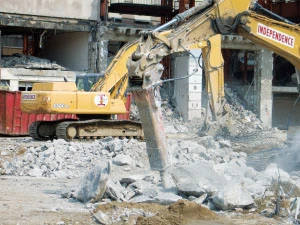
One of the largest construction projects currently in progress in the U.S. is the $465 million Cleveland Medical Mart & Convention Center (MMCC) in downtown Cleveland. Once complete, the facility will consist of a four-story above-ground medical mart on the corner of St. Clair and Ontario Streets as well as a 230,000-square-foot underground convention center with 60,000 square feet of meeting rooms and a 32,000-square-foot grand ballroom. Health care providers, medical device manufacturers, health care educational institutions and health care IT companies will be among the 88 tenants already signed up to locate in the new space.
The project, being managed by MPPI, is working to obtain LEED (Leadership in Energy and Environmental Design) Silver certification from the U.S. Green Building Council. MPPI (Merchandise Mart Properties Inc., Chicago) is no stranger to LEED projects. The company says it completed the largest LEED Silver project in the world at the Merchandise Mart in Chicago.
BRINGING IT DOWN
To make way for the 1 million-square-foot facility, five buildings needed to be demolished. They included a parking garage, Sportsmans Restaurant, the Court Annex Building, the Chicago Title Building and the 113 Building – an 8-story building in the center of a business district. The demolition schedule has been aggressive, according to several parties involved in the project.
The timetable called for demolition to begin Jan. 3, 2011, and at 6 a.m. that day engines started up and shears started crunching right on schedule. Despite the wind, cold, snow and rain that are typical of Cleveland in the winter and spring, demolition has stayed on schedule without a day of work being missed, say the companies involved.
Not only did five buildings need to be demolished above the ground, but much of the demolition has taken place below the ground at the Cleveland Convention Center, Malls B and C and Exhibit Halls C and D on Lakeside Avenue. This phase of the demolition is nearing completion and involves a large volume of concrete.
“The Cleveland Convention Center was basically a gigantic concrete bathtub on top of which was the Cleveland mall,” says Dave Johnson of MMCC.
First, crews scraped off the top of the mall, which consisted of grass, dirt, sidewalks and trees. Once that was done, crews demolished within the building itself, taking down column upon column, removing the old flooring and gutting the building. The Public Auditorium connector also is nearly demolished and a new Public Auditorium switchgear room is more than half completed, including new conduit runs, studs, drywall, painting and equipment installation.
GOING FOR SILVER
Independence Excavating, Independence, Ohio, is handling the demolition. To meet LEED requirements, 95 percent of the demolition materials are being recycled. Doug Thomas, project manager with Independence Excavating, says most of the ongoing work is removing concrete that is being crushed to an aggregate at nearby crushing facilities.
The MMCC will use 20 to 25 percent of the crushed concrete on site for stone fill, sidewalk and roadway bedding materials. The remaining 75 to 80 percent of the material will be used for other local projects – ones that Clevelanders are well aware of, such as work being done in the near-downtown neighborhood known as The Flats and the replacement of an interstate highway bridge. Thomas says 100 percent of the soil is being re-used on other projects in Northeast Ohio, including the aforementioned projects.
GOING GREENER FROM SEVERAL ANGLES |
Recycling 95 percent of demolition debris isn’t the only sustainability initiative the Cleveland Medical Mart & Convention Center (MMCC) will implement into its design. Following are some of the ways the facility will reduce its environmental impact: |
In addition to concrete, steel, aluminum, copper, reinforcing steel, brick, block, wood, gypsum, asphalt, plastic, cardboard and paper are all being recycled to help meet the 95 percent recycling goal. Kurtz Brothers in nearby Valley View, Ohio, is screening and sorting the mixed C&D material.
The plan includes recovering 190,000 cubic yards of dirt and topsoil and 124,000 cubic yards of recyclable materials, leaving 6,000 yards of waste. Thomas is optimistic his crew can keep waste below 6,000 cubic yards, achieving a recycling rate that exceeds the 95 percent goal. With about 80 percent of the demolition complete, an estimated 95,000 cubic yards of material have been recycled.
Demolition should be finished in May of 2011. “Right now, we are basically down to the floor level of the existing convention center,” said Independence Excavating’s Ed Wilk, project general superintendent, during a mid-April visit.
Wilk says he has been involved in many construction projects in downtown Cleveland but not of this scale. “Working in downtown Cleveland is always a challenge because the rest of the world is trying to go on while you are trying to build a building,” he comments.
ORGANIZED CHAOS
Commotion has resulted during the last several months, as heavy machinery has taken up residence in the center of the city. Wilk estimates that nearly 30 to 40 trucks are hauling materials out each day. At the peak of the demolition, an estimated 100 trucks per day were hauling material from the site to be recycled.
Thomas describes the work site as “organized chaos.” There is quite a bit of activity going on, with trucks moving in and out, skid-steer loaders hauling material and larger excavators prying away at the existing structures. But for those in the know, it is orderly. Concrete goes into one pile, structural steel into another, masonry material that will be turned into mulch goes into yet another pile.
Independence Excavating has an estimated 40 employees working at the site in addition to 100 other contractors. Johnson has been pleased with the job the demolition workers have performed. “The crews did a terrific job in terms of a safe and quick demolition project. This is an enormous project,” he says.
Van Auken Akins Architects LLC, Cleveland, has held LEED workshops with the design, architectural and construction teams. These include monthly LEED progress meetings and regular on-site inspections.
Seattle-based LMN Architects, along with Gustafson Guthrie Nichol, also based in Seattle, created conceptual plans and design development drawings as the design architects. The Cleveland office of Turner Construction Co. is the design-build contractor, and the Cleveland office of San Francisco-based URS Corp. is the architect. Construction of the MMCC is expected to be complete in the fall of 2013.
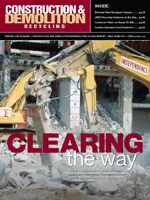
Explore the May 2011 Issue
Check out more from this issue and find your next story to read.
Latest from Construction & Demolition Recycling
- Mazza Recycling adds to transfer station operations
- Michigan awards $5.6M in recycling, waste reduction grants
- Pittsburgh area mall headed for demolition
- RMDAS figures show February surge in recycled steel’s value
- US economic indicators show signs of wavering
- Northstar signs asphalt shingle supply agreement with York1
- Metso’s Lokotrack line turns 40
- Takeuchi adds dealer in Mississippi