and Terex’ compact line.
Exodus Machines Forms Alliance with Caterpillar
Exodus Machines Inc., a Superior, Wis.-based manufacturer of material handlers, and Caterpillar, headquartered in Peoria, Ill., have announced an alliance. Exodus’ purpose-built material handlers will now be available through the Cat dealer network in North America. The companies plan to sell the machines globally in the future.
According to Jody Howard, general manager of Cat’s Industrial & Waste Group, a recently formed strategic business unit within Cat, adding Exodus machines to Cat’s product line will allow Cat to give a new level of attention to industrial and waste customers. “It is an exciting opportunity for us here at Caterpillar to get focused on these waste and industrial customers, who for some time hadn’t really focused our attention,” she said during a teleconference announcing the alliance.
Bill Springer, a vice president with Caterpillar and leader of its Diversified Products Division, which the Industrial & Waste Group falls under, discussed why partnering with Exodus was such a good fit for both companies.
“It was pretty obvious they had a product; we had a product gap,” Springer says. “Exodus didn’t have a distribution system; we have a distribution system. So there were some pretty logical reasons why we began to talk. We started talking and realizing we could create a separate business unit around this.”
Bruce Bacon, Exodus Machines president, says the material handlers his company produces have been so widely embraced by the scrap industry that allying with Cat will be beneficial for customers.
“When Exodus made a decision to design and manufacture innovative, world-class industrial swing machines just a few short years ago, our mission was to incorporate safety and performance, efficiency, ease of maintenance and durability into our designs,” Bacon says. “At the same time, we really wanted to have a continuation of the relationship in the scrap industry that had been built over the years.
The market response has been gratifying and the product performance has resulted in accelerated market acceptance; and that brings us to today.”
Bacon continues, “From our perspective, the strength of Caterpillar’s leadership position and distribution, manufacturing and commitment to customer support combined with Exodus’ ability to create innovative, advanced designs really results in an alliance that delivers a superior value proposition to our current and future customers.”
During the first year of the alliance, the Exodus brand will remain. The product will be transitioned to the Cat brand within the next 12 to 18 months, Howard said. While the machines will be available in North America initially, Howard says, “As we move forward through the Cat brand, they will become available to more Cat dealers worldwide.”
In addition, there are plans to introduce more Exodus models within the next year. “We are aggressively developing and designing additional models to fill a variety of sizes and configurations for the market,” Bacon said.
Exodus’ machines will complement Cat’s current line of wheeled and tracked material handlers greater than 25 metric tons.
A news release issued by Cat indicates the company acquired a minority equity interest in a new entity, Exodus Machines LLC, formed by Exodus.
Get curated news on YOUR industry.
Enter your email to receive our newsletters.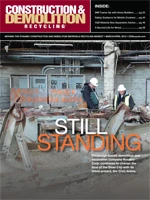
Explore the March 2012 Issue
Check out more from this issue and find your next story to read.
Latest from Construction & Demolition Recycling
- US Senate backs reduced cuts to EPA
- US EPA offers brownfields-related funding
- Sky Quarry seeks crowdfunding support
- Caterpillar releases the new Cat 980 GC Wheel Loader
- NAPA leaders participate in USDOT roundtable
- Yanmar CE launches full line of compact equipment
- Metso reports increased orders after flat H1
- Block Island Recycling Management Inc. aims to promote environmental stewardship