Nothing is more important to a successful demolition contractor than a good safety program. Those companies that develop and maintain a culture of safe operations are usually the same companies that grow and succeed.
There are a number of real benefits that are gained by the demolition contactor when he or she promotes and maintains a good safety program, including:
• protecting employee health and safety promotes a better, more loyal workforce;
• safety measures for the protection of the public and property promotes a good public image;
• insurance rates are lower for contractors with good safety records;
• clients, both private and public, are more likely to seek proposals from contractors with a record of safe operations; and
• low incidents of accidents reduce delays to the project.
TOP-SHELF IDEAS |
Created in partnership with the National Demolition Association, “Demolition: Practices, Technology and Management” by Richard J. Diven and Mark Shaurette was published by Purdue University Press, West Lafayette, Ind., in 2010. ![]() The book’s promoters say it is “an invaluable reference resource for anyone involved in demolition projects, particularly students of construction management and engineering.” Topics covered in the book include a range of technical and management issues encountered by demolition contractors and those who hire them. Topics include modern demolition practices, the impact of different construction types, demolition regulations, estimating demolition work, demolition contracts, safety on the demolition project, typical demolition equipment, debris handling and recycling, use of explosives, demolition contractors’ participation in disaster response and demolition project management. According to a news release promoting the book, during the 1990s the number of contractors grew by nearly 60 percent, and there are now more than 800 companies in the United States focused on demolition, with others offering this service as part of their portfolio. The industry also has become more complex, requiring a combination of project management skills, legal and contractual knowledge and engineering skills. Co-author Richard J. Diven has nearly 40 years of experience in the demolition industry as a manager at structural demolition company ICONCO between 1964 and 2000 and then as founder of R. J. Diven Consulting LLC, Coeur d’ Alene, Idaho. Co-author Mark Shaurette is an assistant professor in building construction management at Purdue University, West Lafayette, Ind. He was previously president of Meridian Homes Inc. and a vice president at Ryan Homes, Reston, Va. Purdue University Press, founded in 1960, is the publishing arm of Purdue University. More information about “Demolition: Practices, Technology and Management,” including how to order it, can be found at www.demolitionassociation.com under the “Store” tab. |
In general, a demolition contractor with a good safety record is likely to be running all facets of his or her business in a responsible manner and has a better chance of being profitable.
THE ROLE OF OSHA
In 1970, the U.S. Congress passed the Occupational Health and Safety Act and created the Occupational Health and Safety Administration (OSHA), which operates as an agency of the Department of Labor.
OSHA, as it applies to the construction and demolition industries, is covered by the Code of Federal Regulation, CFR 1926, with demolition-specific standards set forth in CFR 1926.850, Subpart T, “Demolition.” The stated mission of the OSHA standards is to prevent work-related injuries, illnesses and deaths by issuing and enforcing workplace safety and health.
In 1981, the Department of Labor provided a grant to the National Association of Demolition Contractors (now known as the National Demolition Association, NDA) to prepare a safety manual dedicated to safe practice for the demolition industry.
Subsequent revisions were printed in 1989 and 2000. The NDA’s Demolition Safety Manual is recognized as one of the most comprehensive and user-friendly references for all demolition contractors who are dedicated to maintaining safe demolition practices for their projects.
In addition to a proper Engineering Survey, other standards in Subpart T require a competent person to conduct a continuous inspection as the demolition work progresses to detect hazards resulting from weakened or deteriorated floors, walls or loosened material. No employee is permitted to work where such hazards exist until they are corrected by shoring, bracing or other effective means. To comply with this standard, a competent person must be on each demolition project at all times.
EMPLOYEE TRAINING
OSHA addresses employee training and education in 29 CFR 1926.21, which is designed to cover all construction activities. In order for contractors to maintain a safe environment for their employees, it is critical that they understand the hazards of the project and comply with safe work practices.
The Project Specific Safety Plan along with a Task Hazard or Job Hazard Analysis is essential in identifying hazards and addressing their control measures. For example, if a contractor is going to demolish some obsolete chemical process equipment, it would be the contractor’s duty to ascertain the potential hazards in that work area.
This can be done by having the area surveyed by a competent person or people to see if there are hazards present and reviewing records of what has been done to mitigate residual hazards.
In addition to the potential hazards of dangerous residual material in the equipment, it is also necessary to determine the structural stability of the equipment and any supports that will be demolished as well as the need to de-energize the equipment and disconnect utilities. Once the hazards have been identified, the demolition contractor should communicate these potential dangers to employees and be assured that all personnel on the site understand how the work is to be accomplished in a safe manner.
OSHA offers 10- and 30-hour worker training in construction safety and 40-hour specific training for workers if hazardous materials are involved. The 40-hour courses are referred to as “Hazwoper Training.” Special training is also required for such tasks as the operation of forklifts, aerial lifts, fall protection and scaffold erection.
Some labor unions have extensive worker training that can be a real safety benefit for both the employees and the contractor. Demolition-specific safety training also is available from independent safety training companies.
Thorough training of the demolition contractor’s employees is an ongoing process. Safety-conscious contractors will continue to provide required general safety training. In addition, they will provide site-specific hazard training relative to the project-specific tasks being performed and verify that such training is being done on all jobsites.
Editor’s Note: The preceding text is an excerpt from Demolition: Practices, Technology and Management, the 2010 textbook published by Purdue University Press in cooperation with the National Demolition Association. Those interested in purchasing the book can do so at www.demolitionassociation.com
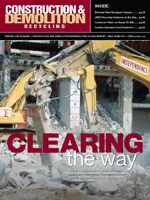
Explore the May 2011 Issue
Check out more from this issue and find your next story to read.
Latest from Construction & Demolition Recycling
- Michael Bros. announces leadership promotions
- Crush costs and lift output with Komatsu crushers
- Komatsu excavators made for demolition and recovery
- New Komatsu wheel loaders
- Trump copper tariff includes potential scrap export restrictions
- CDE publishes sustainability report
- AED opposes 'right to repair' language in federal bill
- UP reaches agreement to acquire Norfolk Southern