The University of Wisconsin Oshkosh (UWO) is installing a biogas cogeneration plant that will divert a number of materials away from the landfill while also providing electrical power and heat to the campus.
A key technology provider for the new biogas system is Cenergy Power Systems Technologies Inc., Orange Park, Fla., which is owned in part by its management team and in part by Germany-based 2G Bio-Energietechnik AG.
Cenergy describes the combined heat and power (CHP) system being installed as “the first dry fermentation anaerobic bio-digester in the nation, which will convert yard and food waste into biogas.”
Michael J. Turwitt, the president and CEO of Cenergy, says the system at UWO and others like it will provide quick return-on-investment (ROI) for the corporations and institutions that install them, by providing energy internally without the monthly utility bill as well as by saving on waste hauling and disposal costs.
POWERFUL YET FLEXIBLE
According to Cenergy, another key technology provider to the UWO system is BIOFerm Energy Systems, Madison, Wis. In a press release, Cenergy refers to BIOFerm as “a leading expert that delivers a wide array of turnkey energy solutions using biomass and organic waste as the primary feed stock.”
Like Cenergy, BIOFerm has corporate roots in Germany, where BIOFerm GmbH is a member of the Viessmann Group holding company (www.viessmann.com), which makes and markets a variety of heating and energy systems.
The system that BIOFerm and Cenergy are installing in Oshkosh is being designed to supply both electricity and heat to the university campus. “In the beginning, approximately 10 to 15 percent of the entire energy consumed by the university will be [supplied] by the new plant,” says Turwitt.
A second phase is being planned that would increase that percentage, and during production spikes energy might be produced in amounts that would allow UWO to put excess energy onto the electrical grid.
“The 370 kWh (kilowatt-hours) biogas CHP cogeneration system . . . is expected to produce 4,183 megawatts (MWs) of thermal energy and 3,071 MW of electricity per year, to be utilized by the university campus, with any excess power sold to the grid,” notes the Cenergy news release.
INFORMED AUDIENCE |
The 2011 C&D Recycling Forum event is being planned so it will offer an update on the residuals-to-energy market, just as the 2010 version of the event did last October. The 2011 C&D Recycling Forum, the second rendition of the event, will take place Sept. 25-27, 2011 at the Turf Valley Resort & Conference Center in Ellicott City, Md. The event is organized by Recycling Today Media Group publication Construction & Demolition Recycling and is co-sponsored by the National Demolition Association and consulting firm Gershman, Brickner & Bratton Inc. (GBB). Programming offered is designed to focus on operational efficiency and maximizing recovered material value, with tie-ins to emerging energy markets a part of that focus in the case of several materials. ![]()
More information on the September 2011 event can be found at http://forum.cdrecycler.com/. |
According to Cenergy CEO Turwitt, when interviewed in mid-March, “The construction of the biogas anaerobic digester is almost finished [and] our biogas CHP cogeneration power plant has been shipped from the factory and will arrive in Oshkosh approximately April 18th.” He adds, “Installation of this 100 percent connection-ready modular power plant will only require a few days. As far as I know, UWO is planning a grand opening for the middle of May.”
In addition to touting installation of the modular equipment as relatively easy, Cenergy cites ease of maintenance as another advantage. “The plant is fully containerized and will be supplied as an ‘all-in-one’ and ‘connection-ready’ module. Benefits over conventional gas engines include much higher efficiency, reliability, durability, extended life, and less maintenance cost.
While the system may sound somewhat experimental to American ears, Turwitt says the technology has proven itself in Europe and other parts of the world. “This is the first dry anaerobic bio-digester plant in the United States, and the management of BIOFerm, as well as the University Executives at UWO, searched the market for the most reliable and proven biogas CHP cogeneration technology available,” he says.
The Cenergy 2G Optimus 370BG co-generation gas engine and the 2G biogas cogeneration technology package of which it is a component have been installed at more than 1,500 biogas plants in locations around the world, according to the company.
“When you invest millions of dollars in a biogas production facility, you don’t want to take chances when it comes to converting valuable biogas into electrical and thermal energy,” Turwitt continues. “For a project like this there is no room for trial and error, and the University of Wisconsin Oshkosh, with their partner BIOFerm, concluded that our technology is the most proven, reliable, and cost-effective solution.”
KEEPING IT FED
For the UWO alternative energy system to offer the best returns, it will require a steady diet of yard trimmings, food scrap and other organic materials that can be used as biomass fuel.
The anaerobic bio-digester will convert yard and food waste into biogas, with many types of material—as long as it consists of 25 percent solids or higher—being potential feedstock.
On its website (www.biofermenergy.com/us), BIOFerm lists “communities, industrial operations, agricultural centers and waste management organizations” as potential suppliers of material for its bio-digestion systems.
“Kitchen scraps, yard waste, food processing waste and agricultural waste from farms” are listed as ideal organic inputs for the anaerobic process.
Sponsored Content
The 1200-CC, Enhanced With New Features
Eagle Crusher’s most popular plant is enhanced with new features to make setup, operation, and transport a breeze. New features include a redesigned return conveyor; a new fully hydraulic side discharge conveyor, a self-lowering control panel, and an available onboard cross-belt permanent magnet that stays on for transport.
That process converts trapped carbon into energy and yields a compost-type end product. “The overall volume of waste put into a BIOFerm plant is greatly reduced through the dry fermentation process,” says the company. “Only 60 percent of the volume of what goes in is left over after the 28-day cycle. The organic material remaining after a complete dry fermentation cycle is the equivalent of advanced stage compost [and] can be further processed and sold for commercial or private use,” the company claims.
By using feedstocks that have largely been considered waste and that are perceived as readily available along with the production of (increasingly expensive) electricity or heat that will not have to be purchased, Turwitt says the ROI on such systems is easy to demonstrate.
Corporations and investment groups have been far quicker to conduct ROI analyses and purchase systems, says Turwitt. “Most of our power plants are purchased by private entities (companies, investment groups, and private project planners/contractors),” he adds.
TERMINATION CLAUSE |
![]()
Among the equipment makers ensuring current and potential customers that they recognize the importance of emerging energy markets is Austria’s Komptech, which operates a North American office in Westminster, Colo. At the 2011 WasteExpo, taking place May 10-12 in Dallas, Komptech USA says it will again be showing its technology for recycling and waste-to-energy markets. |
Turwitt lists “landfill, solid waste management, agricultural businesses, dairy farming, food processing, waste water treatment companies, industrial groups, mining industry, electrical utilities [and] private power producers” as sectors making these investments.
These investors determine that “the ROI is generally excellent,” says Turwitt. “Depending on the type of project, the return is fast. Our systems usually pay off after as little as three to four years.”
Should investors continue to reach this conclusion, the solid waste and recycling industries are among those who will likely be asked to supply the feedstock to keep the lights on and the inside temperature at the proper level at these locations.
Get curated news on YOUR industry.
Enter your email to receive our newsletters.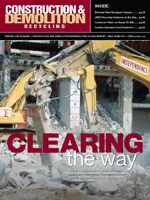
Explore the May 2011 Issue
Check out more from this issue and find your next story to read.
Latest from Construction & Demolition Recycling
- Cielo investor requests annual meeting
- CDE sets up washing plant on Long Island, NY
- NWRA: NIOSH cuts a step in the wrong direction
- Ferrous price hikes could be poised to pause
- Northstar secures 15-year lease extension for asphalt shingle recycling facility
- Greenwave asks for SEC filing extension
- Construction Plastics Initiative lines up projects
- ShearCore adds dealership group in Canada