Long before a demolition crew ever arrives at a job site, a demolition contractor has to determine what equipment will be needed to get the job done right.
When that work involves a bridge crossing a body of water, a road or a valley, contractors must pay very close attention to detail. Making the wrong choice in equipment could hurt productivity, the ability to stay on schdule and even jeopardize safety.
Any time a job involves concrete, stone or asphalt that needs to be broken, a demolition contractor must make sure the breaker or hammer that is used will be able to meet the demands of the material and that it is connected to a machine that can support it. Bridge demolition jobs need proper planning to ensure, too, that it will be able to support the wieght of the equipment.
Site engineers determine what loads a bridge can support at different stages of the bridge demolition job, according to Ryan Murphy, marketing director for Indeco North America, Milford, Conn. “From this information, carrier machines and breakers can be specified for top-down deck removal or another method as required by the structural properties of the bridge itself,” he says. Environmental factors also must be considered such as the waterway and the disposal regulations in that area, he adds.
When deciding on what breaker or hammer to use, Murphy advises, “First and foremost, the decision should be based on the material to be broken and its properties.” He adds that a breaker “must be able to penetrate and fracture the material in the shortest amount of time possible, without being so large and heavy so as to jeopardize the integrity of the structure before it is time to do so.”
Gary Hannum, vice president of sales and marketing for Maverick Hammers, Summerville, S.C., says clients working on bridge demolitions will often request the breaker be equipped for underwater demolition. This is necessary for bridges crossing bodies of water, he says.
A New Design Allied Construction Products LLC (ACP), Cleveland, has announced the addition of the all-new Sandvik Small Range breakers BR555, BR777 and BR999 to its product line. What makes these breakers different from other breakers on the market is that they are designed without tie rods and incorporate Sandvik’s “Constant Blow Energy (CBE) plus operating system,” says ACP. The integrated one-piece tool bushing design includes the thrust ring, upper bushing, lower bushing and dust seal, thus requiring fewer parts, says ACP. The one-piece bushing can be replaced in the field, according to the company. The box-type housing of the “power-of-three” breakers incorporates what ACP describes as high-tech dampening material that reduces noise and vibration in addition to fully-protecting the power cell. The breakers are designed for less wear and better bending force-resistance for an increased life span and reduced operating costs. ACP says installation of the Small Range breakers is designed to be easier by the use of the swivel-type hose connecting block which the company says can be turned over to meet left or right hand hose connections. Sandvik’s Small Range breakers are designed for breaking application for carriers between 7,500 pounds and 27,600 pounds. Features of the Model BR555, BR777 and BR999 include:
More information is available at www.AlliedCP.com. |
Carrying the Weight
Breaker selection also is based on the weight and hydraulic properties of the excavator that will carry it. The carrier machine should be capable of lifting, positioning, maneuvering and stabilizing the breaker at all positions, Murphy says. In addition, the machine’s auxiliary hydraulics should provide adequate oil flow and pressure as recommended by the breaker manufacturer.
Ron Johnson, owner and president of RJ Hammers & Heavy Parts, Largo, Fla., says that for maximum results and safety when choosing a hydraulic hammer, it is important to select the correct size for the specific carrier on which it will be mounted.
“A good rule of thumb is to choose a hammer that does not exceed 10 percent of the carrier weight,” Johnson advises. This excludes long reach excavators, however, as those excavators must downsize the hammer an additional two classes or more, he says.
Hannum says proper hydraulic flow to the hammer that attaches to the machine is essential. “If you choose a hammer that is not the correct size for the carrier, the hammer simply will not work,” he says.
If the bridge is located in a downtown or residential area, dust and noise control also will be considerations for choosing equipment.
Wear Factors
Once the equipment is selected for the job, attention must still be given to equipment while it is being used, as wear will occur. Murphy says it is important for the operator to keep a suitable supply of grease on the moving parts of the breaker, “especially the tool in the lower bushing area to prevent premature fatiguing of components due to extreme heating.”
Johnson agrees, saying a common operator error is neglecting to lubricate the hammer. “Proper timely lubrication, according to manufacturer directions, will eliminate many potential costly repairs,” he says.
Making sure the hammer is used at the proper striking angle is also imperative, adds Johnson. “The hammer should be striking perpendicular to the material it is breaking. This striking angle will prevent unnecessary wear and tear on the tool holder bushings and will help ensure maximum results,” he says.
Hannum says the upper and lower bushings can deteriorate from impact. “The bushings are a critical part in the hammer tool. Without them, the hammer tool will not work properly,” he says. Checking regularly to make sure the hammer tool and bushings are properly greased will aid in maintaining an adequate lifespan for the bushings, he adds.
Proper Maintenance
Alignment is another key factor in maintaining performance. “Proper alignment between the piston and the working steel is paramount to efficiency with any breaker,” Murphy explains. “This is achieved through rotation of and regular replacement of wear items like the upper and lower tool bushings.”
Murphy even suggests giving consideration to the ease of maintenance on wear parts when selecting equipment in the first place.
A word of caution from Murphy on bridge jobs is that bridge deck demolition can leave breakers particularly susceptible to blank firing “by with the hammer is fired without any material to provide resistance.” He explains, “In this case, the lower internal components internal components to the breaker absorb the force of the downward stroke, instead of the material to be broken.”
Indeco and other manufacturers offer hammers that prevent blank firing, Murphy adds.
The size and scope of the project will determine the size of the equipment required, according to Keith Becker, product development specialist, construction tools for Commerce City, Colo.-based Atlas Copco.
“Another key factor is answering the question ‘How fast does it need to be removed?’” Contractors may only have a specified amount of time to complete demolition. If the job takes longer, then the contractor may face steep fines. Avoiding downtime, Becker says, is the biggest concern in completing the job on time.
In addition, having to abide by strict time limits can result in increased wear and tear to the breaker’s working tool and lower bushing. “If not cared for properly during use, the contractor will be down a machine and a breaker,” warns Becker. “Operators must keep a close eye on the job requirements as they can change when, for example, working on a bridge deck versus a concrete footing. ”
Staying Efficient
Murphy recommends having the hammers always breaking and using an alternate machine such as a skid steer loader to pick up debris and load trucks. If that is not a feasible options, an alternative would be using a quick coupler on the carrier machine to allow for quick transition to and from the breaker, he says.
Equipment setup and configuration will vary from job to job depending on space constraints. If a site is confined, Becker says, a bridge job will most likely have a working area where debris is piled up to be hauled away and crushed offsite. But some jobs will have the space and time to allow crushing onsite.
Choosing the right breaker or hammer for the excavator and job as well as performing regular maintenance will help keep the bridge demolition job and material moving along.
The author is associate editor of Construction & Demolition Recycling and can be reached at ksmith@gie.net.
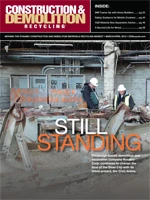
Explore the March 2012 Issue
Check out more from this issue and find your next story to read.
Latest from Construction & Demolition Recycling
- US Senate backs reduced cuts to EPA
- US EPA offers brownfields-related funding
- Sky Quarry seeks crowdfunding support
- Caterpillar releases the new Cat 980 GC Wheel Loader
- NAPA leaders participate in USDOT roundtable
- Yanmar CE launches full line of compact equipment
- Metso reports increased orders after flat H1
- Block Island Recycling Management Inc. aims to promote environmental stewardship