Texas recycled aggregates producer Trey Brown of Big City Crushed Concrete, Dallas, has a concern about the 2011 spring and summer season, but that concern is not necessarily a lack of demand for his company’s products.
Instead, says Brown, the lack of inbound material to be crushed recently has caused him to work though his stockpiles and creates the potential of Big City (http://werockdallas.com) having to scramble to fill larger orders.
If demolition and highway-tear-up work does not pick up in north Texas, Brown can foresee being unable to provide as much base course or other secondary aggregates that will be requested by road builders adding lane miles to the LBJ Freeway in the Dallas area.
That type of dilemma is one of several that may confront recycled aggregates makers as they face another spring and summer construction season predicted to offer subpar overall activity levels.
CONSIDERING CONCRETE-ASPHALT EQUILIBRIUM |
Owners of paving companies as well as crushing plants have an interest in the cost factors that can cause either concrete or asphalt to be the material of choice in a paving project. The Portland Cement Association (PCA, www.cement.org) has an interest in those cost factors since its member companies make a product used in concrete but not asphalt. For that reason PCA chief economist Ed Sullivan examines the key price points and tries to help the association determine how various raw material cost scenarios affect the concrete vs. asphalt demand equation. While presenting an economic forecast at the 2011 ConExpo-Con/Agg event, Sullivan pointed to the rising cost of oil as the key factor affecting asphalt pricing and demand. Sullivan’s models tend to show that at oil prices of around $75 or $78 per barrel and higher, “concrete can win bids over asphalt,” especially if such bids consider product life cycle. With oil having largely stayed above that threshold since mid-2009, this has likely benefited makers of concrete in 2010 and 2011. However, Sullivan pointed out, in states where budgets are under intense pressure, jobs may be bid in such a way that the lowest initial cost wins out, thus reducing what the PCA sees as concrete’s life cycle advantages. That last circumstance is bad news for companies that specialize in concrete rather than asphalt. In a map of the contiguous United States (“lower 48”) that Sullivan showed to attendees, only three of the 48 states (Montana, North Dakota and Arkansas) had no fiscal year 2011 budget short fall. A total of 18 of the 48 states were heading toward budget deficits of 20 percent or higher. That roster was geographically dispersed to include: six western states (Arizona, California, Colorado, Nevada, Oregon and Washington); four Southeastern states (Florida, Georgia, North Carolina and South Carolina); three Midwestern states (Illinois, Minnesota, Wisconsin); and five Northeastern states (Connecticut, Maine, New Hampshire, New Jersey and Vermont). |
DEFERRED HOPE, LITTLE CHANGE
At ConExpo-Con/Agg 2011, held in March in Las Vegas, economist Ed Sullivan offered an economic and construction industry forecast through 2015.
Sullivan, chief economist of the Portland Cement Association (PCA), Skokie, Ill., compared the economy in the wake of the financial system’s near collapse in 2008 as a wound that is slowly healing, “but the wound is very deep.”
As bad as the resulting economic turmoil has been, Sullivan said the steps taken to address the lending industry’s missteps have helped prevent further economic erosion. “We really on the verge of what could have been a depression,” said Sullivan.
The deepness of the wound, though, means recovery has been slow, and it will remain slow for another year or more, he predicted. Growth in the construction sector said Sullivan, “will not be substantial this year . . . it will take more time.”
Examining the construction industry’s three major sectors, Sullivan pointed to these growth barriers:
• Residential: a surplus of residential units (many of them foreclosed), tight lending standards causing potential home-buyers to save for down payments and repair their credit records, and high unemployment cutting into the pool of potential home buyers
• Non-residential: “Still huge amounts of vacancies” is how Sullivan portrayed this sector, pointing to an office vacancy rate that means some 500,000 new office jobs will have to be created before demand in that segment is created
In the first two cases, developers see little ROI (return on investment) incentive to start new projects, he noted, saying of the non-residential sector, “Conditions for positive ROI are years off.”
A lack of construction activity is likely to lead to a lack of demolition activity, causing depleted supplies of crushable, recyclable concrete harvested from demolished structures.
In the public sector, spending tied to the 2009 American Reinvestment and Recovery Act (ARRA) peaked in 2010, will be down modestly this year and is largely depleted for 2012, according to a bar chart that was part of Sullivan’s presentation.
Also contributing to this sector’s woes in 2012, according to Sullivan’s forecast, will be widespread state deficits as well as the delay in the creation of a federal transportation spending bill. Sullivan, citing the PCA’s sources in Washington, said he is not expecting a highway bill to pass until 2013, but once a bill is passed it will contain a 20 percent or more boost in annual spending.
SOLID EXPECTATIONS
Sullivan’s lack of faith in the construction industry’s ability to spring back to life before 2013 is reflected in his predictions of annual portland cement consumption.
The use of portland cement, a basic ingredient in concrete, mortar and stucco, shrank from 2007 to 2009 in the United States, with consumption declining most rapidly in 2009, by 26.9 percent.
In 2010, cement consumption was essentially flat (0.7 percent growth), and Sullivan sees consumption rising only 1.3 percent in 2011 and 3.7 percent in 2012. That scenario suggests that operators of concrete crushing plants can expect road building and commercial construction activity in 2011 and 2012 in many regions to match the past three years.
The good news, in Sullivan’s forecast, kicks in 2013, when a federal transportation spending bill has been authorized, many states will be past their most dire years of red ink, and pent up demand for new commercial and residential construction is also likely. “For every year we are depressed, we are building pent-up demand,” Sullivan stated.
For 2013, Sullivan and the PCA predict a 16.6 percent rise in portland cement consumption. For 2014, the forecast is for 18 percent growth on top of that, and by 2015 cement consumption could reach the 2007 figure.
Pent-up demand is also a factor in the infrastructure sector, where angry constituents are likely to welcome some highway resurfacing and widening projects that languished during the lean state budget years.
REGIONAL VARIATIONS
Even in a climate of subdued activity, there are some major construction, demolition and road building projects that can generate local supply and demand for crusher operators.
In its monthly roundups of construction activity, McGraw-Hill Construction (http://dodge.construction.com), Bedford, Mass., points out the largest projects that have broken ground in the past 30 days. In the first quarter of 2011, some of those major projects have included:
• $1.5 billion to add lanes to the LBJ Freeway in Dallas
• the $500 million Abengoa cellulose ethanol plant in Hugoton, Kan.
• a $450 million air terminal project at Love Field in Dallas
• the $360 million Cleveland Medical Mart and Convention Center (see the story starting on page 22 of this issue)
• a $300 million project at the Ford Motor assembly plant in Louisville, Ky.
• the $295 million Marriott Marquis job in Washington, D.C.
• hospital projects in California, one in San Leandro ($575 million) and the other in Oakland ($244 million).
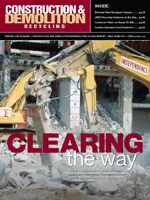
Explore the May 2011 Issue
Check out more from this issue and find your next story to read.
Latest from Construction & Demolition Recycling
- Cielo investor requests annual meeting
- CDE sets up washing plant on Long Island, NY
- NWRA: NIOSH cuts a step in the wrong direction
- Ferrous price hikes could be poised to pause
- Northstar secures 15-year lease extension for asphalt shingle recycling facility
- Greenwave asks for SEC filing extension
- Construction Plastics Initiative lines up projects
- ShearCore adds dealership group in Canada