Replacing wear parts comes with the territory for grinder and shredder operators. Knowing when to replace those parts can vary from type of machine and type of material being processed. Whether it is a tip, a screen, teeth or hammers, being prepared can make all the difference and ensure that valuable time is not lost.
Tim Griffing, assistant engineer of design/stationary facilities at Newton, N.H.-based CBI says that determining a replacement schedule for wear parts is all relative to what is being shredded or size-reduced and the desired size of the end product.
“There is no rule of thumb,” he says. “When your progress goes down, your fuel consumption goes up.”
Tub grinders operate at a higher speed, which can cause some wear factors to be higher than that of a horizontal grinder, says Griffing. A 1,400 rpm rotor is going to go through parts much faster than a 700 rpm rotor, says Griffing.
“It is all visual inspection. You just have to check it,” remarks Griffing.
A VISUAL INSPECTION
A visual inspection is always going to offer the best indication of what parts are in need of replacement, according to several parts and equipment sellers.
David Whitelaw a Florida-based area sales manager for Komptech USA, Westminster, Colo., says standard operating procedure is to check wear parts morning, noon and night. Most good operators keep their eye on the steel bin or the pile under the magnet, he says. Operators will be able to tell when their wear parts hardware starts to arrive in the pile.
Lori Rheinberger, owner of Queen of Parts, Oregon City, Ore., has spent the last 15 years working providing grinder operators with replacement parts.
She says there are definite signs during operation that will indicate it is time to replace parts. If there is additional vibration emanating from the machine, that is a good indication. If tips are visibly worn on one side, then it is time to flip them or replace them.
A replacement schedule for wear parts is going to vary from machine to machine and will depend on what is being processed and how much the machine is being used. Tips can last around 40 hours, she says, although it can be difficult to establish a standard rule for replacing parts.
“Everybody is grinding something different,” says Rhein-berger. In places like Florida, for example, operators are grinding palm prongs. They are wet and gritty because they have a lot of sand in them. Wear will also vary from season to season. In the spring, wood will carry more moisture and sap than in the fall. Wear also is going to be different for an operator who is running clean, dry wood like pallets and two-by-fours through a grinder.
Grinding an abrasive material like asphalt shingles is also going to affect the life of parts. “Shingles are made of tar with a bunch of rocks stuck to it,” Whitelaw says. “They wear everything they touch from infeed chains and belting to discharge belt cleaners. In most high speed applications, tips and screen last 1-3 days.”
EXPECT THE UNEXPECTED
“Often there is a blowout or they will hit something and then they are down,” she says. This is why it is important, she says, to have a skilled operator who can watch out for unwanted material like metal being accidentally put into a shredder or grinder.
“A piece of rock or steel can do a lot of damage to a part. It comes down to having a really good operator to keep that material sorted and clean. The cleaner the material, the longer the parts will last,” she says.
TAKING STOCK
Unexpected incidents do occur, and the best advice Rheinberger says she can give is to keep spare parts on hand for those occasions. Also, when using a spare part, re-stock it right away, she recommends. “If you put a set of teeth on, make a phone call and order some parts,” Rhein-
berger says. She suggests keeping a $300 to $400 set of teeth on the shelf at all times.
Not stocking parts could mean a machine is down for days or even weeks while the part is being made and shipped.
Rheinberger admits that cash flow may not allow operators to keep five sets of teeth on the shelf, but keeping at least one spare set can be worthwhile. It outweighs the alternative of losing thousands of dollars per day from a machine being down.
“It is always nice to have some back-up on the shelf,” she says. “That way when you are broken down you are not down.”
“Screens should last three to six months if you don’t have a blowout and hit something dangerous,” she says. She suggests ordering a screen when it reaches its half-life or at the very least, two to three weeks before it is needed.
If an operator is grinding on a hectic schedule, Rheinberger suggests replacing hammers once per year.
Wayne Brown, owner and executive vice president of Grinder Wear Parts, with locations in Portland, Ore., and the Tampa Bay, Fla., area, notes that grinding is a very high wear environment. The most high wear areas are teeth or inserts and screens, the hammers that receive the teeth, and then the wear plates. On average, teeth can last as little as two hours and tips can last 40 hours, he estimates. But ultimately, the operator should know best. “The operator, after a period of use, will definitely know the average hours he should get for his environment,” says Brown.
WARNING SIGNS
“If the hammer face becomes smaller than the back of the tip it receives, then it is absolutely time to rework that hammer or replace it,” says Brown. If the tip does not fit 100 percent on the hammer then there is no question that the hammer should be reworked or replaced, he adds.
Usually, when the production goes down and the dimension of material that operators want to achieve is altered, it is time to replace a screen. Also, when the screen becomes so thin that it could fracture and cause damage to the machine, it is another indication that replacement is needed, says Brown.
“A lot of operators because they are so experienced in their environment and running their particular machine, they generally have set up their own reference point for when they would like to change screens,” says Brown. “It is a lot of hands-on experience that allows them to know when to change wear parts.”
Brown recommends keeping one or two sets of extra tips/inserts on hand and one or two sets of screens. Hammers, he says, are not as critical because they don’t need to be replaced as quickly (as a general rule). Brown still suggests keeping a spare set. Because of economic reasons, Brown finds that most customers tend not to order an extra set of hammers until they are needed.
“People are stocking less because of economic issues,” observes Brown. “They are relying on quick turnaround time in delivery of wear parts to them in a timely fashion.” Brown says that in general, Grinder Wear Parts has a 48-hour turnaround on its orders.
When all wear parts are new, Whitelaw says product consistency is perfect, but production actually decreases because the tolerances are so close with all new parts. “As the parts wear, production increases because of less resistance. But sooner or later the product starts to be out of spec, which means one or more of your wear parts needs to be changed,” he says.
GETTING THE MOST VALUE
Rheinberger offers some advice for getting the best value out of parts. Her first bit of advice is to shop around. She says it is usually good to work with more than one vendor in order to receive a fair price. She also says handy operators can sometimes do some welding to buy time with screens. Another point she makes is that operators do not have to replace a whole set of hammers at once, but can replace one or two at a time.
It can be costly to operate machinery, so a few dollars in savings can help, according to Rheinberger. One way she suggests saving on tips is to try to save on the tungsten carbide that is applied to a tip. Doing this could mean a $10 savings on a tip.
“At $2 per square inch, it is really important you use the right amount of tungsten. In this day and age, you don’t want any waste. You want to go out into your pile and see if you have any tungsten left on your machine,” she advises. “It could be the difference between a $15 dollar tip and a $25 dollar tip. You might be leaving $10 on the scrap pile that you don’t need. So I always start there when it comes to buying a part.”
Griffing offers additional pointers for buying parts. He points out that buyers should be aware of patent infringements and what kind of steel is being used. He says some parts sellers have poor steel quality while others have very good steel quality. “It is all about experience,” he says. “If you buy a tip from someone and it doesn’t last, then you won’t buy another tip from them.”
Brown warns that price is not always indicative of value. “It is very important to buy a quality product that is responsibly priced,” he says. A low priced wear part will quite often perform short term, but costs will be incurred substantially through labor costs and down time if the part does not last. “The benefit of buying something at a low price could end up costing more in the long run,” he adds.
Another recommendation from Brown includes making sure the parts are made from quality materials. Operators may either prefer tips and inserts that are forged or that are cast. “Quality of material used in the manufacturing of the parts is very important,” he adds.
But most importantly, says Brown are those daily inspections either every four or eigtht hours. “Inspection is really important to maintain the optimum performance of your machine,” he emphasizes.
![]() | The Garden Center Conference & Expo, presented by Garden Center magazine, is the leading event where garden retailers come together to learn from each other, get inspired and move the industry forward. Be sure to register by April 17 to get the lowest rates for the 2025 show in Kansas City, Missouri, Aug. 5-7.
|
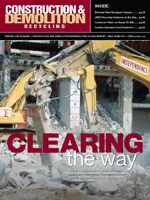
Explore the May 2011 Issue
Check out more from this issue and find your next story to read.
Latest from Construction & Demolition Recycling
- Cielo investor requests annual meeting
- CDE sets up washing plant on Long Island, NY
- NWRA: NIOSH cuts a step in the wrong direction
- Ferrous price hikes could be poised to pause
- Northstar secures 15-year lease extension for asphalt shingle recycling facility
- Greenwave asks for SEC filing extension
- Construction Plastics Initiative lines up projects
- ShearCore adds dealership group in Canada